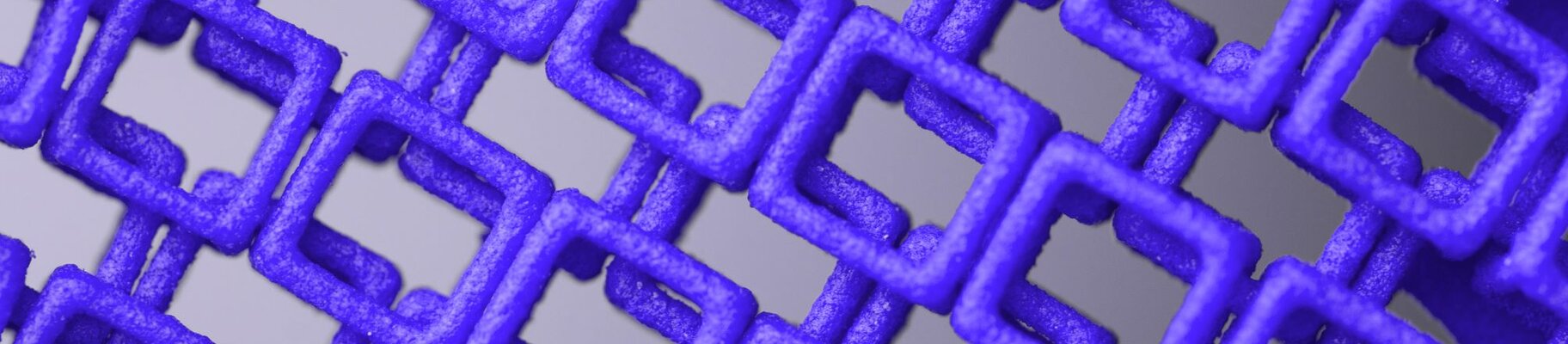
Design for Strength and Intricacy with Fine Detail Resolution
January 10, 2024 | Reading time: 5 min
FDR Makes Intriguing Possibilities into Realities
FDR enables you to produce polymer parts of astonishingly intricate designs, with remarkable detail accuracy and impressive robustness. Fine detail resolution (FDR) technology facilitates the production of complex and remarkably detailed parts - even at fingertip-sized dimensions - without sacrificing durability. Designers and engineers have exceptional freedom even for use cases that require incredible delicacy and precision. FDR is ideal for additive manufacturing (AM) use cases that demand extremely intricate detailing or structures, which might otherwise be challenging for AM designers and engineers.
Designers can craft complex parts based strictly on their end-use requirements, without any fear that the technology will be detrimental to their creative vision. Engineers, meanwhile, need not worry that seemingly tiny dimensions will impede the function of finished parts.
Notable design possibilities FDR allows you to realize


High dimensional accuracy
Because of FDR's ultra-thin CO laser beam, the process's accuracy is comparable to stereolithography (SLA) — at far more efficient production rates. FDR's accuracy allows you to design parts with elements such as:
- Intricate, clear lettering in embossed or debossed fonts to mark or label parts
- Exceptional fits for parts like housings or components that belong to an assembly
- Accuracy to +/- 40 microns, comparable to injection molding
- And more!
Complex yet robust features
With FDR, you can easily manufacture ultra-thin threads, intricate lattice structures, complex interlocking components like meshes or high-level functional connections like cantilever snap-fits — all at miniaturized dimensions and with the assurance that they'll be sturdy once produced.
In addition, parts can be customized to meet the needs of the user, object of utility or desired functionality at no additional integration cost. This allows for a high degree of design freedom.
FDR also improves part robustness: The strength of the PA 11 polymer used in FDR ensures that while even tiny features like pins may deform somewhat under pressure, they aren't fragile enough to break.
Ultra-thin wall thickness
FDR allows designers to produce parts with vertical walls as thin as 0.26 millimeters (as long as they have at least one contour) and horizontal walls that are even thinner (about 0.12 mm minimum).
Engineers will find this attribute of FDR ideal for components used in high-frequency telecommunications, like digital filter units for microwave antennas. Advanced areas of the automotive industry — such as autonomous driving — and aerospace could also benefit from components with thin walls but sturdy composition.


FDR Design Best Practices
Many factors come into play when designing parts for FDR. But the following four principles provide a firm foundation you can always turn back to — even when entrenched in the minutiae of calculating hinge gap sizes, hole diameters, beam offset and various other values.
- Function above all
Focus on a part's intended function, not its manufacturability. For example, imagine you're designing a microelectronic connector: Pay strict attention to whether your intended dimensions allow it to successfully connect to its counterpart, and don't worry about FDR's ability to realize those dimensions. - Minimal material
Design your parts so they only require enough polymer to serve core functions. Using more material than necessary is simply wasteful when you have FDR, given the technology's ability to create functioning end-use parts at a minuscule scale - Force-flow design
Unlike traditional manufacturing, force-flow-based design is possible with AM. For our purposes, this means you only need to require enough material to meet a part's strength requirements. This helps save material and enables more responsible manufacturing. - Soft edges and corners — not sharp
FDR enables you to shape polymer in about any way you can imagine, But in part design, "can" doesn't always mean "should." Eliminating sharp edges or corners during design ensures they won't be potential problems later in the AM life cycle.


Take the Plunge Into FDR's Possibilities
Everything above just scratches the surface of FDR and the particulars involved in part design for this cutting-edge additive manufacturing technique. For a more comprehensive picture, watch our on-demand webinar. In less than 30 minutes our experts will tell you how you can unleash the power of FDR 3D printing to diversify your application portfolio.
