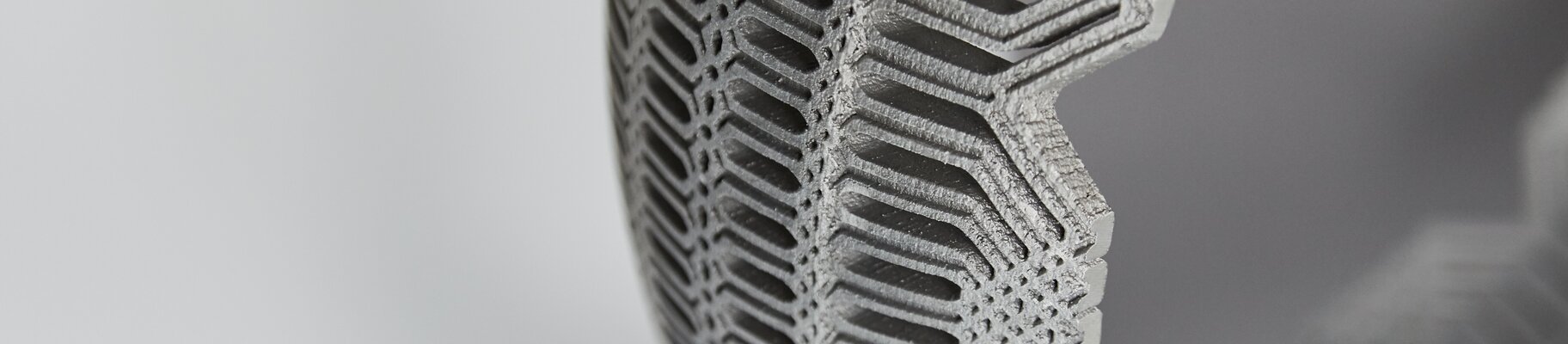
3D-Druck im Fertigungssektor
Anwendungen und praktische Beispiele
Best Practices für den 3D-Druck in Fertigungs- und Produktionsumgebungen
Kostendruck, behördliche Auflagen, steigende Anforderungen der Kunden und vieles mehr. Unternehmen in Produktion und Industrie sehen sich mit einer ständig wachsenden Zahl von Herausforderungen konfrontiert. Gleichzeitig gewinnen Themen wie Energie- und Ressourceneffizienz immer mehr an Bedeutung.
Die additive Fertigung bietet ein breites Spektrum an möglichen kosteneffizienten und nachhaltigen Vorteilen für Unternehmen in Produktion und Industrie.
Der industrielle 3D-Druck eröffnet neue Möglichkeiten und bietet Lösungen in vielerlei Hinsicht, von der Teileproduktion bis hin zur Optimierung der Investitionsrentabilität. Bei EOS bieten wir maßgeschneiderte Lösungen aus einer Hand für Technologie und alles, was Sie für einen sicheren und schnellen Übergang benötigen.