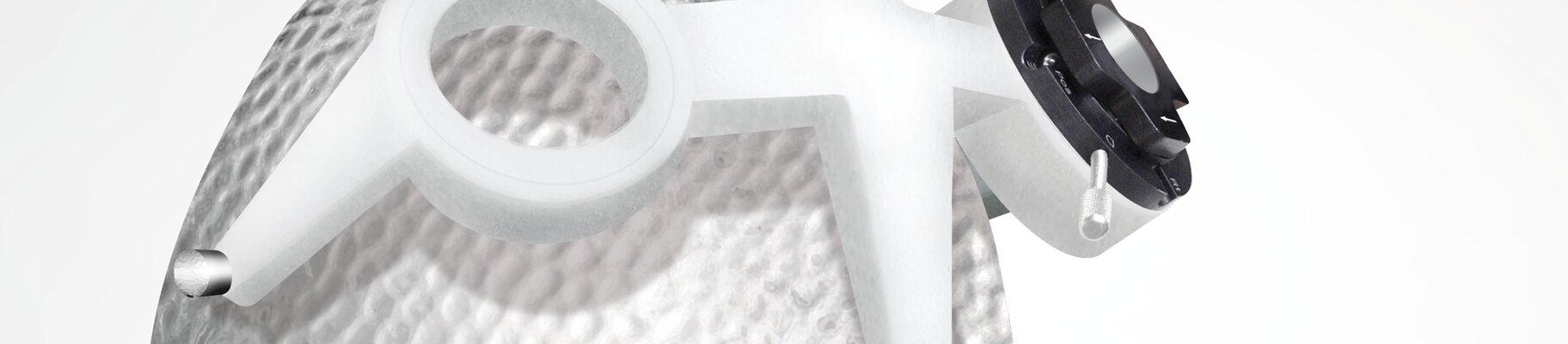
Additive Fertigung für medizinische Geräte 3D-Druck von stereotaktischen Plattformen für die Neurochirurgie
FHC | Erfolgsgeschichte
Stereotaktische Plattformen für die Neurochirurgie
Vorteile durch 3D-Druck
-
Individuelles Design fördert das Wohlbefinden der Patienten
-
Höchste Produktionsqualität nach strengen Standards für medizinische Anwendungen
-
Weniger Material durch schnellere Durchlaufzeiten bei der Herstellung
"Wir gehen davon aus, dass die Umstellung auf das Lasersintern in Zukunft noch mehr Möglichkeiten zur Produktverbesserung bietet. Die Flexibilität einer Technologie, mit der patientenindividuelle Lösungen anstelle von Einheitsgrößen geschaffen werden können, kann sowohl zu Einsparungen im Krankenhaus als auch zu besseren Patientenergebnissen führen.
Fred Haer | FHC CEO und STarFix Präsident
Additive Fertigung von kundenspezifischen chirurgischen Werkzeugen erreicht hohe Präzision
FHC - seit mehr als 40 Jahren weltweit führend im Bereich innovativer neurowissenschaftlicher Produkte - arbeitete mit einem führenden Neurochirurgen zusammen, um die herkömmliche Stereotaxie durch ein 3D-Modellierungsverfahren auf der Grundlage der anatomischen Koordinaten eines jeden Patienten zu verändern.
Die erste Anwendung dieser neuen STarFix-Technologie ist die preisgekrönte, auf den Patienten abgestimmte, rahmenlose microTargeting™-Plattform, die mehr Patientenkomfort, höhere Genauigkeit und Zeitersparnis im Operationssaal (OP) bietet.
Durch den Einsatz des SLS-3D-Druckers FORMIGA P 100 zum Lasersintern der Plattform erzielt FHC Präzisionsergebnisse bei reduzierten Kosten und in Rekordlieferzeiten. Nach den Parametern eines intelligenten, unabhängigen Volumenmodells, das von der Planungssoftware bereitgestellt wird, wird die Vorrichtung im FORMIGA P 100 in nur wenigen Stunden aus Polyamidpulver PA 2201 "gewachsen". Die durch das Lasersintern ermöglichte Konsolidierung der Teile hat es FHC ermöglicht, das StarFix-Design fein abzustimmen und die Montagezeit im OP zu verkürzen.

"Der Trend in der Medizintechnik geht hin zu maßgeschneiderten Produkten. Mit der EOS-Technologie können wir patientenindividuelle Produkte herstellen und gleichzeitig die Kosten kontrollieren, da wir unsere chirurgischen Kunden schneller beliefern können."
Ron Franklin | Geschäftsführer Technik | STarFix