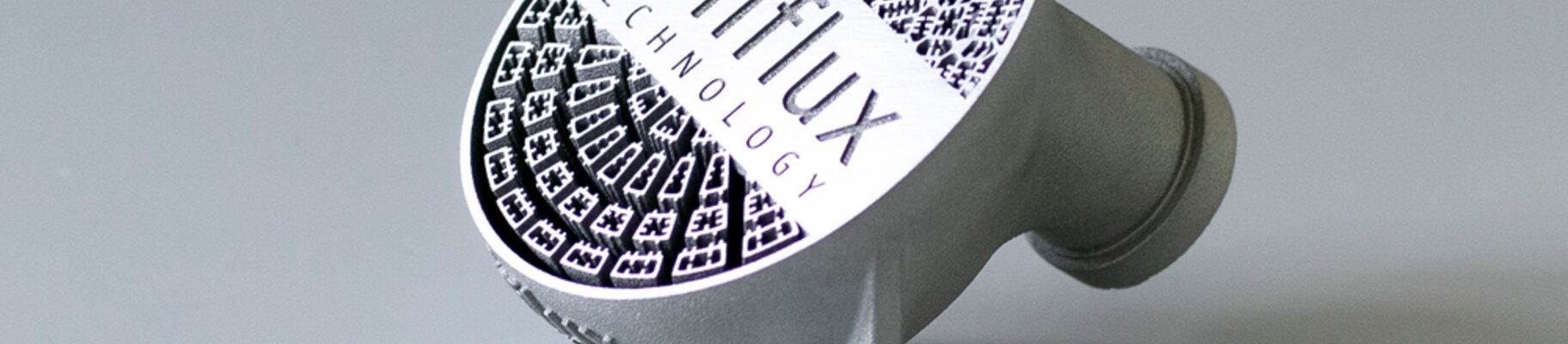
3D Printed Heat Exchanger
Conflux Technology | Success Story
The Next Generation in Heat Exchange Technology With Industrial 3D Printing
Conflux Technology has patented a highly efficient, compact heat exchanger design that derives its performance from a geometry that can only be made using additive manufacturing (AM). High surface area density, combined with optimized fluid pathways and 3D surface features, results in a high thermal exchange, low-weight, low pressure-drop heat exchanger. The performance advantages were achieved within a rapid development timeline which was underpinned by Computational Fluid Dynamics modeling and Design for AM expertise. With no tooling implications to consider, multiple variants can be manufactured simultaneously.
"Our customers' have acceptance criteria that matches exacting quality and repeatable performance. EOS systems are the only AM platforms that can produce our challenging geometries whilst exceeding our customers' requirements."
Michael Fuller | CEO | Conflux Technology

Challenge
Heat transfer is a ubiquitous challenge that is at the heart of the First Law of Thermodynamics. A heat exchanger, simply speaking, is a device that effectively transfers heat between two (or more) fluids, typically a liquid-liquid, liquidgas, gas-gas or multiple fluids. You can find them in products like air conditioners and car engines. One practical benefit of such devices is energy recovery. There are numerous others — it is a complex technology with broad applications. Heat exchanger designs and manufacturing methods have evolved with the prevailing technologies available and, consequently, have been limited by those technologies. Conflux's Founder and CEO, Michael Fuller, spent more than a decade as an engineer in the automotive racing industry.
Here, heat exchangers have to perform in harsh environments. Therefore, smaller and more efficient components are sought but substractive manufacturig methods have reached their limits. Michael Fuller saw the rapid and transfomative benefits of 3D printing and ultimately identified additive manufacturing as an enabling technology for the next generation of heat exchangers. Highly complex geometries with hitherto unachievable surface area densities resulting in a compelling thermal exchange performance could be achieved. And this, packaged in efficient volumes. Such components could have a dramatic effect on future developments, such as lighter racing cars and aircrafts. These fundamental opportunities are extended when functions are integrated and multi-variant simultaneous production is realized. Michael Fuller was set to take this idea from concept, to design, to prototype, to product using industrial 3D printing.

Solution
Additive manufacturing with EOS M 290 and EOS Aluminum AlSi10Mg
Conflux Technology analyzed the industrial additive manufacturing landscape and, after a technical due diligence process, concluded that EOS is the only partner that has the technical and commercial capabilities to fulfill Conflux's ambitions. The Conflux CoreTM design was patented after a rapid proof-of-concept development program. Within just 6 months, 6 prototypes were built and a final product could be developed. During the development program, several tools were utilized: Computational Fluid Dynamics (CFD) complemented the heat exchanger design iterations with flow visualization and, after correlation, performance predictions. Non-linear thermomechanical Finite Element Modeling (FEA) was used to analyze the resultant displacements and stresses to ensure structural integrity was maintained. EOS equipment possesses a suite of specific AM software tools for data preparation, process optimization and quality assurance. These were all used during the development of the Conflux CoreTM heat exchanger which now has applications across multiple industries such as Aerospace, Automotive, Oil & Gas, Chemical Processing and Micro-Processor Cooling.

Results
The Conflux CoreTM heat exchanger was compared to a Formula 1 benchmark. Young Calibrations, a UKAS-certified laboratory in the UK, provides accredited calibration services and thermal fluid and component testing services, and tested Conflux's product. The results (see fig.1) underline the radical improvement Conflux has achieved with their 3D printed heat exchanger. AM allowed Conflux to design internal geometries that radically increased the surface area in a given volume. This tripled the thermal heat rejection. And at the same time, the pressure drop is reduced by two thirds. Additionally, AM enabled a compact and new design of the heat exchanger, reducing its length by 55 mm compared to a F1 benchmark. This ultimately also eliminates 22 percent of weight. The design flexibility AM offers allows for optimum placement inside a vehicle and also enables the merging of components, reducing the overall number of parts.

The Results at a Glance
- 300 % higher heat rejection
- -22 % weight reduction due to lightweight construction
EOS Success Stories
Explore three decades of pioneering 3D printing excellence with EOS