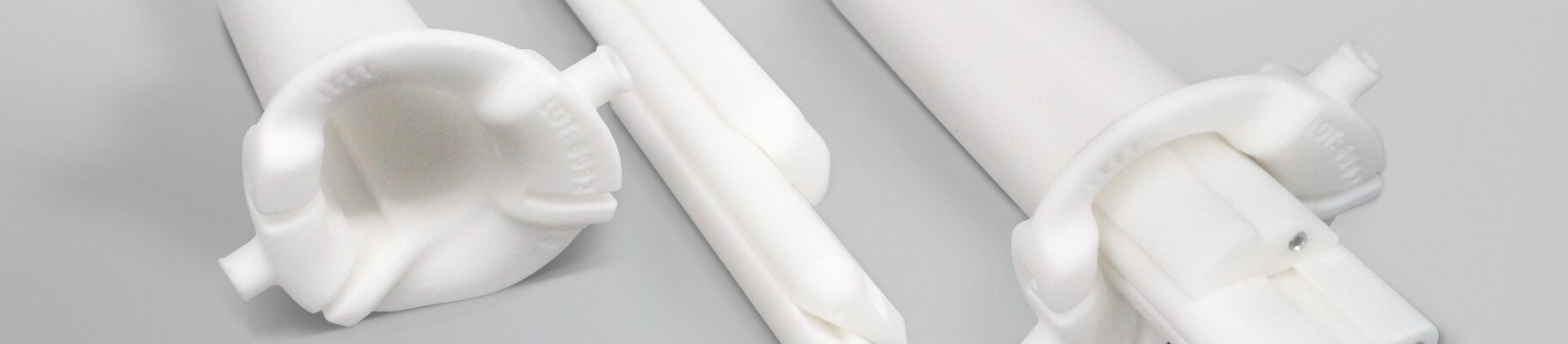
Save Time and Improve Outcome of Spinal Fusion Surgery
Anatomics | Success Story
Spinal Fusion Surgery Using SLS Printing Technology
Spinal surgery is a complicated procedure requiring an extensive and costly support network. Anatomics’ SpineBox™ method of pre-planning surgery and of manufacturing customized devices has the potential to realize significant time and cost benefits for the healthcare system. The streamlined procedure and solution not only improve the patient outcomes, they also reduce the risk of infection, as well as the strain on central sterile services departments (CSSD).

"The innovative SpineBox™ system from Anatomics is aligned with our mission to improve reconstructive surgery outcomes. EOS SLS technology was the obvious choice to manufacture the anatomically matched surgical instruments at the core of the system."
Peter Ostiguy | Staff Team Leader | DePuy Spine
Challenge
As demand for patient-specific solutions in spinal fusion surgery grows, the need for a robust, highly accurate and scalable 3D printing technology for manufacturing biocompatible devices is also growing.
The cost of treating lower back pain in the United States has been estimated at $90 billion per year in 2008 with a further $10-20 billion in costs due to loss of productivity. A significant portion of the expense is attributable to spinal fusion surgery. Anatomics seeks to improve the efficiency of fusion surgery by reducing the manufacturing and supply cost of equipment and optimizing the workflow within surgery without compromising clinical outcomes.
Solution
Anatomics has developed an innovative solution called SpineBox™ - a customized kit that uses individual patient CT scan data to create patient-specific devices and pre-plan the selection of spinal fusion hardware. The patient-specific components are produced using 3D printing (3DP) – specifically EOS Selective Laser Sintering (SLS) technology utilizing the FORMIGA P 110 and PA 2200, a nylon 12 material. The SpineBox™ kit greatly simplifies minimally invasive transforaminal lumbar fusion surgery (MIS TLIF) and can be adapted to support most spinal fusion techniques. Using Computed Tomography (CT) patient scan data together with custom planning software developed by Anatomics, a patient-specific solution involving screws, rods and an intervertebral spacer (fusion cage) is designed for each MIS TLIF surgery. The SpineBox™ kit consists of the following components: A 1:1 scale model of the patient’s spine is 3D printed with EOS SLS technology using PA 2200 and provided to the surgeon and patient to verify the surgical plan pre-operatively. The patient-specific SpineTube™ tissue retractors and anatomically matched positioning templates for surgery are also manufactured from EOS PA 2200 and sterilized. Based on pre-operative measurements, the required titanium implants are pre-selected and packaged with the SLS Nylon 12 instruments and provided as a SpineBox™ kit to the hospital before surgery.The SpineBox™ method of pre--planning surgery and manufacturing customized devices has the potential to realize significant surgical outcome and cost benefits for the healthcare system.

Results
With the Anatomics SpineBox™ kit, the pre-planned specifications for the spinal construct can be mapped onto the bony spine from the skin surface using the 3D printed surgical positioning template, K-wire and minimal radiography. Once deployed, the K-wire provides a railroad for all subsequent instrumentation. The patient-specific SpineTube™ tissue retractor, manufactured to match the skin-to-spine depth, is then temporarily affixed to the spine with an insert and locking screw. The unique insert doubles as an osteotomy guide. Together, these innovative 3DP instruments facilitate nerve decompression, fusion cage implantation and accurate completion of the spinal construct.
Studies have shown that with pre-planned surgery specifications and streamlined 3D printing solutions, patients benefit through reduced operating time, reduced exposure to radiation during operation and, most importantly, significantly reduced complication rates and re-operation rates.
As of August 2019, the SpineBox™ has been used successfully in over 300 surgeries in Australia. Now, Anatomics is set to expand globally with plans to provide its SpineBox™ kit in other countries as of 2020. Anatomics decided to work with EOS’s SLS technology for scalable manufacturing of 3D printed components.
The FORMIGA P 110 printer with EOS PA 2200 material was the obvious choice as it is the standard worldwide for highly accurate, biocompatible (for transient use) and mechanically strong components for surgical cutting and drilling guides. EOS’s reputation for excellence in German engineering and after-sales support was also a critical factor that convinced Anatomics to continue partnering with EOS for their global expansion plans.
The Results at a Glance
- Improved efficiency of entire workflow from planning through recovery
- Radiation exposure reduced by 38.5 %
- Operating time reduced by 17 %
- All patients mobilized day one post-operation