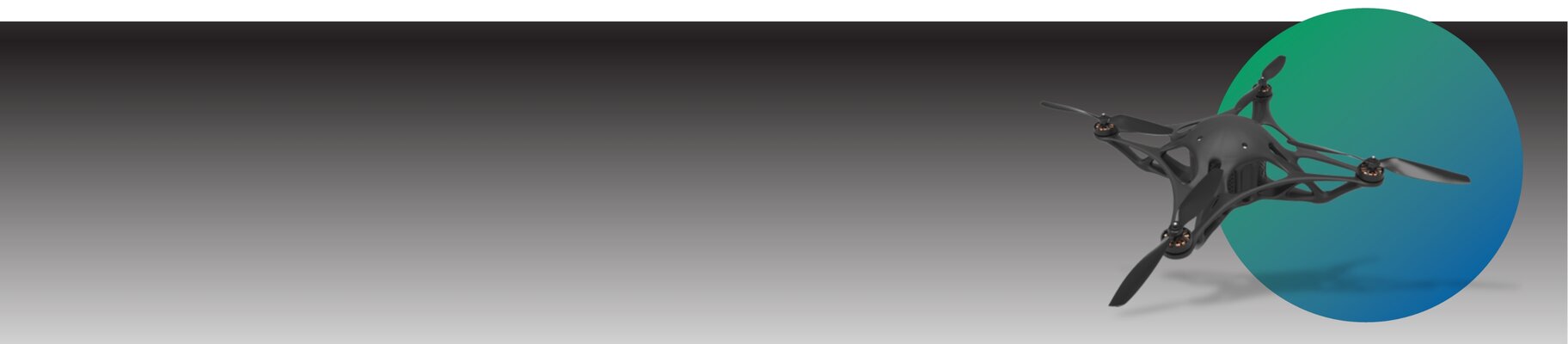
Why SLS 3D Printing is the Right Fit for Drone Manufacturing
June 05, 2025 | Reading time: 5 min
In the fast-moving world of unmanned aerial vehicles (UAVs) and drones, manufacturing demands are evolving. Companies are seeking smarter ways to produce lightweight, functional, and customizable components—often under tight timelines and increasingly diverse use cases.
As an application specialist working with drone OEMs, integrators, and defense contractors, I’ve seen a recurring pattern: teams often start with low-cost 3D printing technologies like FDM (Fused Deposition Modeling) or SLA (Stereolithography) for prototyping, but hit limitations when transitioning toward functional or production-grade parts.
That’s where Selective Laser Sintering (SLS) comes into its own.
A Practical Comparison: FDM, SLA vs. SLS
FDM and SLA are great for early design iterations or visual mockups, but they fall short when parts are exposed to real-world flight conditions—vibration, weather, structural load, and payload integration.
Attribute | FDM | SLA | SLS |
---|---|---|---|
Material Strength | Moderate; anisotropic | Brittle; poor under load | Strong; isotropic |
Weather/UV Resistance | Limited | Poor | Excellent (e.g., PA12, PA11) |
Part Complexity | Limited by supports | Delicate for thin sections | High; no supports needed |
Post-processing | Manual support removal | Curing & cleaning | Simple powder removal |
Production Volume | One-off or low batch | Prototyping | Batch-friendly |
Suitability for Flight Use | Limited | Not suitable | Highly suitable |
Lightweight Design That Performs in the Air
Weight is a primary concern in drone design. Lighter drones fly longer, respond faster, and perform more efficiently under changing wind conditions. But low-cost printing methods often compromise mechanical strength when optimizing for lightness.
SLS allows us to produce lightweight yet mechanically strong parts with precise geometries and thin, consistent wall thicknesses—critical for flight stability and high-altitude operation. Unlike FDM, which often results in anisotropic parts with weak inter-layer bonding, SLS produces fully fused, isotropic structures that behave predictably under stress.
This dimensional consistency translates directly to better in-flight performance, especially when paired with aerodynamic part design and tight tolerance control.
Mixed Production: Injection Molding Meets On-Demand Customization
Many drone platforms rely on injection-molded wings or fuselage shells for efficiency and repeatability at scale. But the reality is: no two end-users are the same. Whether it's a different payload, sensor configuration, or battery system, drone components often need customization—either up front or down the line.
SLS is a natural complement to injection molding in mixed manufacturing workflows. It allows us to:
- Rapidly produce custom mounting systems or payload adapters
- Offer short lead times for small-batch configurations
- Update designs post-deployment without tooling changes
One drone manufacturer I work with uses injection molding for standard components, while SLS handles the payload bays, antenna mounts, and sensor enclosures, which vary between clients. This hybrid model gives them speed without sacrificing flexibility.
Field Adaptability: Meeting Defense and Mission-Critical Needs
In defense and government programs, flexibility extends beyond the factory floor. Some customers are looking to produce main parts with SLS in centralized locations, and then perform quick repairs or replacements in the field using desktop FDM printers.
This dual-level approach—SLS for primary structural parts, FDM for field-replaceable accessories—helps keep systems operational without compromising the integrity of the airframe.
In one case, a defense client requested a complete SLS-based drone architecture but added a requirement to print non-structural covers or access panels using compact printers on site. The ability to swap parts while maintaining the core platform's structural integrity is a major logistical advantage in the field.
Complex Geometries, Reduced Assembly
One of the lesser-appreciated benefits of SLS is the ability to produce complex assemblies in a single build. Without the need for support structures, we can integrate multiple features into a part that would otherwise require gluing or fastening.
This reduces:
- Part count
- Assembly time
- Potential failure points
For example, we’ve helped clients print integrated battery enclosures with cable routing and heat management features built in—something that’s simply not feasible with FDM or SLA without extensive post-processing.
Final Thoughts
Low-cost 3D printing technologies will always have their place in rapid prototyping and hobbyist applications. But when it comes to functional, flight-ready parts that can endure real-world use, Selective Laser Sintering offers a balance of strength, flexibility, and scalability that other desktop solutions can’t match.
In the drone industry, where payloads change, missions evolve, and expectations around turnaround time are tightening—SLS is enabling manufacturers to design smarter, respond faster, and deliver better-performing systems.
If you’re exploring how additive manufacturing can streamline or strengthen your drone production workflow, I’d be happy to share more real-world examples or help evaluate candidate parts for SLS. The possibilities are broad, and the learning curve is shorter than you might expect.