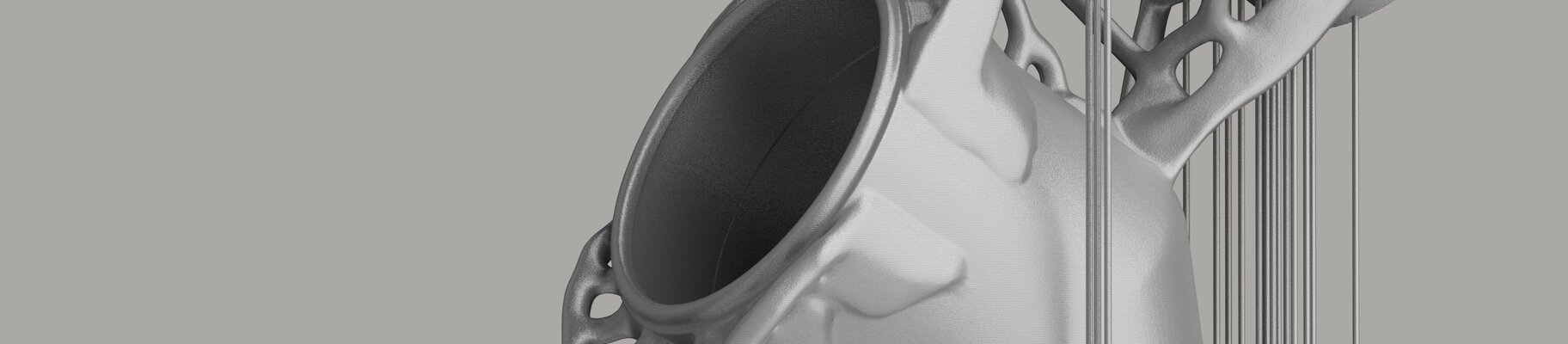
Smart Fusion
Fortschrittliche Prozesssteuerung zur Reduzierung von Stützstrukturen
Die neue Prozesssteuerungslösung von EOS umfasst das erste intelligente Wärmemanagement in Echtzeit, das Stützstrukturen reduziert oder eliminiert und 2 bis 5 Mal schneller als andere Technologien arbeitet.
Smart Fusion ist die jüngste Ergänzung des Engagements von EOS für die Weiterentwicklung und Förderung der additiven Fertigung von Metallen durch innovative Lösungen, die den Prozess vereinfachen, Kosten sparen und die Produktivität steigern.
Wie Smart Fusion Ihren Fertigungsprozess verändert
Die Echtzeitfähigkeit von Smart Fusion passt die Laserleistung automatisch an, um potenzielle Fertigungsprobleme schnell und effizient zu lösen. Die Technologie misst die vom Pulverbett absorbierte Laserenergie und passt sie mithilfe fortschrittlicher Algorithmen an. Ein positiver Nebeneffekt ist, dass Stützstrukturen vermieden oder sogar eliminiert werden können. Dies spart nicht nur Zeit, sondern senkt auch die Kosten pro Teil (CPP) durch reduzierte Nachbearbeitung und geringeren Materialverbrauch.
Diese neuartige Softwarelösung ermöglicht mehr Anwendungen, einen positiven Business Case für AM-Metallanwendungen, insbesondere für Unternehmen mit hochtechnischen Anwendungen wie Energie, Raumfahrttechnik, Mobilität und Luft- und Raumfahrt. Im Kern verbindet sich Smart Fusion mit den bestehenden Überwachungslösungen von EOS und setzt fortschrittliche Algorithmen ein, um den Aufbau Schicht für Schicht zu überwachen und so homogenere und konsistentere Teile zu erhalten. Aus Sicht des Datenflusses bereitet EOSPRINT die Daten vor, die an den 3D-Drucker gesendet werden. Smart Fusion arbeitet mit seiner optischen Tomographiekamera (OT), wobei die erzeugten Bilder den Laser justieren.
Vorteile von Smart Fusion
- Intelligentes Wärmemanagement mit geschlossenem Regelkreis in Echtzeit
Mit unserem intelligenten Überwachungssystem haben wir einen der größten Nachteile des Metall-AM-Marktes behoben. Da wir die Sensordaten Schicht für Schicht nutzen, um die Prozessparameter in Echtzeit anzupassen, sind keine zusätzlichen Abkühlzeiten mehr erforderlich, die die Gesamtbauzeit verlangsamen könnten.
- Kürzere Zeit bis zur Markteinführung
Unsere firmeneigene Technologie umfasst Automatisierungsfunktionen, die den Ingenieuren helfen, die richtigen Parameter schneller zu finden. Dadurch verkürzt sich die Zeit bis zur Markteinführung neuer Produkte, was für Unternehmen, die wettbewerbsfähig bleiben müssen, von entscheidender Bedeutung ist.
- Weniger Abfall
Durch die Verringerung des Bedarfs an Stützstrukturen reduziert Smart Fusion auch die Abfallmenge, die während des Herstellungsprozesses entsteht. Dies ist sowohl umweltfreundlich als auch kosteneffizient.
- Designfreiheit
Mit Smart Fusion haben die Ingenieure mehr Flexibilität bei ihren Entwürfen. Das bedeutet, dass mehr Anwendungsfälle für die Herstellung mit positiven Geschäftsszenarien in Betracht gezogen werden können, und dass mehr ältere Anwendungen lebensfähig gemacht werden können, ohne dass ihr Design geändert werden muss.
- Senkung der Stückkosten
Die CPP macht den industriellen 3D-Druck für die Integration in die Lieferkette attraktiver. Dies führt zu einer größeren Akzeptanz der Technologie und einer breiteren Anwendung in der Fertigungsindustrie.
Funktionsprinzip von Smart Fusion
EOSTATE Exposure OT wird verwendet, um das thermische Verhalten der Teile in jeder Schicht zu überwachen. Ein Controller ermittelt dann die Korrekturfaktoren für die Laserleistung, die zur Aufrechterhaltung einer homogenen Wärmeverteilung erforderlich sind. In der nächsten Schicht werden diese Korrekturfaktoren berücksichtigt, und die Laserleistung wird entsprechend angepasst.
Dieser Vorgang wiederholt sich Schicht für Schicht mit einer hohen optischen Auflösung von ca. 100 µm. Die Anzahl der Iterationen, die erforderlich sind, um ein Teil richtig zu machen, wird auf eine reduziert, zusammen mit der Möglichkeit, Stützstrukturen innerhalb der Anwendung zu reduzieren. Dies führt zu folgenden Ergebnissen:
- Drastische Reduzierung der Stützstrukturen an einer Halterung.
- Herstellung eines Treibstofftanks für die Luft- und Raumfahrt mit einem Überhang von null Grad ohne jegliche Stützstrukturen.
- Ermöglichung der Produktion eines großen Laufrads.
Möchten Sie mehr erfahren? Holen Sie sich das kostenlose Whitepaper hier.