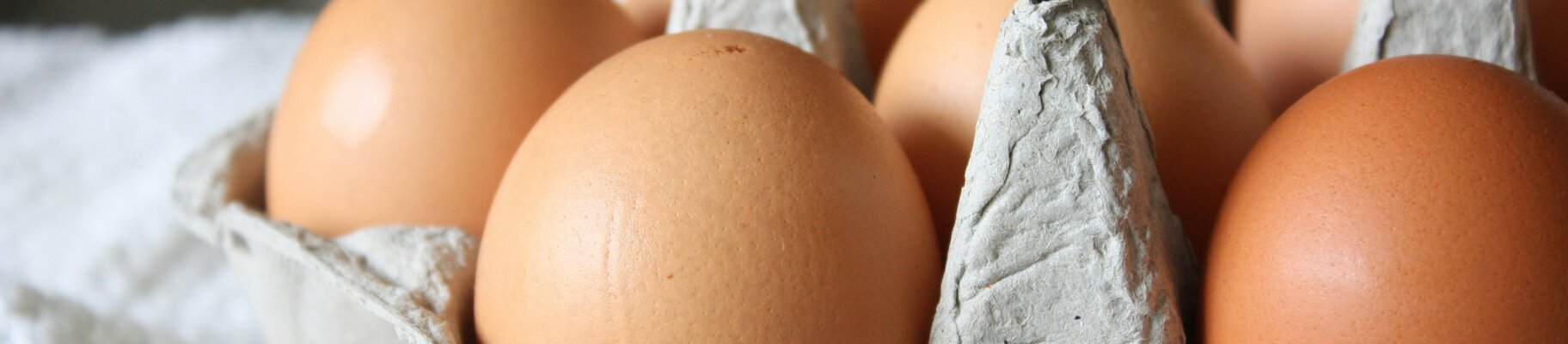
3D- gedruckte Werkzeuge für die Faserguss-Produktion
Payr Engineering | Erfolgsstory
Sauber verpackt
- 50% geringere Werkzeugkosten
- Herstellungszeit sinkt auf wenige Wochen
- Rentabel auch für kleine Losgrößen des Endprodukts
Etwas wie ein rohes Ei behandeln – eine bekannte Redewendung. So robust eine Eierschale im Grunde auch ist, für den sicheren Transport nach Hause ist der berühmte Eierkarton in der Regel die erste Wahl. Die Faserguss-Verpackung schützt und ist umweltfreundlich. Der österreichische Engineering-Dienstleister Payr hat mittels additiver Fertigung das Werkzeug für die Herstellung optimiert und produziert schneller und kostengünstiger. Zusätzlich konnten die Transportwege verkürzt werden und kleinere Stückzahlen sind möglich.

„
Mit den Maschinen von EOS können wir robuste Bauteile herstellen, die mit Maschinen anderer Anbieter nicht zu fertigen wären.
Peter Paul Payr | Geschäftsführer Payr Engineering
Herausforderung
Faserguss – das Wort selbst ist weniger geläufig als das Material. Denn ob aus Altpapier oder nachwachsenden Faserstoffen wie Gräsern hergestellt, immer mehr Unternehmen nutzen das recycel- und wiederverwertbare Material als schützende Verpackung. Die Bandbreite reicht im Endkundenumfeld vom eingangs erwähnten Eierkarton bis hin zu passgenauen Verpackungen, die elektronische oder Haushaltsgeräte schützen. Dank des technologischen Fortschritts kann das Material heute noch mehr leisten. Fettabweisend, wasserresistent – all das ist möglich, ganz ohne Plastik.
Dadurch ist das Material auch für weitere Anwendungsfelder interessant geworden. Eine Herausforderung war bislang die Stückzahl der Verpackung. Der Grund hierfür liegt unter anderem im Produktionsprozess. Grundsätzlich wird das in Wasser gelöste Material – die sogenannte Pulpe – mittels Vakuums in eine perforierte Form gesaugt, die mit einem Überzug aus vielen kleinen Öffnungen versehen ist. Die Flüssigkeit läuft über diese Siebe ab bzw. wird abgesaugt. Das Beziehen der perforierten Formen mit dem Sieb erfolgte meist per Handarbeit vornehmlich asiatischen Produktionsstätten – ein Aufwand, der sehr kosten und zeitintensiv ist.
An diesen Stellschrauben setzte Payr an, wobei der Fokus auf dem Werkzeug und hier insbesondere dem Sieb lag: „Eine solches Bauteil von Hand zu fertig wäre hierzulande zu teuer und ist im Ausland mit langen Transportwegen verbunden, die wiederum Kosten verursachen. Aufgrund der Produktions- und Herstellungszeit beim althergebrachten Verfahren gab so oder so Optimierungspotenzial“, erklärt Peter Paul Payr, Geschäftsführer bei Payr Engineering und Gesellschafter der Payr Gruppe. „Darum haben wir uns nach einer Alternative für die Produktion des Siebs umgesehen und diese in der additiven Fertigung gefunden.“
Günstig & Nachhaltig
Produktionsprozess von Fasergussverpackungen

Lösung
Dabei hat sich Payr eine besonders innovative Herangehensweise ausgedacht: Früher bestanden Form und Sieb aus zwei Bauteilen: einem Metallkern und einer Gitterstruktur, die manuell geformt und aufgebracht wurde. Dank additiver Fertigung konnte eine innovative Entwässerungsstruktur realisiert werden, die nun die ursprünglichen Funktionen der statisch stabilen Form und der regelmäßig verteilten Entwässerung über die gesamte Form in einem Teil vereint. Auf diese Weise ist auch nur noch ein einziger Produktionsschritt nötig. Das vereinfacht die Herstellung zusätzlich und beschleunigt zudem den Prozess insgesamt, bei nunmehr gleichbleibend hoher Qualität.
Als Material hat sich Payr dabei für den in der additiven Fertigung gängigen Kunststoff PA 12 entschieden. Er ist kostengünstig und robust genug, weil der verwendete 3D-Drucker die feine Siebstruktur hervorragend reproduziert. Dass das kein Selbstläufer ist, bestätigt Peter Paul Payr: „EOS hat mit der EOS P 396 ein extrem performantes Produkt im Portfolio. Die Leistung übertrifft die von anderen bekannten Herstellern besonders in Hinblick auf Gitterstrukturen deutlich. Die für diesen Einsatzzweck nötige Stabilität des Bauteils konnten wir mit keinem anderen Gerät erreichen.“
Die Präzision ist ausschlaggebend und damit erfolgskritisch, um den Fluss-Widerstand der Pulpe richtig steuern zu können: Die Geometrie der Entwässerungsstruktur entscheidet einerseits darüber, wie viel Material an der Form haften bleibt und wie stabil die Verpackung später wird. Andererseits beeinflusst sie wie viel Feuchtigkeit zurück bleibt, was sich auf die Trocknungszeit auswirkt. Selbstredend bringt die additive Fertigung auch hier ihre „klassischen“ Vorteile ein, etwa die große Designfreiheit bei der Konstruktion der Form und die kurze Zeit, die überhaupt für ihre Herstellung benötigt wird.
Erebnisse
Die Stunde der Wahrheit ist jedoch stets die Prüfung der Zielerreichung. Und hier überzeugt das neue Werkzeug von Payr auf ganzer Linie: Lag die Beschaffungszeit früher bei mehreren Monaten, so ist die neue kombinierte Saugeinheit jetzt in wenigen Wochen verfügbar. Mindestens genauso wichtig – und beeindruckend – ist die durch die Umstellung erreichte Kostensenkung: „Wir können unseren Kunden hier einen signifikanten Vorteil bieten. Die Kosten für die Fertigung des Werkzeugs sind mindestens 50 Prozent niedriger verglichen zur traditionellen Herstellungsmethode. Und damit sind 3D-gedruckte Formen auch für Verpackungen in kleinen Stückzahlen oder bei Varianten attraktiv“, sagt Peter Paul Payr stolz. Durch die Designfreiheit der Additiven Fertigung ist es auch möglich Endverpackungen mit unterschiedlichen Wandstärken herzustellen, d.h. Material nur dort einzusetzen, wo es notwendig ist.
Gemeinsam mit der optimierten Sieb-Technik hat Payr den gesamten Produktionsprozess unter die Lupe genommen – und dort auf Basis des optimierten Werkzeugs noch weitere Potenziale mit ihrer eigenentwickelten Fasergussanlage FIBRA MINI heben können. So ließen sich etwa die Saug- und ebenso die Entwässerungstechnik verbessern. Daraus resultieren ein geringerer Energiebedarf für die Trocknung und niedrigere Materialkosten, weil die Wandstärken trotz eines Qualitätsaufwuchses noch dünner gestaltet werden konnten. Weniger Material bedeutet gleichzeitig Vorteile im gesamten Lebenszyklus vom Druck bis zum Recycling.
Gar nicht beziffern lässt sich ein weiterer für Unternehmen erzielbare Vorteil: Die Lieferkette wird deutlich resilienter. Eine kostengünstigere Verlagerung eines Produktionsschritts ist nicht nur eine Seltenheit, sondern erhöht auch die Pfadunabhängigkeit für Anbieter von Faserguss-Produkten. Gleichzeitig bietet diese Verschlankung der Supply Chain weitere ökologische Vorteile – denn was nicht um den halben Globus transportiert werden muss, hat naturgemäß auch einen geringeren CO2e-Fußabdruck. Noch wichtiger für die Nachhaltigkeit ist aber, dass Faserguss so noch wettbewerbsfähiger wird und damit immer mehr Plastikverpackungen ersetzen kann.
Für Payr Engineering und seine Kunden ist die Umstellung bei der Fertigung des Produktionswerkzeugs für Faserguss daher ein in vielerlei erfolgreiches Projekt. „Wo können schon Transportwege verkürzt, eine Produktion zurückgeführt und gleichzeitig Kosten gesenkt und die Qualität erhöht werden“, fragt Peter Paul Payr. Und diese ganze Kette von Vorteilen nimmt ihren Anfang technologisch bei: der additiven Fertigung. Damit künftig immer mehr Produkte wie rohe Eier den Weg vom Produzenten zum Kunden finden.
Präzise & stabil
3D-gedrucktes Werkzeug mit innovativer gitterförmiger Entwässerungsstruktur aus dem Kunststoff PA 2200


„
Wir können Qualitätsschwankungen beseitigen und gleichzeitig die Kosten und Markteinführungszeiten reduzieren. Die Lieferkette unserer Kunden wird widerstandsfähiger, Transportkosten und die Menge an Kunststoffverpackungen sinkt.
Peter Paul Payr | Geschäftsführer Payr Engineering
EOS Success Stories
Explore three decades of pioneering 3D printing excellence with EOS