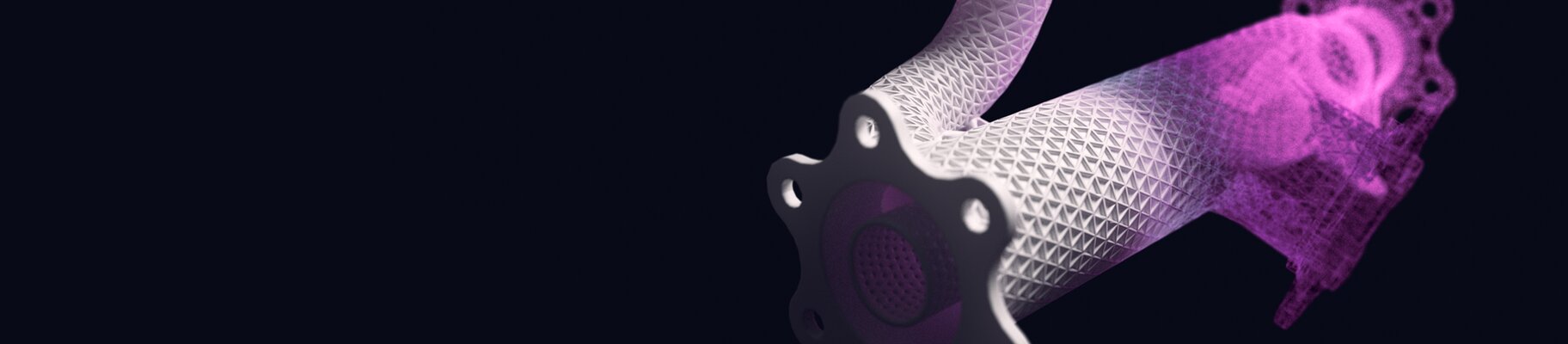
Get Inspired - Polymer
Polymer Additive Manufacturing Solutions
Industrial quality parts – every single time
Despite the creative freedom additive manufacturing allows, many vendors still try to lock you up inside a one-size-fits-all solution. The problem is, even the most inventive teams can’t tweak the process to meet their requirements. Not so with EOS.
Our polymer printing solutions allow for highly reproducible industrial-quality parts, no matter how intricate your design or how daring your plans to scale. To make your manufacturing process truly creative, EOS offers unparalleled customization, so you can easily adapt it to the requirements of your application.
We offer polymer solutions and periphery equipment to match the various stages of your business growth and help your team maintain their innovative stride. Thanks to automation capabilities and fully customizable hardware and software, you’re free to mix and match components that integrate with your existing environment.
Taking Flight with Precision
Polymer AM meets industry-specific requirements to hazard levels and materials at around half the weight of most traditional solutions. This gives airlines and manufacturers the option to drastically reduce their part storage or even switch to just-in-time production, no matter how complex the part design.
The tool-free process allows for streamlined operations at lower costs and helps aviation companies to lower their carbon footprint through reduced transportation costs and lighter parts.

Custom Healthcare Perfectly Printed
Polymer 3D printing offers a myriad of benefits that cater to the evolving needs of the healthcare sector, one of the most significant ones being customization. With the capability to create patient-specific implants and prosthetics, AM is revolutionizing the way healthcare can be delivered. Moreover, the biocompatibility of many materials ensures that the body resorbs printed parts without complications.
Yet, addressing customer challenges across reliable production and regulatory compliance is paramount, and polymer 3D printing meets this demand with precision. It guarantees excellent dimensional accuracy and repeatability, ensuring consistency and reliability in the production of vital medical components. Adhering to stringent regulations is simplified, as the technology allows for the creation of parts that comply with the industry’s exacting standards, ultimately enhancing patient safety and the quality of care.

Custom Creations for Consumer Goods
The consumer goods industry is moving at an unprecedented pace, with a higher demand for individualized designs than ever before. Polymer 3D printing offers a treasure trove of advantages for both producers and consumers. With the option to let consumers design their dream products, customization reigns supreme, be it unique household items or personalized fashion pieces.
At the same time, polymer also addresses the industry’s crucial challenge of producing aesthetically pleasing personalized products at scale, as it enables the creation of eye-catching, artistic designs that stand out. On the production side, 3D printing provides manufacturers with the flexibility to swiftly adjust to changing demands and customize parts or produce variants at a lower cost.
Polymer can even indirectly contribute to your own sustainability efforts and branding. By offering eco-friendly, less wasteful products, you can appeal to environmentally conscious consumers and align with the values of an ethically conscious market. Rapid prototyping and quick iterations are the cherry on top, enabling a faster time to market and ensuring consumer goods follow the latest trends. With polymer 3D printing, the consumer goods market is ushering in a new era of personalization, sustainability, and agility.

Metal Coated Waveguides
Metal-coated waveguides employing fine detail resolution technology bring a host of game-changing benefits to various technological applications. They facilitate the transfer of substantial data volumes through high-frequency electromagnetic waves, supporting frequencies as high as 100 GHz. This, coupled with their unmatched design flexibility, enables precise tailoring to meet performance and frequency requirements, all while fitting seamlessly into compact spaces. Remarkably, these waveguides boast propagation losses that are a mere fraction of those encountered with classical 2D circuit board approaches, enhancing signal integrity.
Their applications are as diverse as they are impressive. From powering radar systems in autonomous vehicles and aircraft to facilitating IIoT sensors, full-body scanners at airports, remote space exploration, and robust data transfer in telecommunication, these waveguides are indispensable in today’s technological landscape.

Digital Foam
EOS’ Digital Foam program is revolutionizing 3D-printed foam production for various applications like helmets and soles. This innovative solution combines product design, materials, part qualification, and 3D printing. Companies can seamlessly produce additively manufactured helmets, orthopedic aids, high-performance shoes, and more in less time.
To make for a more streamlined production process, we rely on solid engineering software and then finetune the results through detailed design and analysis protocols.
