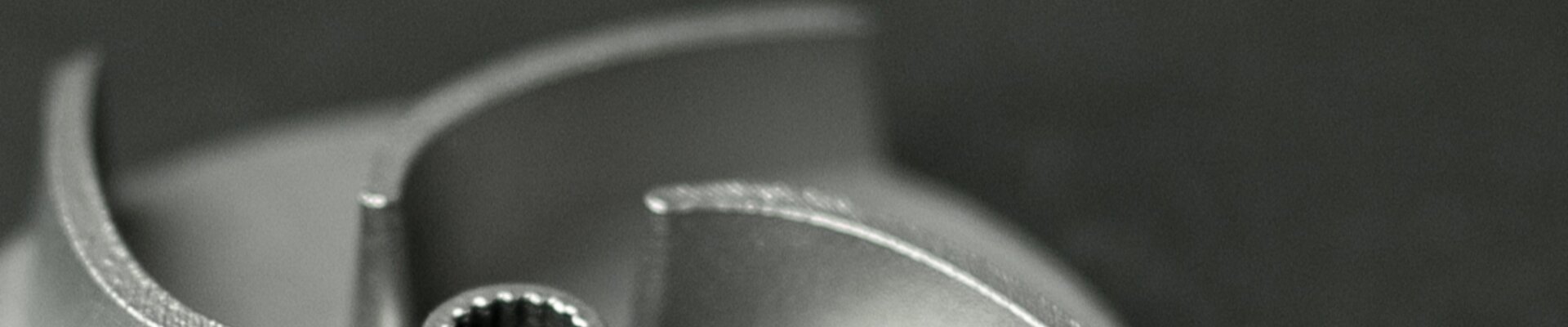
EOS StainlessSteel 254
Material Data Sheet
EOS StainlessSteel 254
EOS StainlessSteel 254 is an austenitic stainless steel for extreme conditions. The high chromium, molybdenum and nitrogen alloying give excellent corrosion resistance in many difficult environments. The general pitting resistance equivalent PREN for 254 is 43 (PREN = %Cr + 3.3 X %Mo + 16 X %N).
- Excellent resistance to uniform, pitting and crevice corrosion
- High resistance to stress corrosion cracking
- Higher strength than conventional austenitic stainless steels
- Chlorinated seawater handling equipment
- Pulp and paper manufacturing devices
- Chemical handling equipment
The EOS Quality Triangle
EOS incorporates these TRLs into the following two categories:
- Premium products (TRL 7-9): offer highly validated data, proven capability and reproducible part properties.
- Core products (TRL 3 and 5): enable early customer access to newest technology still under development and are therefore less mature with less data.
All of the data stated in this material data sheet is produced according to EOS Quality Management System and international standards
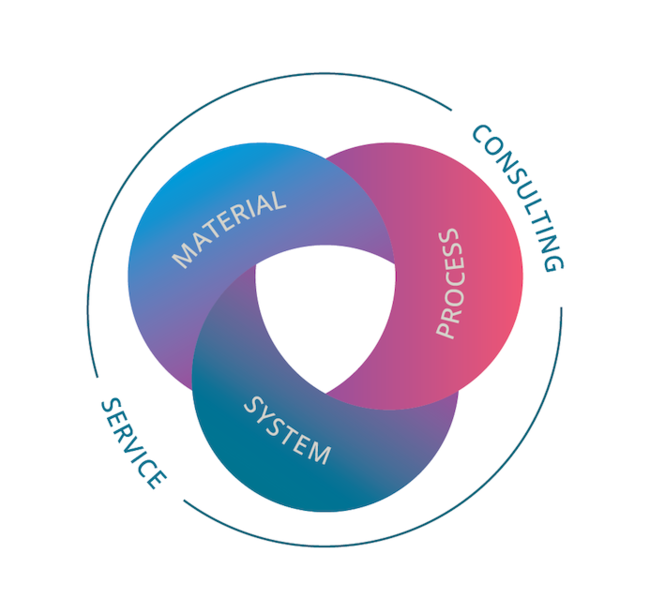
POWDER PROPERTIES
EOS StainlessSteel 254 powder material is in accordance with DIN EN 10088-3, EN 1.4547
Powder Chemical Composition (wt.-%)
Element | Min. | Max. |
---|---|---|
Cr | 19.5 | 20.5 |
Ni | 17.5 | 18.5 |
Mo | 6.0 | 7.0 |
Cu | 0.5 | 1.0 |
N | 0.18 | 0.25 |
Powder Particle Size
GENERIC PARTICLE SIZE DISTRIBUTION | 20 - 65 μm |
---|
HEAT TREATMENT
Heat treatment procedure
Optional solution annealing: At 1180 °C for 2 h after parts have fully heated through, water quenching Typical dimensional change after heat treatment: 0.06 %
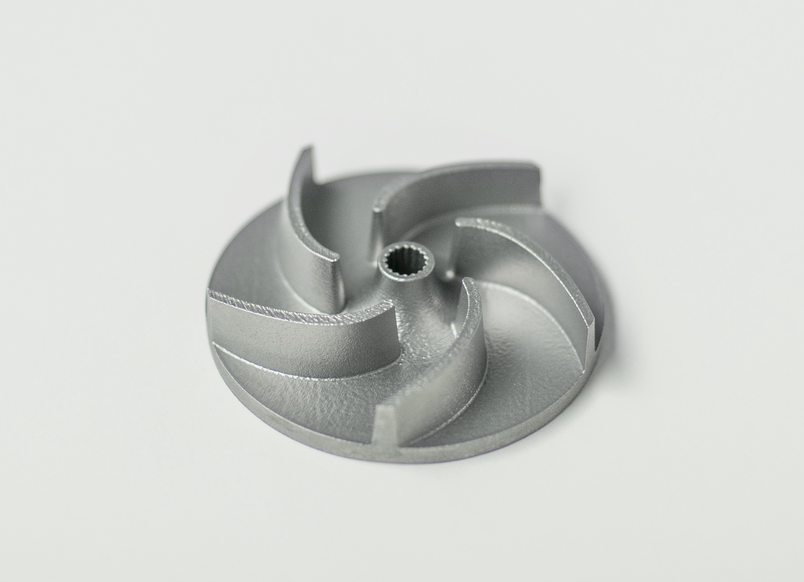
EOS StainlessSteel 254 for EOS M 290 | 40 µm
EOS M 290 - 40 µm - TRL 3
System Setup | EOS M 290 |
---|---|
EOS Material set | 254_040_CoreM291_100 |
Software Requirements |
EOSPRINT 2.8 or newer EOSYSTEM 5.20 or newer |
Recoater Blade | HSS (High Speed Steel) |
Nozzle | EOS Grid Nozzle |
Inert gas | Argon |
Sieve | 75 µm |
Additional Information | |
---|---|
Layer Thickness | 40 µm |
Volume Rate | 4.1 mm³/s |
Chemical and Physical Properties of Parts
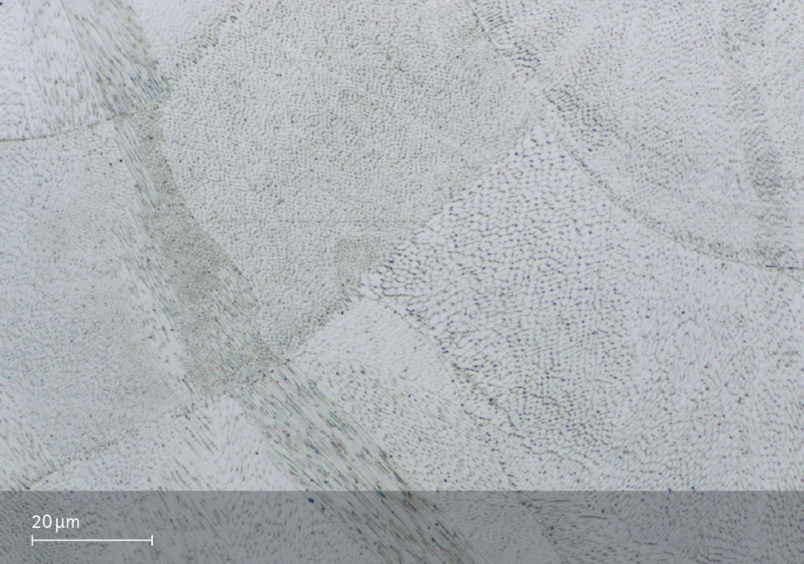
Microstructure of the Produced Parts
Defects | Thickness | Result | Number of Samples |
---|---|---|---|
Average Defect Percentage | 40 µm | 0.01 % | - |
Density EN ISO 3369 | Thickness | Result | Number of Samples |
---|---|---|---|
Average Density | 40 µm | ≥ 8.07 g/cm³ | - |
Mechanical Properties
Mechanical Properties Heat Treated
EN ISO 6892-1 Room Temperature | Yield Strength [MPa] | Tensile Strength [MPa] | Elongation at Break [%] | Reduction of Area Z [%] | Number of Samples | |
---|---|---|---|---|---|---|
Vertical | 360 | 660 | 48 | - | - | - |
Horizontal | 360 | 700 | 43 | - | - | - |
Optional solution annealing
At 1 180 °C for 2 h after parts have fully heated through, water quenching
Typical dimensional change after heat treatment: 0.06 %
Mechanical Properties As Manufactured
EN ISO 6892-1 Room Temperature | Yield Strength [MPa] | Tensile Strength [MPa] | Elongation at Break [%] | Reduction of Area Z [%] | Number of Samples | |
---|---|---|---|---|---|---|
Vertical | 600 | 720 | 35 | - | - | - |
Horizontal | 680 | 810 | 29 | - | - | - |
Surface Roughness
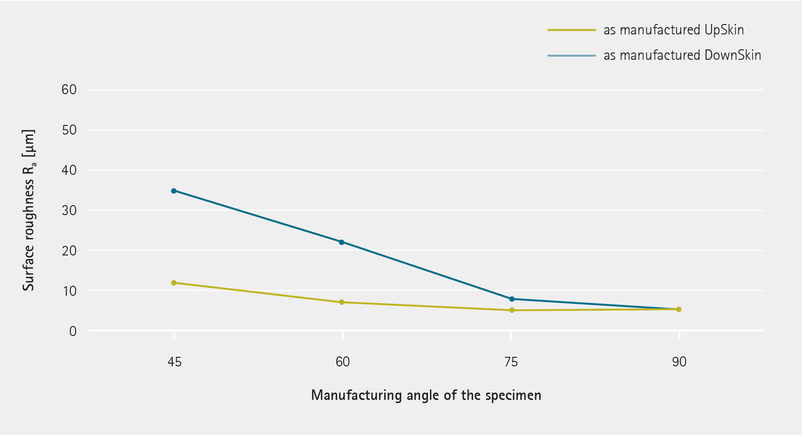
Coefficient of Thermal Expansion
ASTM E228 | Temperature |
---|---|
14.8*10-6/K | 25 – 100 ºC |
15.7*10-6/K | 25 – 200 ºC |
16.3*10-6/K | 25 – 300 ºC |
16.7*10-6/K | 25 – 400 ºC |
EOS StainlessSteel 254 for EOS M 290 | 60 µm
EOS M 290 - 60 µm - TRL 3
System Setup | EOS M 290 |
---|---|
EOS Material set | 254_060_CoreM291_100 |
Software Requirements |
EOSPRINT 2.8 or newer EOSYSTEM 5.20 or newer |
Recoater Blade | HSS (High Speed Steel) |
Nozzle | EOS Grid Nozzle |
Inert gas | Argon |
Sieve | 75 µm |
Additional Information | |
---|---|
Layer Thickness | 60 µm |
Volume Rate | 6.1 mm³/s |
Chemical and Physical Properties of Parts
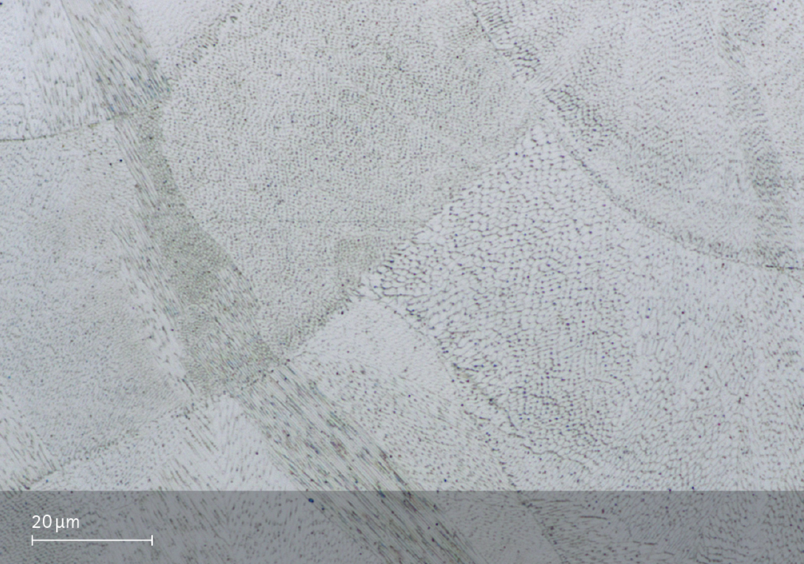
Microstructure of the Produced Parts
Defects | Thickness | Result | Number of Samples |
---|---|---|---|
Average Defect Percentage | 60 µm | 0.02 % | - |
Density EN ISO 3369 | Thickness | Result | Number of Samples |
---|---|---|---|
Average Density | 60 µm | ≥ 8.07 g/cm³ | - |
Mechanical Properties
Mechanical Properties Heat Treated
EN ISO 6892-1 Room Temperature | Yield Strength [MPa] | Tensile Strength [MPa] | Elongation at Break [%] | Reduction of Area Z [%] | Number of Samples | |
---|---|---|---|---|---|---|
Vertical | 360 | 660 | 48 | - | - | - |
Horizontal | 360 | 700 | 44 | - | - | - |
Optional solution annealing
At 1 180 °C for 2 h after parts have fully heated through, water quenching.
Typical dimensional change after heat treatment: 0.06 %
Mechanical Properties As Manufactured
EN ISO 6892-1 Room Temperature | Yield Strength [MPa] | Tensile Strength [MPa] | Elongation at Break [%] | Reduction of Area Z [%] | Number of Samples | |
---|---|---|---|---|---|---|
Vertical | 580 | 730 | 36 | - | - | - |
Horizontal | 660 | 800 | 30 | - | - | - |
Surface Roughness
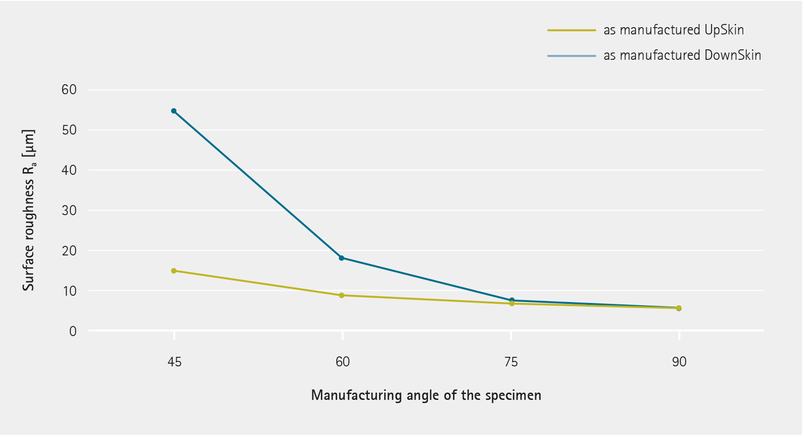
Coefficient of Thermal Expansion
ASTM E228 | Temperature |
---|---|
14.8*10-6/K | 25 – 100 ºC |
15.7*10-6/K | 25 – 200 ºC |
16.3*10-6/K | 25 – 300 ºC |
16.7*10-6/K | 25 – 400 ºC |