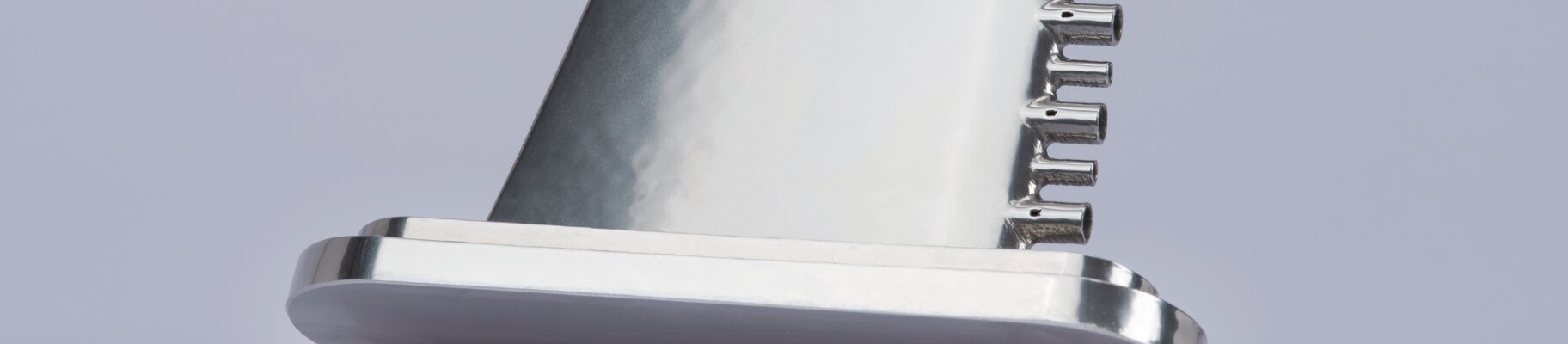
3D Printed Flow Measurement Probe
Vectoflow GmbH | Success Story
Advantages of Probes for Measuring Speed and Temperature in Turbo Engines
- Product development in just 1/3 of the usual project duration
- Freedom of design in terms of form, material and size
- Components are up to 150 % sturdier than those made by conventional manufacturing
Flow Measurement Probes From Vectoflow – Robust Thanks to Additive Manufacturing and EOS
"Our team has many years of experience in fluid-dynamic development as well as in the industry. We are driven by an entrepreneurial spirit that results in the continuous improvement and expansion of our product range, with innovative production methods playing a key role. We are absolutely convinced by EOS technology. It is revolutionary."
Dipl.-Ing. Katharina Kreitz | Vectoflow GmbH
Vectoflow specialises in developing and manufacturing complex flow measurement probes. It uses EOS additive manufacturing technology to achieve an ideal design with maximum endurance.
The engineers were given the task of producing a group of probes with a particularly aerodynamic design a so-called rake. In plain terms, this meant having to produce instruments in a very small and optimised form in order not to disrupt the airflow. When modelling the components, Vectoflow also attaches great importance to minimizing the number of possible disruptive factors and their effects, for example the development of undesirable secondary noise, as acoustics measurement was also part of the remit in this case.
The engineers also found effective solutions relating to thermal load capacity thanks to the nature of the layered production with the EOS M 290. The thermal elements measure the temperature of the respective measuring units. The nickel-chromium alloy is even able to withstand high temperatures of up to the required 1,000 degrees Celsius and continue to be fully functional at twice the speed of sound. Formerly frequent component fracturing is now a thing of the past.
Vectoflow was able to cut its overall production time—from the initial draft to the finished part—to about one third of time it originally needed.

"We received very positive feedback. Unlike probes manufactured using the traditional machining process, our sample was impressively robust. Our component is 150 percent more rigid than conventionally made parts. Moreover, the extremely low thickness, together with the improved aerodynamic design and post-treatment played a major role in allowing the user to obtain very precise measurements."
Dipl.-Ing. Katharina Kreitz | Vectoflow GmbH
The Results at a Glance
- 150 % higher rigidity in comparison to traditional manufacturing methods
- -67 % reduction of project duration time
EOS Success Stories
Explore three decades of pioneering 3D printing excellence with EOS