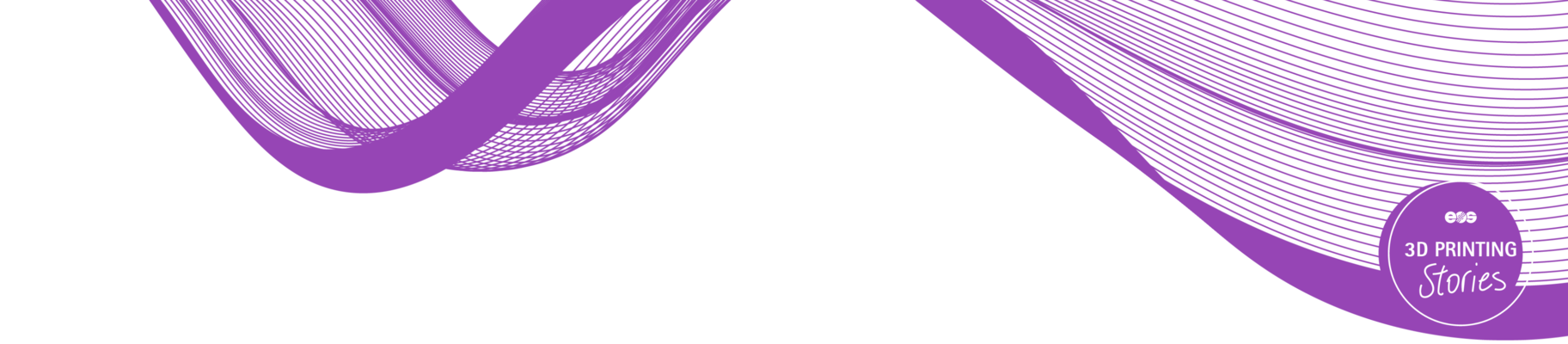
3D-Printed Prostheses for Dogs
AMFox develops customized 3D-printed prostheses and orthoses for animals
April 17, 2024 | Reading time: 10 min
3D-printed prostheses for dogs: Fast, durable and individual
Some ideas take a somewhat circuitous route to the person who will ultimately implement them. This is certainly true of the visionary idea that individually fitted prostheses and orthoses could also be produced for animals; after all it has been several years now since additive manufacturing revolutionized the use of orthopedic technology in human applications. It was the University of Veterinary Medicine Hannover that submitted the idea to Hannover Impuls, a support program that mediates between science and industry. It didn’t take long before the right partner was found in the person of Florian Lange, today the CEO of AMFox. Having now concluded its foundation and discovery phase, the company is ready to make a start in improving the lives of dogs and dog owners, with individually fitted, 3D-printed prostheses and orthoses.
Approaching the product: From orthosis to prosthesis
Florian, who previously worked at EOS, immediately realized that the only technology suitable for making individually fitted orthoses and prostheses for dogs was additive manufacturing. The use of SLS technology ensures a maximum of design freedom and flexibility, resulting in products that can be individually fitted to each individual animal. To help him reach his goal, he teamed up with Roman Reiner Schmidt, partner and co-founder of AMFox, who, like him, was able to contribute a wealth of experience in 3D printing projects. The two of them took their first steps with orthoses for the hyperextension of the carpal joint in dogs. A little background information: the joint consists of several small bones, stabilized by tendons. If the ligaments lose their supporting ability, the front leg bends backwards and is no longer able to stand straight above the paw. This hyperextension creates an incorrectly distributed load on the joint, which causes pain to the dog.
As Florian explains, “previously, this was treated with a brace, but in 30 percent of cases it led to complications, since it is unsuitable for older animals, as they are no longer able to tolerate anesthetics. Our orthosis supports the joint without the need for surgery and assists the animal in regaining a good quality of life.” After successfully implementing a variety of orthoses, Florian and Roman continued to develop their concept of a standardized product, which led to the idea of creating prostheses. "Our goal was to establish a kit of components that would enable us to create an individual fit for any dog at low expense."
3D-printing creates what only 3D printing can create: Lattice structures and TPU inlays
One question that needed to be solved in developing the product concerned which elements are required to ensure a solution that is both convenient and medically sound. For instance, AMFox works with a net-like inlay that enables a prosthesis to be fitted into the torso as comfortably as possible, following the amputation of a front leg. It can be produced from a thermoplastic elastomer (TPU) using SLS 3D printing technology, needs no support structures, and can be squeezed together like a sponge. Not only is there as good as no pressure on the dog’s torso, it also has a very good cushioning effect. The elements providing support to the joint between the thorax and the leg are made from hard cover shells that have a lattice structure and are printed from PA11. As Florian explains: “This is already an established material in human-medical applications, as it doesn’t splinter and is very malleable. Because each prosthesis is designed for an individual dog, it provides a perfect fit.“
Then there are two components for the leg, which are screwed to the joint. The upper section has a thread that enables the length to be adjusted over a certain range. The positioning angle of the paw can also be individually set, allowing the dog to get used to wearing the prosthesis. Alternatively, a wheel is also available, since some dogs actually get on better with this. “We have now achieved exactly what we set out to achieve: a kit that enables all forms of patient-individualized fitting. This is also useful in the event that a part breaks, as it is not necessary to replace the whole prosthesis but only the 3D-printed part - which is significantly cheaper for the dog owner."

How it works: A network for the digital dog
But how does a dog actually get its prosthesis? First let us take a look at current practice: unfortunately, animal orthopedics is not available everywhere in Germany, which often requires dog and owner to undertake a long journey. Moreover, several appointments are needed for the design, production and fitting of the prosthesis. This is not only very expensive but it also takes a long time. The AMFox concept solves this problem by creating a digital model of the dog. To this end, Florian and his team are assembling a team of partners who are able to supply photogrammetric data. As Florian explains: “The owner brings his dog to us, and the entire animal is photographed in one shot using multiple lenses. Alternatively, we can use X-ray or CT images, and we are also working on other, AI-supported ways of obtaining the necessary data.”
Once the digital image of the dog has been created, AMFox applies an algorithm that adapts the basic design parameters of the prosthesis to the individual body of the dog. This results in a print file that can be processed directly on a FORMIGA P 110 Velocis, which is currently carried out at AMFox. But another vision is also being developed for this component. In future, the idea is for production to be carried out by a local 3D printing partner with facilities as close as possible to the dog's home. Florian notes: “This is where the general benefits of additive manufacturing come into play, since we are naturally able to save on logistical and transport capacity, which optimizes our CO2 footprint.” This enables a global rollout of the concept, since, after all, it is possible to establish a network of scanning and production partners in any country. Even though we have not yet carried out any marketing, we have already received inquiries from New Zealand, Turkey and the USA, so there is clearly great interest. Florian and his team are already working on their next idea - to create an insertable walking frame for dogs that have lost both front or hind legs or are paralyzed. And thanks to SLS 3D-printing technology and the innovative concept of AMFox, nothing stands in the way of its realization. We are very curious to see how things progress from here.
#3dprintingstories