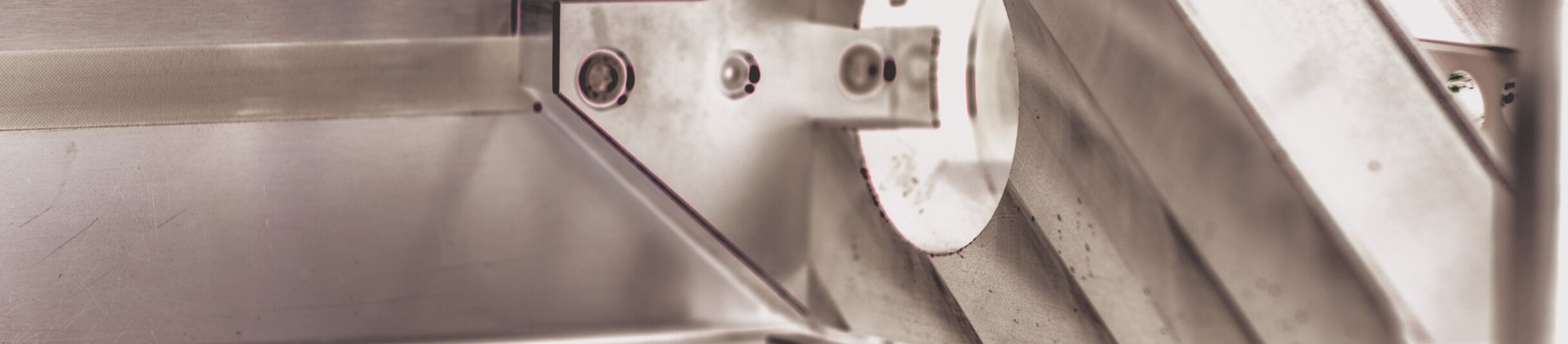
How Metal Additive Manufacturing Recoaters Affect Build Quality
July 27, 2022 | Reading time: 4 min
Choosing a additive manufacturing recoater blade for your metal 3D printing jobs may seem like a difficult decision to make, but what if we told you that it doesn’t need to be? Our research team has been experimenting with additive manufacturing recoater and powder combinations to give you a better understanding of how it affects the quality of your builds.
What are the different recoater materials?
There are several types of recoater blade, each made from a different material and used for a different purpose. They can generally be separated into two categories, though: soft and hard.
Soft recoater blades have an elastomer lip or carbon brush and are generally used for more delicate projects that require a finer detail to the finished part. This kind of recoater has the potential to flex around imperfections, reducing the risk of job interruptions due to recoater jams, but this can mean that parts are less pristinely finished. Soft recoaters are also effective for high aspect ratio parts with a large surface area.
Hard recoater blades can be made from high-speed steel (HSS) or a zirconium oxide ceramic blade, which is ideal for magnetic metal powder builds. Hard recoaters offer a higher level of part quality and repeatability while improving material and process development, which is why they are the preferred choice for EOS 3D printers. While jams are more likely to occur because the blade isn’t as forgiving as a soft recoater, a hard recoater is not the best choice when fine structures have to be built.
Testing the additive manufacturing recoaters
To find out if a different combination of additive manufacturing recoater and metal powder has any impact on the end quality of a build, we chose three recoaters and three print materials for a series of comparative tests.
The three metals chosen were EOS Aluminium AlSi10Mg, EOS Titanium Ti64 and EOS MaragingSteel MS1. We selected these three particular, widely used metal powders because each has distinct properties. The aluminium powder is a lightweight alloy frequently used in aerospace and mobility applications, while the titanium is a much denser, robust material used in various industries, most notably medical implant production. The steel powder is our magnetic material often used in tooling production. The key differentiating factors for these powders, in regards to our experiment, are their varying densities and powder particle distribution, which would allow us to observe how the different recoaters affect a range of powder types.
Each metal was tested with the same soft recoaters — the silicon lip and the carbon brush. Because of its magnetic properties, the steel powder was tested with a ceramic hard blade while the other two were paired with the HSS recoater.
We plotted various standardized builds so each one could be directly compared. A series of simple shapes, such as cylinders in various orientations and cubes, were arranged for the first job layout. This job was run seven times in total — once for each recoater-powder combination, plus one standard ‘control’ version.
A second job was also specifically designed to test the elastomer blades for fine detail printing. The parts in this job included the addition of a lattice ball and a chess rook with a filigree inner structure to really push the recoaters’ capabilities. For this second job, half of the build platform was intentionally left empty so we could observe how the damaged blade affected the powder bed after completing the parts.
What did we find?
Put simply, we found no real difference between each recoater, regardless of what metal powder is used. That isn’t to say there was no difference at all between the parts produced, simply that whichever recoater was used on a certain powder didn’t result in any discernible difference. When each recoater was used while printing with the titanium powder, for example, all the parts built were fairly consistent.
Three main things were assessed for each build to establish where any differences may occur. Firstly, we looked at recoater blade performance to discern if any recoater-powder combination was more likely to jam. Secondly, we examined the overall quality of the finished parts to see if any were distinct from others — the mechanical properties and porosity of the parts built. And thirdly, we analyzed the powder bed following the build to identify any disruptions to the build material, such as powder “clumping” — where powders of varying densities may react differently to the chosen recoater.
For all recoater-powder combinations, we found that the printer performance, build quality and powder bed integrity were all within the requisite parameters for a “good build”. Some very minor discrepancies were noted, which we hypothesized could be down to a change of the material lot.
What have we learned?
Through this research we’ve determined that, from a build quality perspective, it doesn’t matter which combination of metal powder and recoater you use. What matters is the intended purpose of the part you’re creating. Each of the metal powders and recoaters tested offer benefits for different practical applications. Using the right metal for the right part is the primary objective, while using a recoater that allows the part to perform at its best follows in a close second.
From the small imperfections that were noticed, we are now curious to continue our research to see how any potential contamination from changing powders and recoaters in the 3D printer may affect the performance of parts built from one job to the next. This is what our next phase of research is going to focus on: Performing chemical analysis on the parts and powder bed to see if there is any contamination, and determine whether this affects the longer term practical applications of parts built using different recoater-powder combinations.
Find out more about the details of our research into the build quality of various metal recoater-powder combinations by downloading our whitepaper.