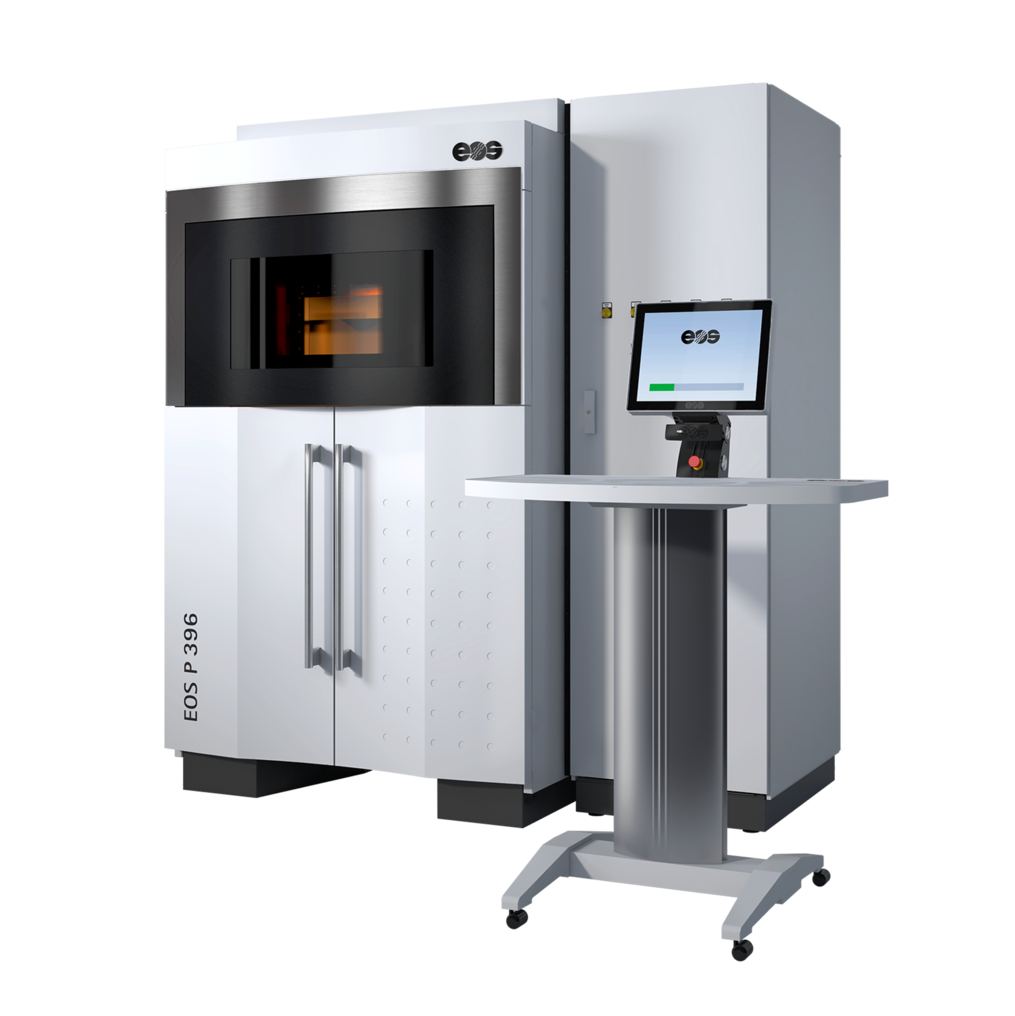
POLYMER SOLUTIONS
EOS
P 396
- All 3D printed parts with excellent mechanical properties and dimensional accuracy due to software features such as Smart Scaling, EOSAME and a continuous temperature monitoring.
- Highest productivity ensured by its powerful laser plus high scanning and recoating speed.
- A multitude of applications that fully meet industry requirements is possible with the 14 materials and their 26 parameter sets.
- Full integration into the IIoT environment with EOSCONNECT Core resulting in an entirely digital process chain from the CAD model, through ERP and MES connection, to the finished part.
- Maximum machine park uptime with digital track and trace from everywhere and at any time.
- Continuous optimization of the entire production workflow made possible with the evaluation and documentation of all build cycles.
EOS P 396
Reliable Production with the Industry‘s Largest Material Portfolio
The medium-sized bestselling EOS P 396 can be integrated into IIoT environments. It enables a flexible and tool-free production of everything from spare parts on-demand, to serial production.
EXPOSURE MODULE
LASERS
- 1 x
70 W
SOFTWARE
-
EOS SYSTEM SUITE EOS System Suite optimizes production by streamlining processes, integrating with MES and shop-floor IT systems, and generating detailed quality reports.
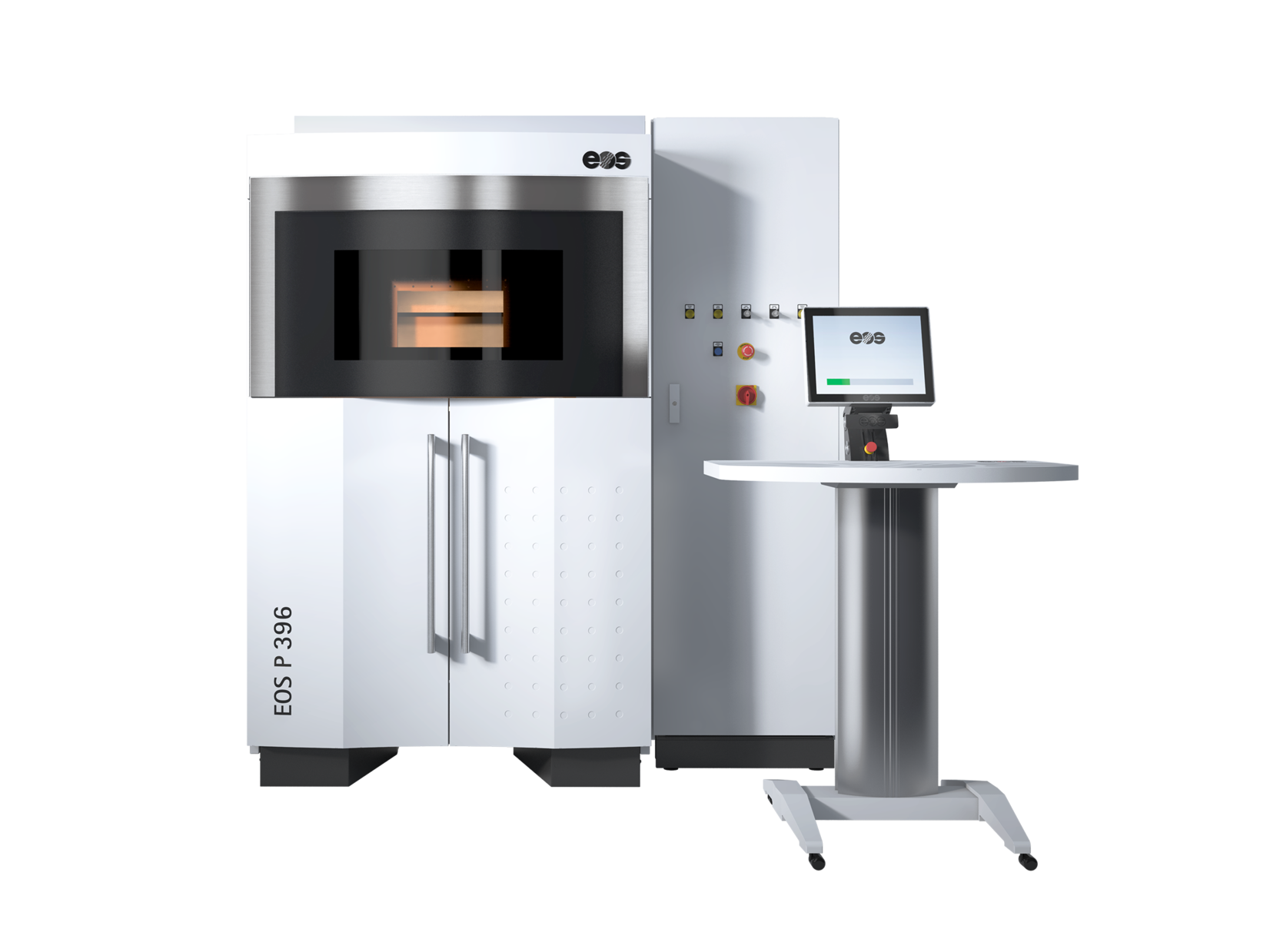
EOS P 396
TECHNICAL DATA
BUILD VOLUME | 340 x 340 x 600 mm (13.4 x 13.4 x 23.6 in) |
LASER TYPE | CO₂; 1 x 70 W |
SCAN SPEED | up to 6.0 m/s (19.7 ft/s) |
POWER SUPPLY | 1 x 32 A |
POWER CONSUMPTION | max. 10.0 kW / typical 2.1 kW |
MATERIALS & PROCESSES
EOS has exceptional materials expertise and a comprehensive portfolio of highly developed materials for additive manufacturing. Our materials, systems and process parameters fit together optimally. With the right materials, you can realize the desired property profiles in the best possible way for your products
EOS P 396
-
PA 1101
-
PA 1101 ClimateNeutral
-
PA 1102 Black
-
PA 2200
-
PA 2200 CarbonReduced
-
PA 2201
-
PA 3200 GF
-
Alumide
-
EOS TPU 1301
-
PA 2210 FR
-
PA 2241 FR
-
ALM FR-106
-
ALM HP 11-30
-
ALM PA 640 GSL