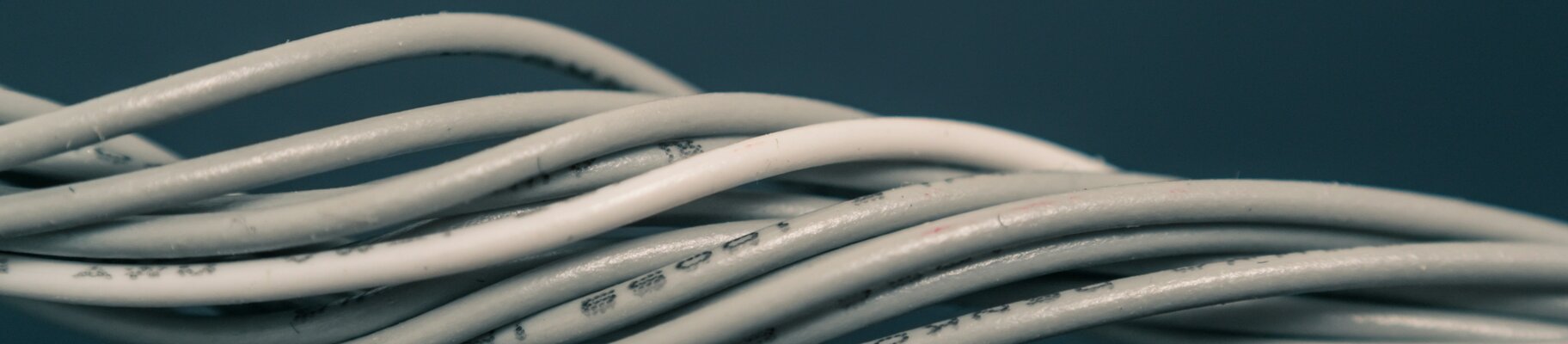
精度与稳定性:FDR3D 打印技术成就电气连接器的未来
WAGO | 案例研究
实现卓越
- 快速交付,只需数天而不是数周即可提供组件
- 质量一流,几乎与最终产品无异
- 简化效率,只需最低限度的后期处理
- 详细决议符合
原型的实验室测试
没有电,我们的社会和经济几乎就无法运转--房屋、工厂、轮船、火车等的供电线路就是我们这个时代的生命线。为了让电子传输能量,它们必须通过电缆到达正确的位置。这就需要可靠的连接元件,例如东威斯特法伦州 WAGO 公司生产的元件。与加利福尼亚的 IT 大本营硅谷相对应,那里的电子产业集群也被称为 "终端谷"。WAGO 公司证明了这一点:在增材制造 (AM)领域,原型制造采用了高分辨率的连接技术原型制造工艺,即所谓的精细分辨率(FDR)。通过这种方式,WAGO 能够使用 PA 1101 在 EOSFORMIGA P 110 FDR 上快速、精确地制作出新产品弹簧夹的原型,从而成功地缩短了新型接线盒和配电盒的上市时间。

"人类需要模型。如果你想取得快速进步,工业3D 打印是绕不开的。它是我们的主力军。常规的选择性激光烧结技术已经给我们留下了深刻的印象,但 FDR 在精细度、精度和速度方面更上一层楼"。."
Olaf Zoschke | WAGO GmbH & Co.KG
挑战
连接两根导线乍听起来很简单,但在细节上却对创新、功能、安全和质量提出了很高的要求。有电的地方就有正确的规定。连接必须符合实际、事实和法律的安全要求:"WAGO GmbH & Co.KG原型制造部主管 Olaf Zoschke 解释说:"即使在负载情况下,电缆也不能从接触点滑脱。KG 的样机制造主管 Olaf Zoschke 解释说。"此外,接触点的轮廓必须具有适当的质量。如果不能保证这一点,就会造成人身和财产损失"。他是 WAGO 公司原型制造部门的负责人:他和他的七人团队一起设计和制造功能原型以及测试样品,这些样品必须通过内部和外部实验室的功能和安全测试;在此之前,任何新产品都不得出售。
因此,对 WAGO 及其市场合作伙伴开发的产品进行的安全测试既广泛又频繁。我们必须应对多项挑战:无论是在家中的电表站还是在轨道车的控制柜中,配电空间都越来越小。同时,可用于开发、测试并将相应产品推向市场的时间也越来越少。"Olaf Zoschke 总结道:"要想快,就不能绕过增材制造。此外,样品必须尽可能与最终的系列产品一致,因为它们不仅要让测试工程师信服,还要让专业零售商和其他买家信服。
在开发安装空间尽可能小的新型接线盒时,电缆夹线套的设计尤其具有挑战性:导线插入插座后,必须牢牢卡住。这是通过夹紧装置实现的。它通过一个联锁齿轮锁定到位。导体上的任何拉力都必须被绝缘层上的固定装置吸收。触头本身不得受力。为了满足尺寸要求,安装在接片上的齿轮也必须尽可能小。同时,还必须具有高度的稳定性,以符合相关的安全规定。在批量生产中,可以执行这样的要求目录,因为传统工艺的成本可以分摊到大批量生产中。但在原型制造中呢?
精确、快速
3D 打印 使 WAGO 能够在很短的时间内开发出功能齐全的接线盒,并成熟地推向市场。


解决方案
"在开发过程中,我们在初始测试和优化过程中自然会更改组件。众所周知,增材制造在这方面具有优势。不过,最重要的是,我们需要一定的批量来进行功能测试和实验室测试。我们需要 10 到 50 件产品,当然,这些产品之间必须绝对等同。Olaf Zoschke 解释说:"例如,精细齿轮所需的高精度直到最近才有可能实现。只有 FDR 能够将工业3D 打印 的优势融入到细微部件的应用中。
此时,借助FORMIGA P 110 FDR 对增材制造 进行精细分辨工艺是最佳选择:由于部件非常小,只需要一个小的制造室就能一次性生产出所需的数量。这也与原型的其他部件实现了 "完美的时间匹配"。根据要求,这些部件采用其他工艺生产,包括更粗糙的选择性激光烧结(SLS)。"例如,对于较大的部件 1,传统的 SLS 就足够了,而对于较小的部件 2,我们则依靠 FDR。SLS 比高分辨率3D 打印更快,但由于零件尺寸的原因,我们在差不多相同的时间内就能得到样品,"Olaf Zoschke 生动地解释道。
原型制作团队会事先确定在每种情况下使用哪种工艺:根据日后的预期用途,在 CAD 规划时就已决定使用哪种工艺和材料。最终,决定性的问题是如何在所需数量内合理地达到所要求的质量。因此,Olaf Zoschke 的团队可以有针对性地利用各个工艺和材料的优势。"FDR 是精确度、高边缘锐利度和功能集成的黄金分割点;PA 1101 作为一种材料非常适合于此。有一些原型制作方法甚至更加精确。然而,例如,功能集成在这里是缺失的。标准 SLS 虽然速度更快,但精度不高,"原型制造负责人补充道。
成果
这种高分辨率的3D 打印 工艺达到了预期的目标:WAGO 能够在预期的时间内,按照要求的公差和数量,成功地生产出齿轮和齿板的样品。通过这种方式生产出的耐用部件在使用寿命方面丝毫不逊于后来的系列产品。生产和后处理只用了两天左右的时间,而其他程序则需要一到两周的时间。说到后期处理:由于增材制造的 FDR 工艺分辨率高,因此只需对部件进行少量的后期处理。
Olaf Zoschke 证实了这一点:"即使没有 FDR,EOS 产品也能提供非常出色的质量。通过后期处理,我们总是能获得令人印象深刻的效果。有了精细分辨率,效果会更好。我们实现了极高的原型设计价值,约为后期系列组件质量的 80%。这也让我们的产品开发人员兴奋不已。SLS 高分辨率技术的另一个优势在于后处理:该工艺还能对不平整的地方进行化学平滑处理。这会导致轻微的 "模糊",因此不如 FDR 生产精确。
通过这种方式,WAGO 组件也获得了样品测试所需的产品特性:精致的挂耳和挂耳齿提供了所需的强度。同时,它们的制造质量非常高,能够无缝互锁,因此非常坚固 - 通过钩挂达到所需的导体夹紧力。多次内部和外部测试表明,如果一个增材制造 部件经久耐用,那么它在批量生产中也同样经久耐用。因此,创新的 FDR 工艺兑现了自己的承诺:进一步提高工业3D 打印的精度和速度,并实现完全集成的功能。
坚固可靠
3D 打印 可提供一流的质量,几乎与最终产品无异
"即使没有 FDR,EOS 产品也总能提供非常出色的质量。通过后期处理,我们总是能获得令人印象深刻的效果。有了精细分辨率,效果就更好了。我们实现了极高的原型设计价值,约为后期系列组件质量的 80%。这也让我们的产品开发人员兴奋不已。
Olaf Zoschke | WAGO GmbH & Co.KG
EOS 案例研究
通过 EOS 探索三十年来开拓3D 打印 的卓越成就