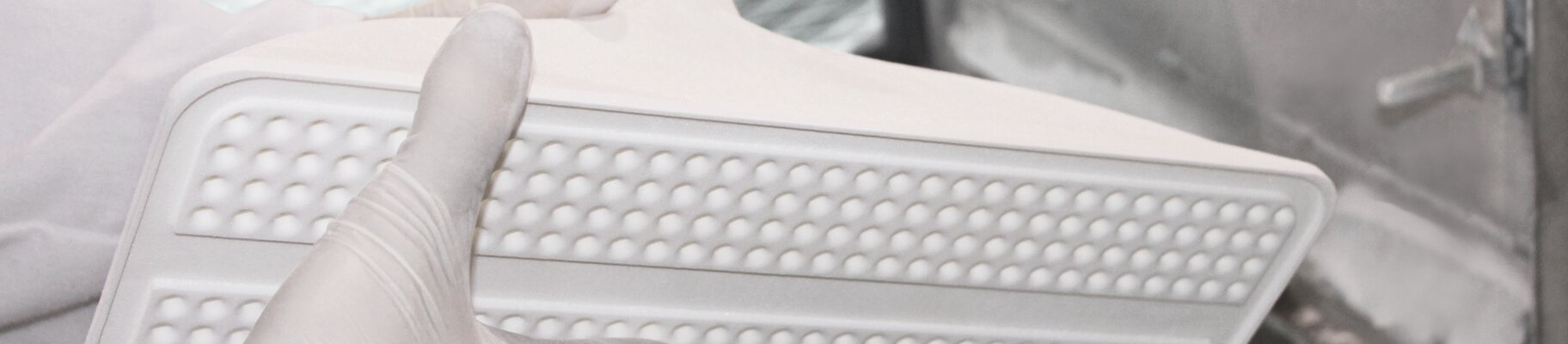
Additive Manufacturing for Gripper
End-of-Arm for Smarter Packaging Manufactured with FORMIGA P 100
Anubis 3D | Success Story
-
Less parts make assembly very easy
-
New tool was ready to use in just one week
-
500 g light gripper has four times the power
"I tell people that, unlike traditional manufacturing, complexity is free with additive manufacturing. A designer can come up with all sorts of wild ideas and no one will complain. You can reduce part weight, maintain strength, and deliver nice looking products with greater functionality, in less time and at lower cost than ever before. It's a real manufacturing shift."
Tharwat Fouad | President | Anubis
An Innovative, Industrial, 3D Printed End-of-Arm Enables Langen Group to Lighten the Load on Their Customer’s Robotic Packaging Line
To achieve maximum speed without upsetting the center of gravity of the robots, the tool — plus the weight of the product itself — couldn’t weigh more than two kilograms. But the largest load of crackers on the line was 1.5 kilos for a ten-pack. That left only 500 grams with which to design the perfect tool. Once the decision to pursue additive manufacturing was made, Fouad performed a detailed analysis of the many different types of equipment available before deciding on a FORMIGA P 100 system from EOS.
In the case of the major American food manufacturer job for Langen Group, instead of a more traditional metal vacuum plate and shroud (which would have taken months to design and manufacture), Anubis designed a lighter, streamlined set of components that provided four times the gripping force of legacy vacuum grippers. It took only a week to additively manufacture, assemble and test the new tool.
The material used for the main vacuum part was nylon 12 (PA 2200 material from EOS), chosen for its flexibility, ability to sustain crash loads, and because it is certified as USP Class VI approved for food contact.

"To design and produce tooling capable of picking what we wanted,
while still staying within the payload constraints of the robot,
would have been impossible before."
Robert Husnik | Engineering Manager | Langen Group
The Results at a Glance
- 4-times the power
- Performance improvement
EOS Success Stories
Explore three decades of pioneering 3D printing excellence with EOS