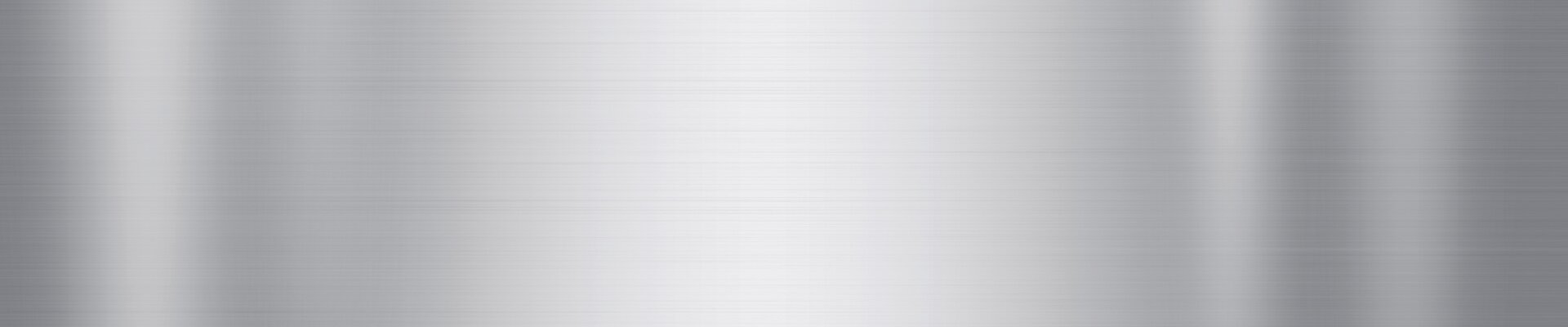
EOS StainlessSteel PH1
Material Data Sheet
EOS StainlessSteel PH1
EOS StainlessSteel PH1 is a pre-alloyed stainless steel in fine powder form. The chemistry of EOS StainlessSteel PH1 conforms to the compositions of DIN 1.4540 and UNS S15500. This kind of steel is characterized by having good corrosion resistance and excellent mechanical properties, especially in the precipitation hardened state. This type of steel is widely used in variety of engineering applications requiring high hardness, strength and corrosion resistance. This material is ideal for many part-building applications (DirectPart) such as functional metal prototypes, small series products, individualised products or spare parts. Standard processing parameters use full melting of the entire geometry with 20 µm layer thickness. Using standard parameters the mechanical properties are fairly uniform in all directions. Parts made from EOS StainlessSteel PH1 can be machined, spark-eroded, welded, micro shot-peened, polished and coated if required.
- High strength and hardness
- Corrosion resistant
- For mildly corrosive environments
- Engineering applications including functional prototypes, small series products, individualised products or spare parts
- Parts requiring high corrosion resistance, sterilisability, etc.
- Parts requiring particularly high hardness and strength
The EOS Quality Triangle
EOS incorporates these TRLs into the following two categories:
- Premium products (TRL 7-9): offer highly validated data, proven capability and reproducible part properties.
- Core products (TRL 3 and 5): enable early customer access to newest technology still under development and are therefore less mature with less data.
All of the data stated in this material data sheet is produced according to EOS Quality Management System and international standards
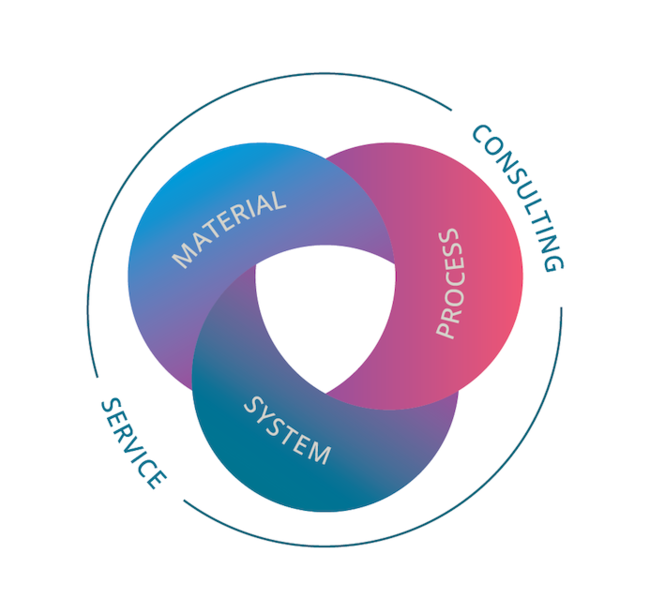
POWDER PROPERTIES
The chemistry of EOS StainlessSteel PH1 conforms to the compositions of DIN 1.4540 and UNS S15500.
Powder Chemical Composition (wt.-%)
Element | Min. | Max. |
---|---|---|
Cr | 14.0 | 15.5 |
Ni | 3.5 | 5.5 |
Cu | 2.5 | 4.5 |
Mn | 0.0 | 1.0 |
Si | 0.0 | 1.0 |
C | 0.0 | 0.07 |
Mo | 0.0 | 0.5 |
Nb | 0.15 | 0.45 |
Powder Particle Size
GENERIC PARTICLE SIZE DISTRIBUTION | 20 - 65 μm |
---|
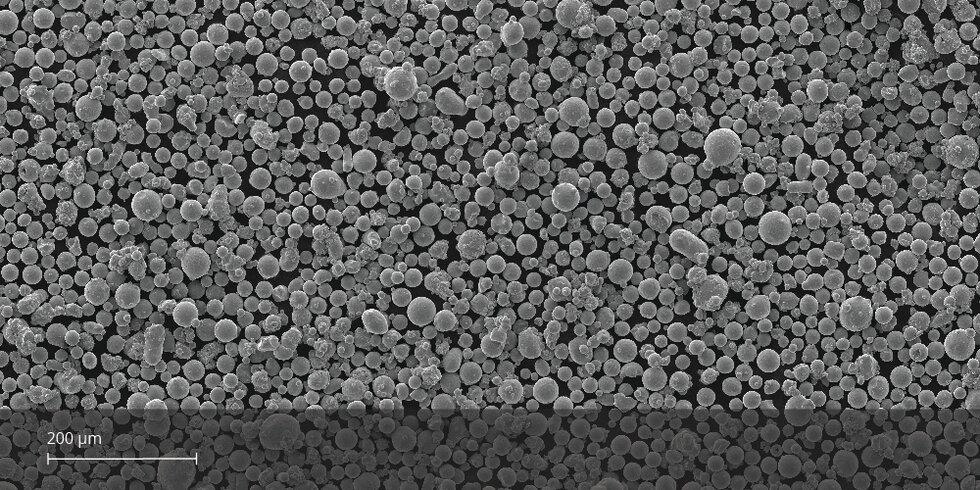
HEAT TREATMENT
Hardening of EOS StainlessSteel PH1 done using modified H900 heat treatment
Soaking time at precipitation hardening temperature 525°C elongated for 4 hours
EOS StainlessSteel PH1 for EOS M 290 | 40/80 µm
EOS M 290 - 40 µm - TRL 3
Process Information Metal
This process product is optimized for flexible and fast production of PH1 parts with EOS M 290 and M 400-4 systems. The parameter set has three different layer thickness options that can all be utilized within the same build: 40µm, 80 µm and 40/80 µm Skin. For high productivity needs a 80 µm parameter set is included with a build rate more than double the long established 40 µm parameter set. Both can be used separately for different parts or combined by using 40/80 µm Skin with faster 80 µm for the core of the part and higher quality 40 µm building for the surface of the part with defined thickness. Sectionioning parts in vertical direction for different parameters is also possible.
System Setup | EOS M 290 |
---|---|
EOS Material set | PH1_040_080_Core M291 |
Software Requirements |
EOSPRINT 2.11 or newer |
Recoater Blade | Ceramic |
Nozzle | EOS Grid Nozzle |
Inert gas | Nitrogen |
Sieve | 63 µm |
Additional Information | |
---|---|
Layer Thickness | 40/80 µm |
Volume Rate | 4.1-7.9 mm³/s |
Typical Dimensional Change after HT [%] | +0.1 % |
Chemical and Physical Properties of Parts
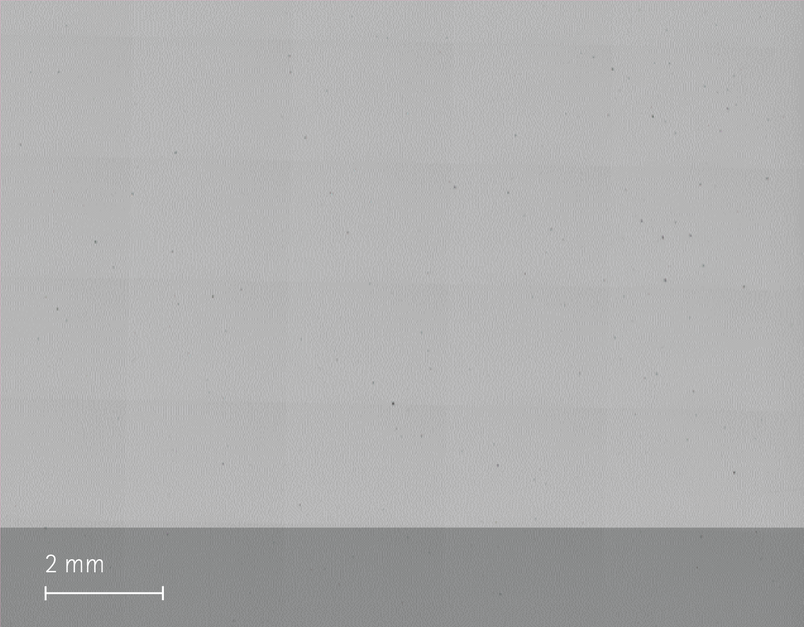
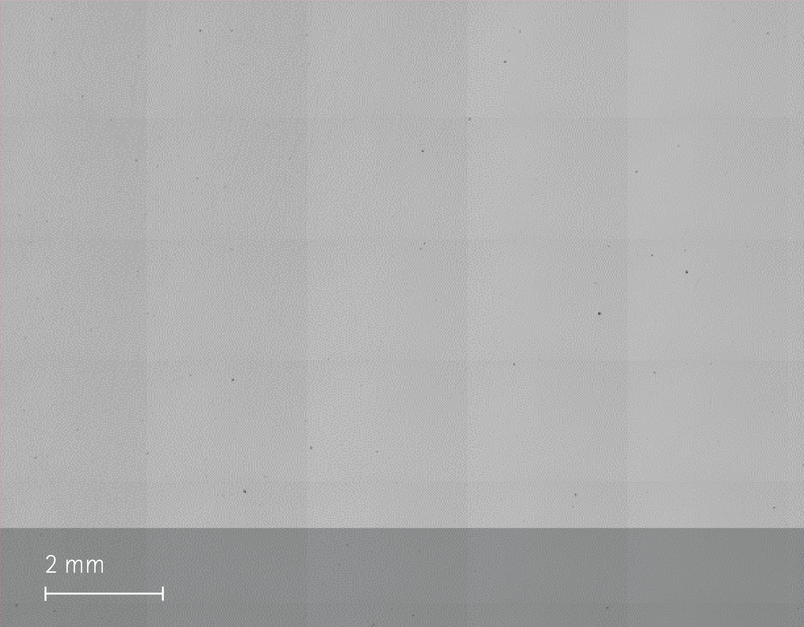
Microstructure of the Produced Parts
Defects | Thickness | Result | Number of Samples |
---|---|---|---|
Average Defect Percentage | 40 µm | <0.1 % | - |
Average Defect Percentage | 80 µm | <0.2 % | - |
Mechanical Properties
Mechanical Properties Heat Treated
EN ISO 6892-1 Room Temperature | Yield Strength [MPa] | Tensile Strength [MPa] | Elongation at Break [%] | Reduction of Area Z [%] | Number of Samples | |
---|---|---|---|---|---|---|
Vertical | 1305 | 1440 | 8 | - | - | - |
Horizontal | 1300 | 1450 | 10 | - | - | - |
H900 heat treatment
Mechanical Properties Heat Treated
EN ISO 6892-1 Room Temperature | Yield Strength [MPa] | Tensile Strength [MPa] | Elongation at Break [%] | Reduction of Area Z [%] | Number of Samples | |
---|---|---|---|---|---|---|
Vertical | 1310 | 1440 | 7 | - | - | - |
Horizontal | 1310 | 1460 | 10 | - | - | - |
H900 heat treatment
Impact Toughness
EN ISO 148-1, Charpy-V Heat Treated | |
---|---|
Typical Impact Toughness [J] | 8 |
Layer Thickness | 40 µm |
H900 heat treatment
EN ISO 148-1, Charpy-V Heat Treated | |
---|---|
Typical Impact Toughness [J] | 6 |
Layer Thickness | 80 µm |
H900 heat treatment
Surface Roughness
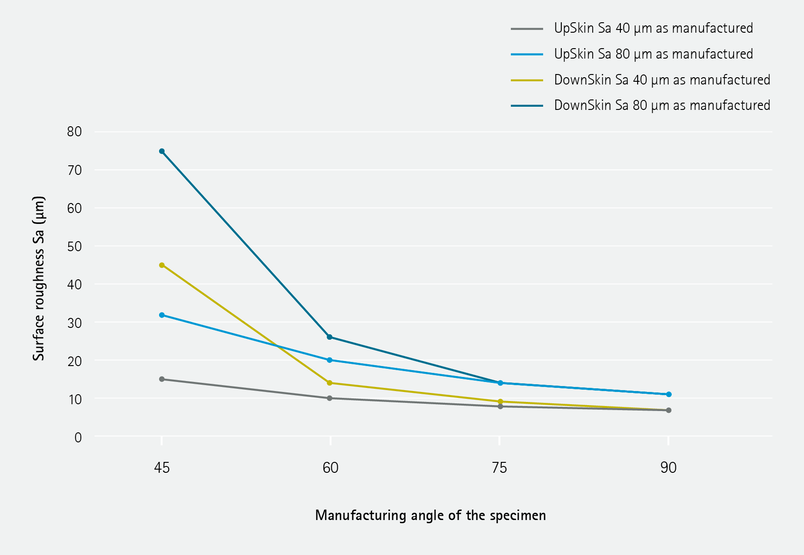
EOS StainlessSteel PH1 for EOS M 400-4 | 40/80 µm
EOS M 400-4 - 40 µm - TRL 3
Process Information Metal
This process product is optimized for flexible and fast production of PH1 parts with EOS M 400-4 system. The parameter set has three different layer thickness options that can all be utilized within the same build: 40µm, 80 µm and 40/80 µm Skin. For high productivity needs a 80 µm parameter set is included with a build rate more than double the long established 40 µm parameter set. Both can be used separately for different parts or combined by using 40/80 µm Skin with faster 80 µm for the core of the part and higher quality 40 µm building for the surface of the part with defined thickness. Sectionioning parts in vertical direction for different parameters is also possible.
System Setup | EOS M 400-4 |
---|---|
EOS Material set | PH1_040_080_Core M404 |
Software Requirements |
EOSPRINT 2.11 or newer |
Recoater Blade | Ceramic |
Inert gas | Nitrogen |
Sieve | 63 µm |
Additional Information | |
---|---|
Layer Thickness | 40/80 µm |
Volume Rate | 4.1-7.9 mm³/s |
Typical Dimensional Change after HT [%] | +0.1 % |
Chemical and Physical Properties of Parts
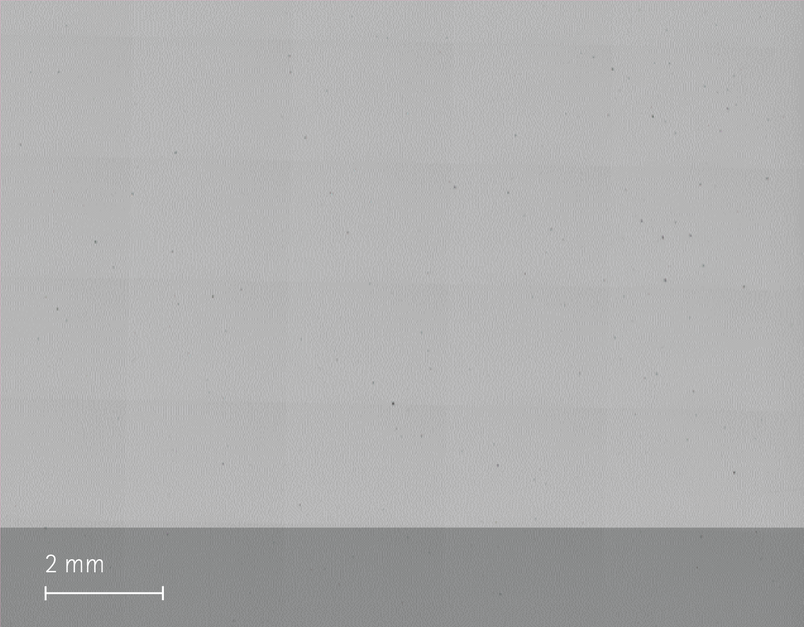
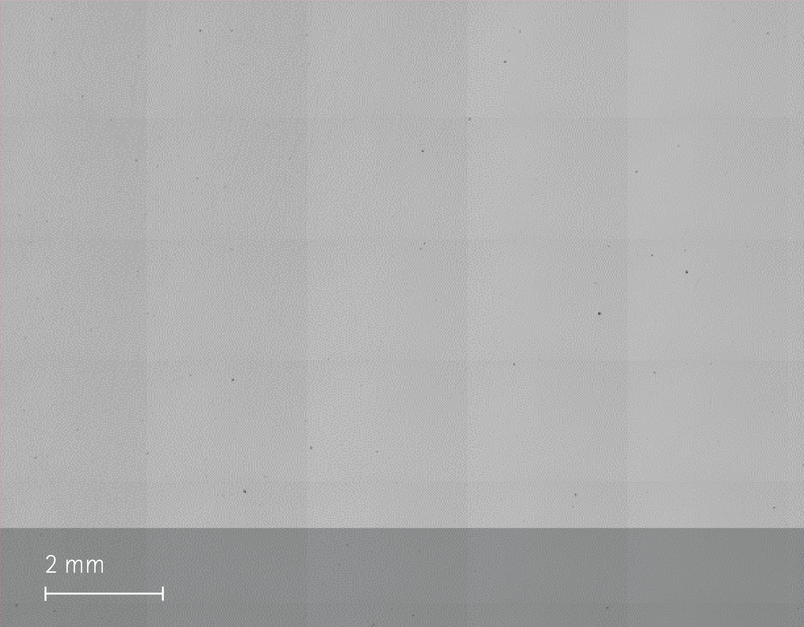
Microstructure of the Produced Parts
Defects | Thickness | Result | Number of Samples |
---|---|---|---|
Average Defect Percentage | 40 µm | <0.1 % | - |
Average Defect Percentage | 80 µm | <0.2 % | - |
Mechanical Properties
Mechanical Properties Heat Treated
EN ISO 6892-1 Room Temperature | Yield Strength [MPa] | Tensile Strength [MPa] | Elongation at Break [%] | Reduction of Area Z [%] | Number of Samples | |
---|---|---|---|---|---|---|
Vertical | 1290 | 1430 | 8 | - | - | - |
Horizontal | 1330 | 1450 | 8 | - | - | - |
H900 heat treatment
Mechanical Properties Heat Treated
EN ISO 6892-1 Room Temperature | Yield Strength [MPa] | Tensile Strength [MPa] | Elongation at Break [%] | Reduction of Area Z [%] | Number of Samples | |
---|---|---|---|---|---|---|
Vertical | 1305 | 1440 | 7 | - | - | - |
Horizontal | 1320 | 1460 | 7 | - | - | - |
H900 heat treatment
Impact Toughness
EN ISO 148-1, Charpy-V Heat Treated | |
---|---|
Typical Impact Toughness [J] | 8 |
Layer Thickness | 40 µm |
H900 heat treatment
EN ISO 148-1, Charpy-V Heat Treated | |
---|---|
Typical Impact Toughness [J] | 6 |
Layer Thickness | 80 µm |
H900 heat treatment
Surface Roughness
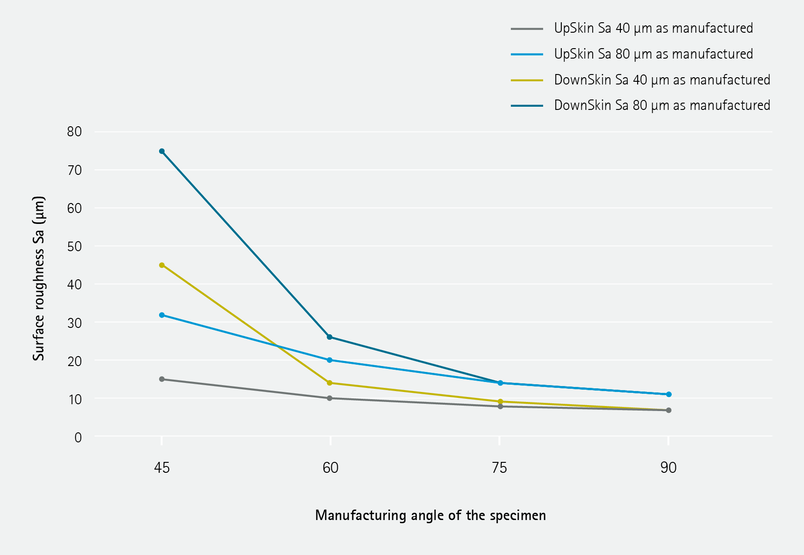