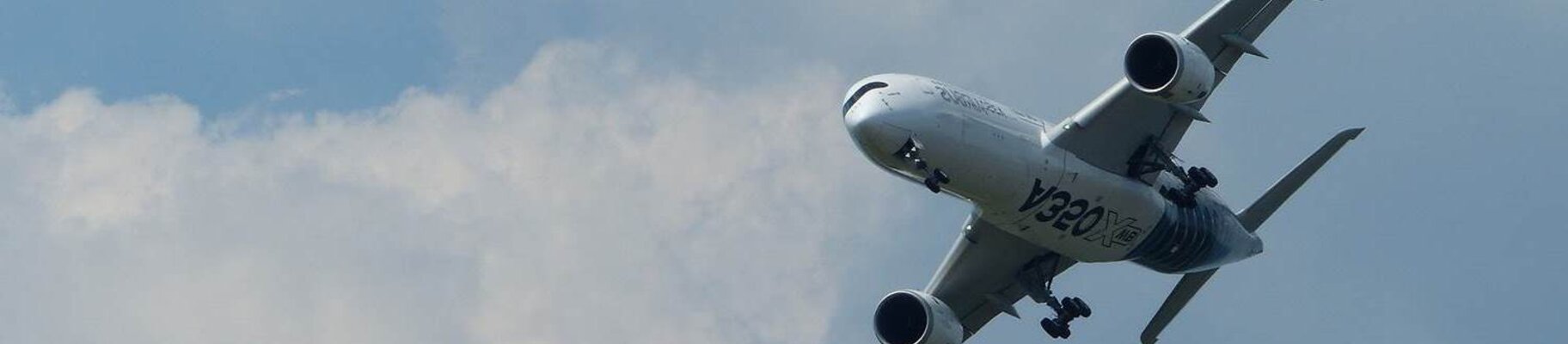
Sogeti High Tech Additive Manufacturing for the New Airbus A350 XWB
A350 XWB Cable Routing – From Design to Component in Two Weeks | Success Story
The moment when a completely new commercial aircraft takes to the skies for the first time is always special – and this was especially true of the Airbus A350 XWB. As a child of the new millennium, it was clear from the very beginning that development work would focus on innovative materials and production processes – the goal was no less than to build the world's most efficient aircraft. As a technology of the future, additive manufacturing was another possibility that needed to be considered during development. As part of a pilot project, experts from Sogeti High Tech succeeded in developing a cable mount on the front spar of the vertical stabilizer for the passenger aircraft in record time, taking only two weeks from the initial sketch to the finished part. EOS technology and expertise was a pivotal aspect of this development process.
"Getting an existing component 'AM-ready' in just two weeks meant that we had to succeed at the first attempt. The excellent, proactive collaboration with EOS made this ambitious undertaking possible – with outstanding results."
Carlos Ribeiro Simoes | Additive Manufacturing Offering Leader | Sogeti High Tech
Challenge
Time-critical development and production of a cable routing mount for a camera in the vertical stabilizer of the A350 using additive manufacturing
The project specifically involved producing a cable routing mount for the latest Airbus model. The mount was ultimately needed for the power supply and data transportation of a camera located in the vertical stabilizer, providing a view of the outside to passengers and orientation on the ground to the pilots.
The product requirements document called for a functionally operational component suitable for series production. This task was entrusted to Sogeti High Tech, a wholly-owned subsidiary of Cap Gemini S.A., which is listed on the Paris stock exchange.
The particular challenge in this case was the short lead time of just two weeks. The entire development had to be completed within this time frame: From analysis of the part and of the current installation set-up, a parameter study aimed at optimizing the topology and its interpretation, and the design and production of the finished part. The mount also needed to have as few support structures as possible to avoid post-processing.
In addition, the specifications for the component called for integration of the snap-on cable holder, weight reduction, and compliance with the strict requirements for subsequent aviation industry certification.
The conventionally produced component was made up of formed sheet metal parts and numerous rivets – more than 30 individual parts in total. The plug connectors in the upper area were made from plastic, and thus from a different material than the other individual parts of the mount. The aim was to develop an integrated solution consisting of a single part that also included the plug connectors, thereby significantly reducing construction and installation times. The weight reduction target for additive manufacturing was determined by a parameter study based on topology optimization.
Solution
Reduction to a single component and manufacturing on an EOS M 400 minimizes production time to 19 hours
For the new component, Sogeti High Tech followed the tried-and-tested development process for designing additively manufactured parts. The project kicked off with an analysis of the existing, conventionally produced component in terms of the upcoming manufacturing process – with an extremely positive outcome. The component's functionality, material, and previously complex structure made it an ideal candidate for powder-bed-based 3D printing technology from EOS. The design freedom offered by this technology allows complex structures to be produced in a single piece, meaning that a weight-saving design can be selected without neglecting functional integration.
This analysis then allowed the so-called design space – the space that the cable-routing mount may occupy – to be defined. The aluminum alloy AlSi10Mg, which is ideal for thin-walled, complex structures, was chosen as the material. The interfaces to the external areas remained the same, forming the non-design space, meaning that no changes needed to be made to them. The defined loads were taken as the boundary conditions for topology optimization in the parameter study, providing the basis for a new design.
As is customary, CAE software was used for the topology optimization calculations; in by contrast, a dedicated solution for designing structures with free-form surfaces was used for the re-design. Sogeti High Tech created the design itself. In order to meet the lead time of two weeks, EOS calculated the build time and optimized parameters from the topology optimization results using the software EOSPRINT. This created the CAE implementation for the manufactured part while also taking into account the possibilities and limitations of the manufacturing process and the need to avoid support structures.
"In addition to outstanding hardware, EOS also offers comprehensive expertise in making additively manufactured components reality – something that we rate very highly."
Carlos Ribeiro Simoes | Additive Manufacturing Offering Leader | Sogeti High Tech
Results
Thanks to the cooperation between Sogeti and EOS, it was possible to develop a component optimized for additive manufacturing that fully exploits the design freedom afforded by DMLS technology while at the same time taking account of its restrictions. This allowed plug connectors for cable routing to be integrated into the design and local reinforcement to be incorporated in specific critical areas in order to optimize the structure. Self-supporting apertures and struts within the component help to keep the effort and hence the post-processing costs to a minimum.
Additionally, the mount can be produced extremely fast, whenever it is needed. Manufacturing – which is performed on an EOS M 400 with layer thicknesses of 90μm – only takes 19 hours instead of the 70 days previously required.
This corresponds to a reduction in the production time well in excess of 90 %. This is largely because the many individual steps and formerly 30 parts have been brought together in a central component that can now be produced in a single run. In addition, the individual parts no longer need to be constructed and held in stock, which can be expensive. Storage for the entire component assembly is now also much more straightforward.
Sogeti was not only able to save a huge amount of time in production, but also in development. The entire process from the initial sketch to the finished component took only two weeks. This is a phenomenal lead time. At the same time, the design also means greater weight efficiency.
Whereas the conventionally manufactured original part weighed 452 grams, the additively manufactured cable mount weighs just 317 grams – and it is well known that the aviation industry counts every single gram in the interest of cutting fuel consumption to a minimum. The customer, Airbus, was more than satisfied with the results.
The Result at a Glance
- -29 Single Parts Functional integration
- -90% Reduction of production time
- -135 Grams Reduction of weight
Discover More
Explore three decades of pioneering 3D printing excellence with EOS