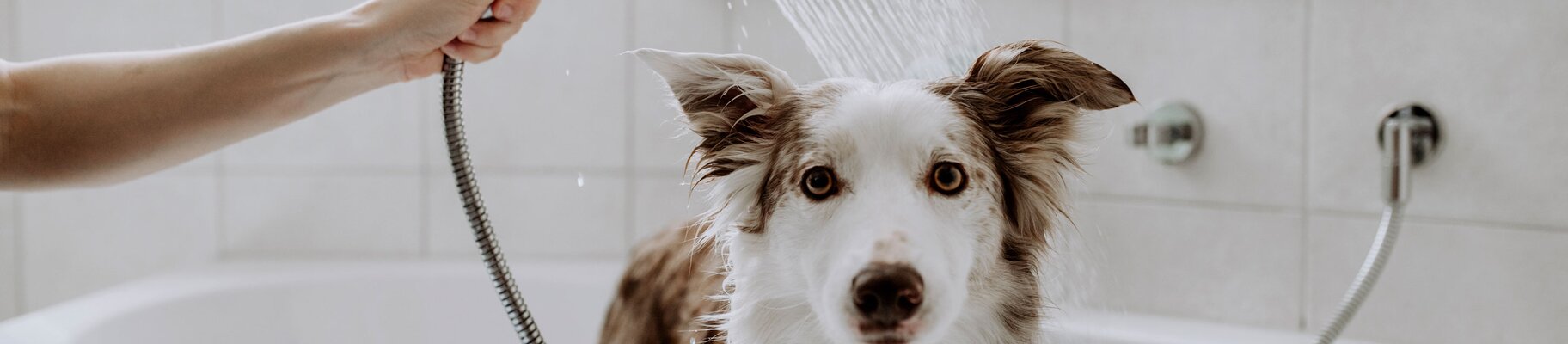
3D Printed Dog Shower - Innovation with an Woof
Hansgrohe | Success Story
-
Sellable product within 22 weeks
-
Drinking water permit for PA 2200
-
Product range expanded with minimal financial risk
"With the EOS P 396, we were able to develop our dog shower head within a short time frame and quickly test whether it would be accepted on the market. Our customers were impressed with the high quality and resilience of the end product. Thanks to 3D printing, we were able to expand our product range with minimal financial risk."
Jochen Armbruster | Head of CA-Tools & Prototyping | Hansgrohe Group
Hansgrohe InnoLab: the Dog Shower
That furry friends do not like to shower is nothing unusual. But what if our water-shy four-legged companion could simply be petted clean?
For the furly canine shower head, there were initially two key tasks to solve: first, improve relations between dogs and owners. Second, take the product from concept to series production under tight cost and time constraints. The goal was to bring a Minimum Sellable Product (MSP) onto the market within just six months – a profitable and high-quality product ready for sale, not just for testing. The project requirements were therefore similar to what you might find in an IT start-up environment, well within the skillset of the thinktank division of faucet and shower specialists Hansgrohe in the Black Forest: agility – test quickly, find errors quickly, learn quickly.
Thanks to close collaboration between Hansgrohe and EOS, a drinking water certification was
successfully obtained for the additive manufacturing material: EOS submitted samples of the powder-based material PA 2200 and the relevant extracts of the patented recipe created by EOS to several laboratories. Compatibility with drinking water was confirmed with no exceptions, meaning that PA 2200 could now be used in sanitary fittings for the very first time. Permit in hand, Hansgrohe now set about building the furly prototype and the first batch of 5 000 units with the EOS P 396 3D printer.
In fact, thanks to the functionally integrated production, the team saved around one third of the parts that would otherwise have been required: reduced complexity makes assembly easier while also reducing additive manufacturing costs. It only took around five and a half months between the first design and an internally tested, sellable product.
The design ensured that there was no need to weld any of the components together. Only the switch valve for changing the jet was fitted separately, borrowing a part from one of their own high-volume series. “Overall, it was cheaper than designing our own additive part,” explains Jochen Armbruster. The switch valve allows dog owners to choose whether the water should flow gently over the nubs of the shower head, or instead as a firm, compact jet. And thanks to the high additive manufacturing quality of the EOS P 396, both furry friends and their human companions will enjoy this special shower head for years to come.
The advantage
Reduction of individual parts
-
-33% individual parts through function integration