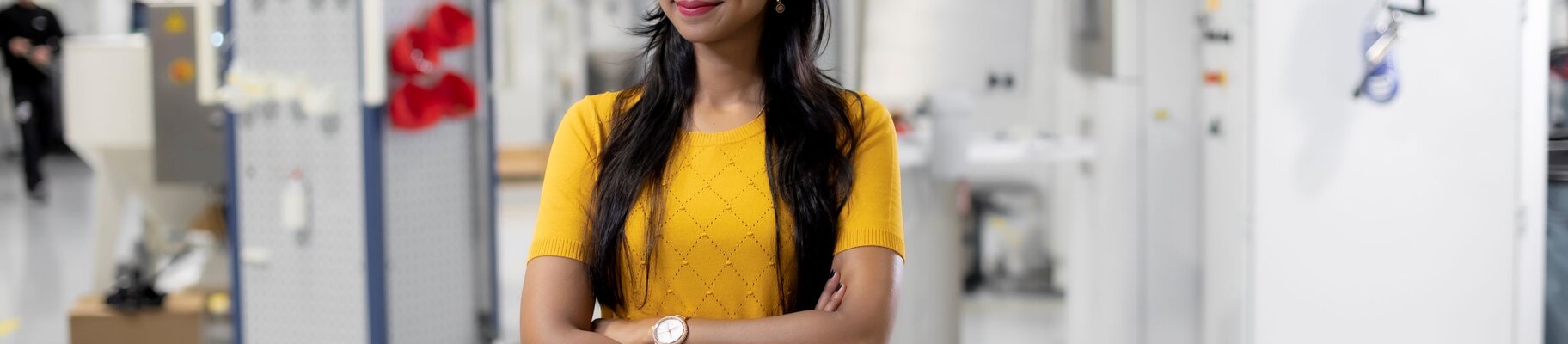
Top 5 Biggest 3D Printing Misconceptions
MAY 08, 2023 | Reading time: 3 min
Even though 3D printing first made its debut in manufacturing over 35 years ago, it is often still perceived as an emerging technology. While it is certainly a futuristic one and has many more developments in store over the next several decades and beyond, it is far from a ‘fast fashion’ manufacturing technology. As an industry leader in industrial 3D printing, EOS is often met with 3D printing misconceptions or myths when educating the market about our technology. Here are a few we hear often, and the proof behind why they are in fact misconceptions.
#1: 3D printing is replacing traditional manufacturing
Although according to Forbes, additive manufacturing (AM) is among the ten biggest future trends for the manufacturing industry and is continuously being looked to for rapid prototyping and complex application production, it will never completely replace traditional manufacturing. Manufacturing processes such as injection molding, machining, and casting are economical and speed-oriented production tools able to mass produce with minimal cost and labor. AM has many benefits but is meant to be used alongside other manufacturing methods, rather than replacing.
Where do the strengths lie in traditional vs. additive manufacturing?
Traditional manufacturing’s mass production capabilities provide a more economical method of production for high-volume, low-cost products. For example, consumer goods such as solo cups or soda bottles are unlikely candidates for industrial 3D printing because of the production volumes needed and the uniform design and manufacturing.
Although additive manufacturing can be a higher cost option for large-volume manufacturing, AM has the benefits of customization, part consolidation, and speed-to-market rapid prototyping which allows businesses more freedom and individualization with production. Customization, often a buzz word in 3D printing, allows companies to cater to their consumers in a way traditional manufacturing is unable to match.
#2: 3D printing is only for rapid prototyping
3D printing is used for rapid prototyping, and has seen immense success in decreasing production time for developers and speed-to-market – but it is not the only benefit of leveraging AM. Other benefits of 3D printing include:
-
Ability to produce complex geometries - Complex application geometries can be impossible to produce with traditional manufacturing techniques, such as milling, turning, or casting. When they are possible, the cost-per-part does not make economic sense. AM gives engineers incredible design freedom to create applications with complex geometries – unique, organic, and AI-derived – without increasing production costs for your business.
-
Ability to mass customize and manufacture on demand - Evolving consumer expectations and market demands are changing the deliverables expected of manufacturers in the automotive, consumer goods, and medical industries who now find themselves under pressure to deliver customized products. In other words, production capabilities must be tailored for a single- or small-batch production with design requirements defined by everyone. The economics of traditional manufacturing methods do not allow for this.
-
Ability to prioritize sustainability and reduce the carbon footprint– Subtractive or traditional manufacturing is inherently wasteful, as it requires cutting or shaping a block of material into a finished part or product, while AM uses only the amount of material it needs to manufacture an object, and leverages material recyclability and carbon neutral materials to reduce the impact on our carbon emissions and greater environment.
#3: All CAD files are 3D printable
Computer-aided design (CAD) files are used for designing and drafting applications digitally. There are many strategies and tools that assist with converting CAD files to stereolithography (STL) files with the assistance of slicing software, but often, they are not perfect in converting the files and leave elements of the application weak due to the difference in manufacturing strategies.
For example, a CAD file for a metal application with overhangs of less than 45 degrees that has been converted to an STL file would not automatically produce a successful application. Although the EOS Additive Minds consulting team has made great strides in support-free 3D printing, an application without built-in support structures for acute overhangs and angles would not be printed correctly without added AM design elements.
#4: All 3D printers are alike
Although 3D printing technology is rooted in the same methodology, there is a vast range of 3D printing solutions, styles, and sizes. There are seven main types of 3D printing processes currently used for both metal and polymer additive manufacturing:
-
Material Extrusion
-
Vat Polymerization
-
Powder Bed Fusion
-
Material Jetting
-
Binder Jetting
-
Directed Energy Deposition
-
Sheet Lamination
There are also varied sizes of 3D printers, from desktop printers such as FDM (Filament Deposition Molding) printers that can be bought and used by everyday people, to industrial 3D printers such as EOS powder bed fusion systems that require professional AM education and training.
#5: AM is too expensive
Additive manufacturing, specifically metal industrial 3D printing is often met with the misconception that it is too expensive for businesses to leverage within their production process. While it is true that industrial-grade metal 3D systems are not regarded as ‘cheap’ from a business standpoint, they are also part of a much larger production equation.
Supply chains have become so far-reaching and extensive that investing in AM can often help organization’s bottom lines, rather than add another expense to them. Onshoring manufacturing with AM allows for less warehousing, less shipping, and more sustainable parts being delivered on time.
To learn more about how AM can help save money in your business, read Glynn Fletcher, President of EOS North America’s article, “Additive Manufacturing: Key to Unlocking Supply Chain Resiliency” here.
To sum it up, there are many misconceptions about industrial 3D printing, and as an industry, we recognize that we are not the one-stop shop for all manufacturing needs. But there are many benefits to industrial 3D printing and ample resources to assist with enabling your organization to succeed.
If you are interested in speaking with an AM expert about the possibilities of 3D printing for your production and prototyping needs, book a meeting with an Additive Minds consulting team member today. Whether your questions stem from specific part design or just general curiosity about the industry, our team can assist and provide advice for all your 3D printing questions.