EOS ToolSteel 1.2709 for EOS M 290 | 40 µm
EOS M 290 - 40 µm - TRL 7
System Setup | EOS M 290 |
---|---|
EOS Material set | 1.2709_040_HiPerM291_1.00 |
Software Requirements |
EOSPRINT 2.7 or newer |
Recoater Blade | Ceramic |
Nozzle | EOS Grid Nozzle |
Inert gas | Argon |
Sieve | 75 µm |
Additional Information | |
---|---|
Layer Thickness | 40 µm |
Volume Rate | 4.1 mm³/s |
Typical Dimensional Change after HT [%] | + 0.1 % |
Chemical and Physical Properties of Parts
Chemical composition of built parts is compliant to EOS ToolSteel 1.2709 powder chemical composition.
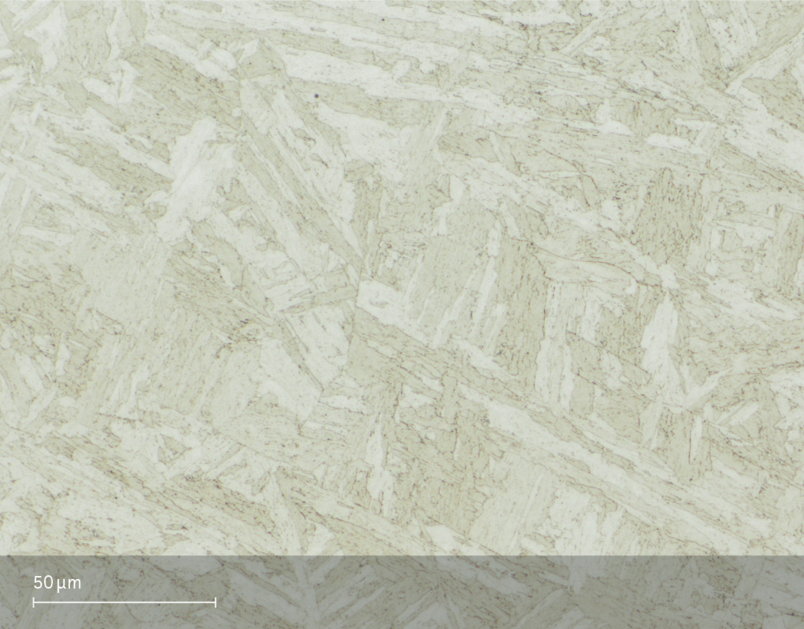
Microstructure of the Produced Parts
Defects | Thickness | Result | Number of Samples |
---|---|---|---|
Average Defect Percentage | 40 µm | 0.03 % | 55 |
Density EN ISO 3369 | Thickness | Result | Number of Samples |
---|---|---|---|
Average Density | 60 µm | > 8.05 g/cm³ | 20 |
Mechanical Properties
Mechanical Properties Heat Treated
EN ISO 6892-1 Room Temperature | 60 µm | Yield Strength [MPa] | Tensile Strength [MPa] | Elongation at Break [%] | Reduction of Area Z [%] | Modulus of elasticity [GPa] | Number of Samples |
---|---|---|---|---|---|---|
Vertical | 2180 | 2260 | 3.3 | - | - | 188 |
Horizontal | 2170 | 2250 | 4.2 | - | - | 162 |
EOS ToolSteel 1.2709 can be heat treated to match various needs of different applications. The two step heat treatment can be performed under vacuum or inert gas atmosphere. First step is solution annealing to minimize amount of austenite in the martensitic matrix. The needed hardness and strength is achieved through aging treatment where hardening takes place through forming of intermetallic phases and precipitates.
Solution Annealing: 2 h at 940 °C (±10 °C) measured from the part followed by rapid air cooling to room temperature (below 32 °C). Cooling rate 10-60 °C/min. Reaching room temperature before starting aging treatment is required to achieve desired microstructure.
Aging: For peak hardness and strength 3-6 h at 510 °C (±10 °C) measured from the part followed by air cooling. Mechanical properties presented in this document achieved through this aging procedure. For bulky parts ensure uniformity of properties by increasing hold time up to 6 h. Also, to maximize fatigue strength, a hold time of 6 h is recommended.
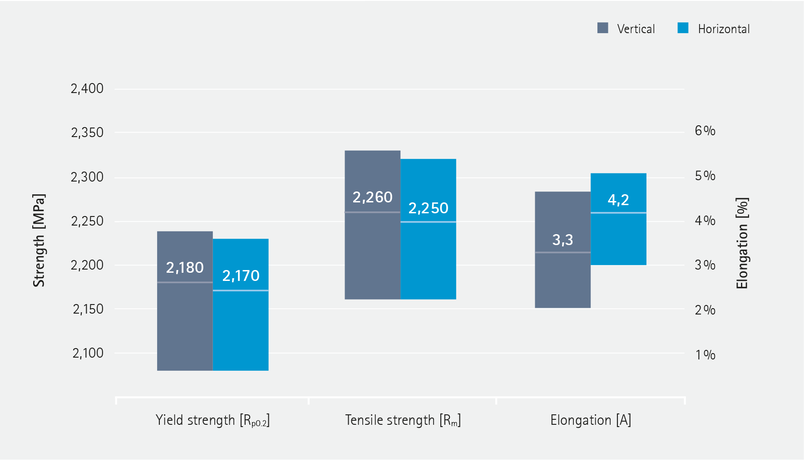
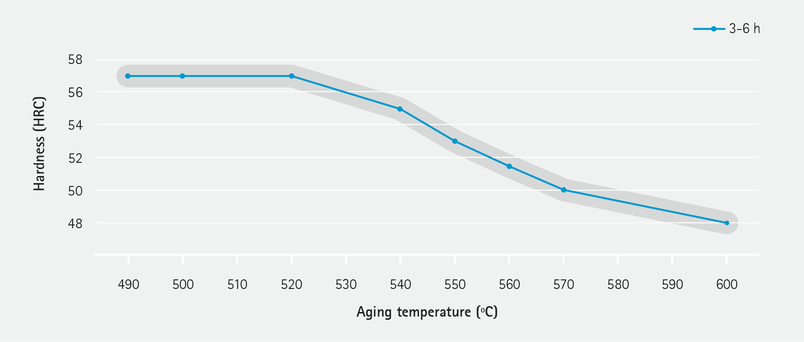
Hardness
EN ISO 6508 Heat Treated | |
---|---|
Value | 57 |
Unit | HRC |
Impact Toughness
EN ISO 148-1, Charpy-V Heat Treated | |
---|---|
Typical Impact Toughness [J] | 10 |
Fatigue
Heat Treated | |
---|---|
Fatigue strength [MPa] | 732 |
Fatigue strength at 1 x 10 million cycles in heat treated state
Fatigue strength determines a stress level where specimen fails at a defined number of stress cycles [ISO 12107]. Fatigue strength was estimated statistically according to ISO 12107. Testing was performed according to ASTM E466. Fatigue results typically show large deviations due to the nature of the fatigue process [ISO 12107].
Surface Roughness
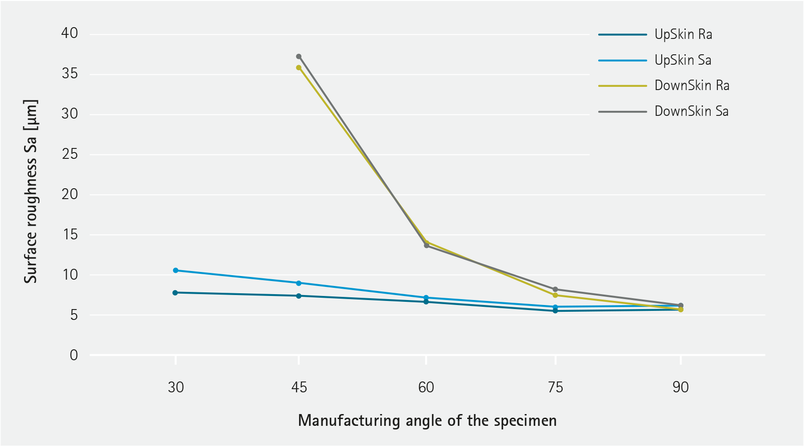
Coefficient of Thermal Expansion
ASTM E228 | Temperature |
---|---|
10.72*10-6/K | 25 – 100 ºC |
11.15*10-6/K | 25 – 200 ºC |
11.5*10-6/K | 25 – 300 ºC |
11.51*10-6/K | 25 – 400 ºC |