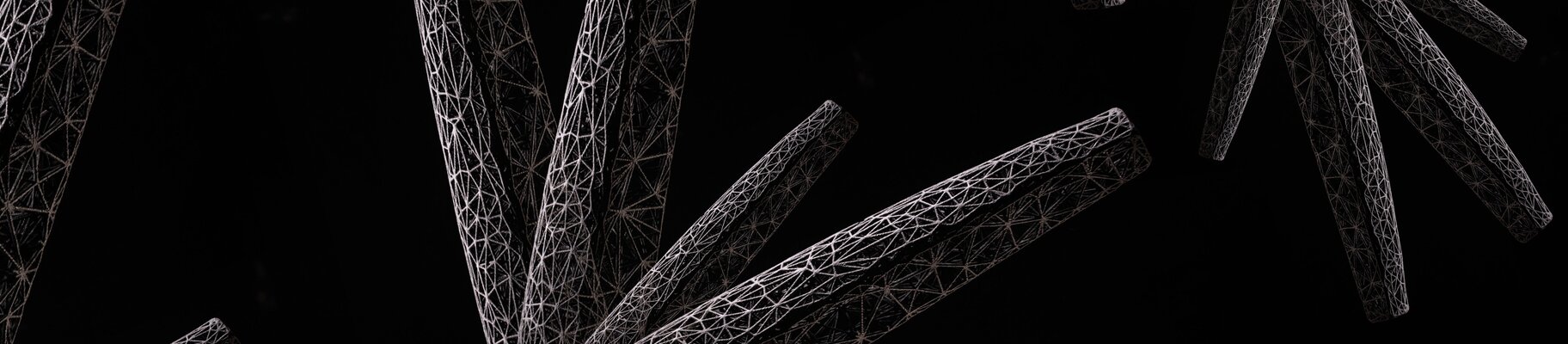
First-Ever Automated AM Production Line for Scalable Polymer Parts at BMW Group
The POLYLINE project proves successful for BMW Group through next-generation digitalized production line development, complementing conventional production techniques with additive manufacturing (implemented by DyeMansion, EOS and Grenzebach).
____ Krailling, Germany, November 2, 2023
The POLYLINE project achieved the first successful implementation of an automated additive manufacturing (AM) production line for polymer parts at scale. At the Additive Manufacturing Campus of BMW, the projectpartners made 3D printing serial production a reality with high throughput. Therefore, it is no surprise that after the defined three years of project time, BMW, DyeMansion, EOS and Grenzebach – four partners of the consortium – draw a positive balance.
"The successful POLYLINE project shows that an end-to-end automated factory is possible with 3D printing – and this is just the beginning."
Philipp Kramer, CTO and co-founder of DyeMansion
"The POLYLINE automated process chain fits into the next generation printers and our standard production requirements, is a system-agnostic solution due to their standardized interfaces. Which is crucial for scaling up additive manufacturing."
Dr. Blanka Szost-Ouk, head of additive manufacturing, predevelopment & planning at BMW Group
"The main advantages of automation are to increase the productivity of the equipment, to reduce the downtime of the equipment, and to create a safe work environment for the employees."
Oliver Elbert, head of additive manufacturing at Grenzebach
"The successful POLYLINE project shows that an end-to-end automated factory is possible with 3D printing – and this is just the beginning."
Philipp Kramer, CTO and co-founder of DyeMansion
"The POLYLINE automated process chain fits into the next generation printers and our standard production requirements, is a system-agnostic solution due to their standardized interfaces. Which is crucial for scaling up additive manufacturing."
Dr. Blanka Szost-Ouk, head of additive manufacturing, predevelopment & planning at BMW Group
"The main advantages of automation are to increase the productivity of the equipment, to reduce the downtime of the equipment, and to create a safe work environment for the employees."
Oliver Elbert, head of additive manufacturing at Grenzebach
How the AM Lighthouse Project Worked
The Roles of BMW, DyeMansion, EOS & Grenzebach
BMW, the premium automotive manufacturer, has given the project a home in its Additive Manufacturing Campus in Munich and has taken over the coordination of the different project partners.
EOS, the world's leading technology provider in industrial 3D printing of metals and plastics, was responsible for the printing with its EOS P 500 which sets a new standard in terms of industrial additive manufacturing. It can be fully automated and fully integrated. The level of automation and integration then differs from the use case and can be adjusted specifically to each situation. The machine ensures the highest reliability, the highest level of homogeneity, repeatability, and reproducibility.
As a specialist in the automation of industrial processes, Grenzebach contributed its expertise in the intelligent and safe networking of manufacturing processes to the project. This includes the Exchange P500/4 solution, which is placed directly in the printer and automatically replaces the exchange frame and cools the build jobs in the buffer stations. The automated transport of the exchange frame to the next stations with the secure transport container and an automated guided vehicle (AGV). And the robotic cell with KLT handling and bin-picking robots for further processing and sorting of components. In addition, the joint development of automated hardware and software interfaces suitable for industrial use in all process stations was a vital component of the Grenzebach work package.
DyeMansion, the global leader in post-processing solutions for industrial polymer 3D printing, was responsible for delivering the right look and feel for the final application – to all areas of post-processing: cleaning, surfacing, and coloring. DyeMansion’s processes are completely traceable, ensuring consistent quality. The Powershot DUAL Performance fulfills all requirements for physical automation, so it can run batch after batch continuously without the need for an operator to be present.
Together with all other project partners and thanks to the funding by the German Federal Ministry of Education and Research, BMW, DyeMansion, EOS and Grenzebach achieved to develop a next-generation digitalized production line.
Quotes from BMW, DyeMansion, EOS & Grenzebach
"Current printers are fast -- soon, they will be even faster. Therefore, logically the cost per part per unit will be cheaper, but printed jobs would have to be changed more frequently. To be human-centric we need to put the people in the middle of our process chain and make it effective, cheap, and simply excellent for happy and motivated people.
The POLYLINE automated process chain fits into the next generation printers and our standard production requirements, is a system-agnostic solution due to their standardized interfaces. Which is crucial for scaling up additive manufacturing at the BMW Group."
Dr. Blanka Szost-Ouk, head of additive manufacturing, predevelopment & planning at BMW Group
______________
"Automation is one of the key drivers in our strategy, making it possible to integrate our systems in automated production lines like POLYLINE. And this is important to reduce costs per part and ensure the right quality throughout the whole production chain.
Enabling serial manufacturing is one of the main reasons why DyeMansion was founded, and that is what our systems are built for, to get post-processing to this level. The Powershot DUAL Performance was built for scale, so it can serve ten or even more printers in production and therefore make an end-to-end factory possible. The main takeaway here is that an end-to-end automated factory is possible with 3D printing. The successful POLYLINE project shows what is possible and this is just the beginning."
Phillip Kramer, CTO & co-founder of DyeMansion
______________
"The target of the POLYLINE project was to develop a fully automated selective laser sintering production line. As an automation company, our part was to develop the layout of the line, provide the automation equipment for the transport between the different machines, and create the machine interfaces together for our project partners. The main advantages of automation are to increase the equipment's productivity, reduce its downtime, and create a safe work environment for the employees.
Automation is essential for serial production to increase the productivity of the equipment and to reduce the cost to become more compatible to the conventional production technology of today."
Oliver Elbert, head of additive manufacturing at Grenzebach
______________
"The EOS P 500 sets a new standard in terms of industrial additive manufacturing. It can be fully automated and integrated. The level of automation and integration then differs from the use case and can be adjusted specifically to each situation. The machine ensures the highest reliability, the highest level of homogeneity, repeatability, and reproducibility.
Besides a prominent level of automation and integration, the EOS P 500 provides a superior level of flexibility. It offers different modes of operation and has a one-click mode of operation for shop floor execution as well as an all-access operation for manufacturing engineers. Using industry-standard APIs for software connectivity, hardware automation and integration, the EOS P 500 can be integrated into industrial environments."
Fabian Krauß, head of polymer systems at EOS
About the POLYLINE Project
The POLYLINE project brought together 15 industrial and research partners from Germany to develop a next-generation digitalized production line. This line has been used to produce plastic parts for the automotive industry. The aim was to complement conventional production techniques (e.g., machining, casting, etc.) with Additive Manufacturing (AM) in the form of high-throughput production line systems. The project was funded by the German Federal Ministry of Education and Research with a total of 10.7 Mio. Euro. The project had a defined duration of three years. After the successful completion of the POLYLINE project BMW, DyeMansion, EOS and Grenzebach – four partners of the consortium – drew a positive balance. Learn more about the POLYLINE project by watching our new video here.

About the Companies
BMW GROUP – ADDITIVE MANUFACTURING
With its BMW, MINI, Rolls-Royce and BMW Motorrad brands, the BMW Group is the world's leading premium manufacturer of cars and motorcycles and a provider of premium financial and mobility services. The BMW Group production network comprises 31 production and assembly plants in 15 countries; the company has a global sales network with representatives in over 140 countries. The use of 3D printed parts is becoming increasingly important for the BMW Group. In the past ten years alone, the company has produced more than one million components for use in, for example, test vehicle construction and end-customer vehicles. As part of POLYLINE, the BMW Group is drawing up a catalogue of requirements to ensure that the production line developed meets the standards of the automotive industry and can therefore be integrated into existing production structures. In the future, the demonstrator line will be set up on the new Additive Manufacturing Campus near Munich. There, cause-and-effect relationships will be jointly researched as part of the project. You can find detailed company information at: www.bmwgroup.com
BMW Group Contact
Benedikt Torka
Media Relations Manager Production Network
+49 151.601.32455
Benedikt.Torka@bmwgroup.com
______________
DyeMansion
DyeMansion is the global leader in post-processing solutions for industrial polymer 3D-printing that turns 3D-printed raw parts into high-value products. From perfectly fit eyewear to personalized car interiors, their technology makes 3D-printed products become a part of our everyday life. Starting in 2015 with the first industrial coloring solution for powder bed fusion parts, the Munich-based company extended its portfolio with advanced part cleaning and surfacing solutions for a wider range of 3D-printing technologies in the field of plastics. Today, DyeMansion’s Print-to-Product workflow combines industry-leading hardware with the widest range of color and surfacing options on the market. Their systems are applicable for Industry 4.0 and can be integrated seamlessly into various production processes. The ability to provide a flexible solution for both small batches and high volumes makes DyeMansion a trusted partner for future factories. Through close collaboration with customers across all industries, the 3D-finishing technology and expertise continuously grow with the market. Reduced cost per part, unmatched quality, and high sustainability are core values that drive each innovation of the fast-growing company. In addition to these principles, finding the right finish for every application is what drives them. Learn more about DyeMansion and visit www.dyemansion.com, LinkedIn, Instagram, Twitter or YouTube.
DyeMansion Contact
Robert Simbeck
+49 89.414170500
robert.simbeck@dyemansion.com
______________
Grenzebach
As a specialist in the automation of industrial processes, Grenzebach is contributing their expertise in the intelligent and safe networking of production processes to the project. In cooperation with the partners, Grenzebach takes over responsibility for the material flow and transport between the individual processes. A vital component here is the joint development of automated hardware and software interfaces towards all process stations suitable for industrial use. Overall aim is to develop a holistic automation concept for the pilot line. Further information can be found at: www.grenzebach.com
Grenzebach Contact
Franziska Gellner
Corporate Marketing & Communications
+49 906.982.2000
Franziska.Gellner@grenzebach.com
______________
EOS
EOS provides responsible manufacturing solutions via industrial 3D printing technology to manufacturers around the world. Connecting high quality production efficiency with its pioneering innovation and sustainable practices, the independent company formed in 1989 will shape the future of manufacturing. Powered by its platform-driven digital value network of machines and a holistic portfolio of services, materials and processes, EOS is deeply committed to fulfilling its customers’ needs and acting responsibly for our planet.
Downloads
-
POLYLINE Project Press Release Image 1
JPG 2,42 MB -
POLYLINE Project Press Release Image 2
JPG 2,08 MB -
POLYLINE Project Press Release Image 3
JPG 1,88 MB -
POLYLINE Project Press Release Image 4
JPG 1,65 MB -
Group of POLYLINE Project Partners
JPG 161,83 kB