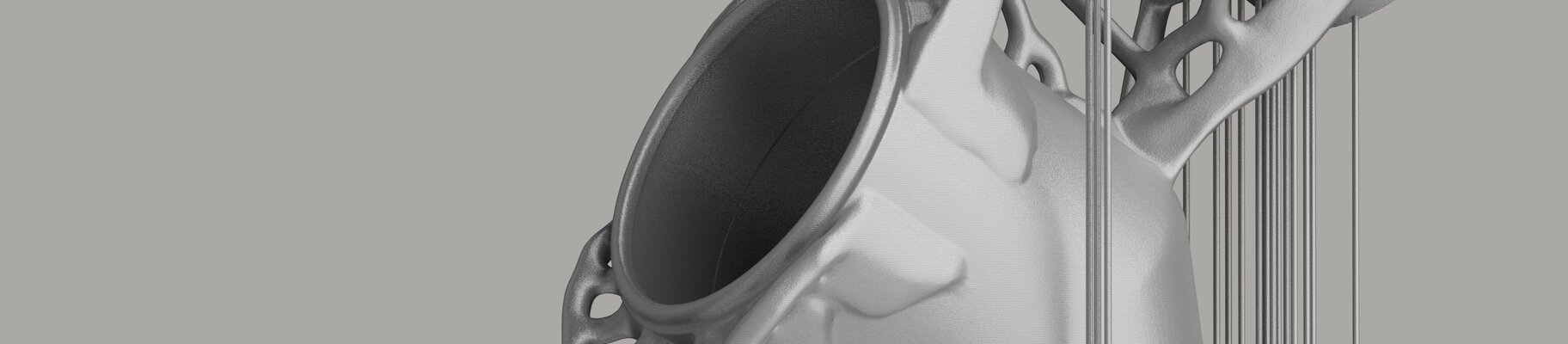
Pursue the Possibilities of Support-Free Building With Smart Fusion
September 20, 2023 | Reading time: 5 min
Support-free building for metal additive manufacturing is not yet commonplace, but it's been proven feasible. The revolutionary real-time process control of EOS Smart Fusion will play a major role in realizing engineers' vision of minimal-support or support-free metal 3D printing.
While EOS experts are working on several support-free projects, the prospect raises concerns for some in metal additive manufacturing (AM). The aspects of a build with which supports are associated — including part orientation, design, heat transfer and recoating — all have a great influence on the build's success or failure. There are some understandable reservations regarding the idea of abandoning a historically effective approach
With Smart Fusion, a highlight of the new EOS Smart Monitoring subscription plan, the level of real-time layer-by-layer control you have over the build process can mitigate or eliminate some of the most significant risks that supports traditionally address. Leveraging this technology is practically beneficial — via its reduction of overheating risk, increased rate of successful assembly and use of few or no supports — and also grants unprecedented freedom to AM designers.
In this blog, we'll explore the support-free concept’s genesis, look comprehensively at the unique way Smart Fusion helps bring engineers closer to it and consider some future implications of these advancements in metal AM.
The Limitations of Supports
Until recently, supports were considered an unavoidable reality of metal additive manufacturing. They're assembled during the build process with the same powder as the part being manufactured and strategically placed as needed. Supports are then removed in post-processing.
Parts orientated with complex structures, where a great deal of surface area doesn't touch the 3D printer's build plate, require supports to ensure the assembly’s integrity. The same has historically been true of designs that include channels, holes or overhangs more acute than 45 degrees (or any other similarly acute angle). But disruptions stemming from excessive laser power levels, thermal stresses and recoater blade damage are generally the most pressing motivators behind support use.
Supports came with notable downsides — increased total print time, added material use, lengthy post-processing and cleaning — but only in the last few years did additive experts begin working on alternate methods in earnest.
Emergence of the Supportless Concept
The factors adjusted to reduce (and, if possible, eliminate) the need for supports vary. Design can play a role — for example, plotting the specifications of a part's walls or arches so that they're self-supporting.
The optimization of processes and parameters is even more important: Laser power is critical, but many other parameters can also be adjusted to facilitate support-free building, including but not limited to scan speed, scan pattern, adjustments to the downskin dimensions (the part's downward-facing surface) and recoating techniques.
The Power of Smart Fusion
EOS engineers and the experts from our Additive Minds team have allocated a great deal of time and resources toward the development of technologies and process optimization techniques to facilitate support-free metal AM. One of our most important developments in this vein — albeit one with clear utility for all metal AM jobs — is Smart Fusion.
We called Smart Fusion a "game-changer" upon its announcement, and that may have been selling it short. This software solution enables intelligent heat management with a never-before-seen level of real-time control. Smart Fusion ensures that a metal 3D printing system's laser power is always in line with the parameters established in EOSPRINT, measuring the powder bed’s laser absorption and adjusting laser power up or down whenever necessary. Advanced, intricate algorithms govern the laser's function to keep heat levels consistent, greatly reducing the risk of overheating.
Because of the diminished heat risk, which is among the biggest reasons supports are used, you can reduce the number of supports for a given build by up to 75%. In truth, all of the advantages Smart Fusion helps you realize during the build contribute to circumstances that make support-free building easier to attempt. For one, your builds can be 2 to 5 times faster. With accelerated builds and minimal overheating hazards, there are fewer chances for a recoater blade to disrupt the process or for other temperature-related stresses to materialize. If you reduce these risks, you reduce the need for supports.
The value of Smart Fusion's precision process control extends beyond the build itself. Ultimately, you’ll improve build consistency and increase your chances of getting a part right the first time — thus minimizing the cost-per-part and resource expenditure of multiple part iteration.
Insights From EXPOSURE OT = Fuel for Smart Fusion
Smart Fusion has a critical relationship to the EOSTATE EXPOSURE OT platform. (Hence their pairing in the EOS Smart Monitoring subscription plan.)
EOSTATE EXPOSURE OT combines near-infrared optical tomography hardware and complex analysis software. The camera records live, real-time OT images from build jobs, and the software program's advanced algorithms detect hot spots, cold spots or any other heat distribution anomalies, along with any existing or potential flaws these might lead to. Armed with that OT data and controller settings within the software, Smart Fusion can apply the appropriate laser correction factor (LCF) and ensure the safe production of metal parts according to their specifications.
The Future of Metal AM With Zero (Or Few) Support(s)
Because support-free building is still a nascent method, it's not a process any metal additive manufacturing user can jump into. For the immediate future, "support-free" might more often mean very few supports rather than zero. Also, there will be some applications where the method won't be ideal, such as those requiring particularly complex part geometries, or larger parts.
But, in the long run, EOS believes support-free building’s value will outweigh its limitations and that our dedication will lead us to technologies and processes that help mitigate those shortcomings. The potential advantages are simply too great to ignore: In addition to long-term cost savings (particularly cost-per-part), improved productivity and more consistent part quality, supportless building will help lower material consumption, contributing positively to responsible manufacturing and sustainability goals.
Review this case study to learn how EOS experts eliminated the need for internal supports from an intricate impeller part design, with only a few external supports required. To find out more about Smart Fusion, the Smart Monitoring plan, EOS metal systems, software, materials and more, contact us today.