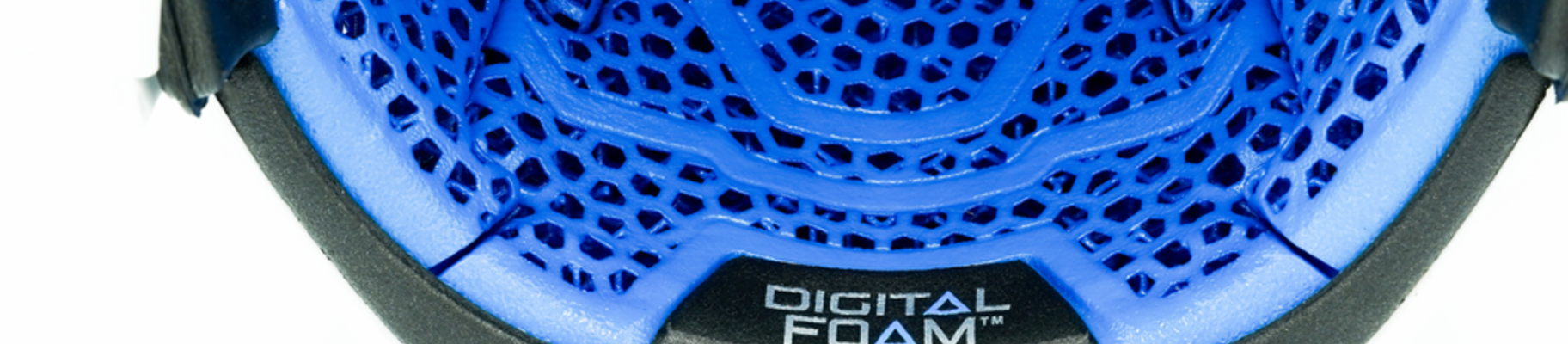
Digital Foam: A Revolutionary Polymer Solution Built with Your Design in Mind
MARCH 08, 2023 | Reading time: 5 min
The customizable design traits of Digital Foam introduce new possibilities for personalized products, light-but-strong components, superior protection, and individualized comfort. Read on to understand the Digital Foam process and how customers are leveraging it for increased customization and performance.
What is Digital Foam?
Organizations from a variety of industry sectors are now exploring how 3D printing enables never-before-produced product features like mass personalization and what benefits that may bring. EOS and its technology partners now offer Digital Foam™ to manufacturers seeking the expertise needed to quickly get their ideas off the whiteboard, to production, and into the market. Launched in 2019, Digital Foam gives access to critical design and additive manufacturing (AM) expertise and resources – streamlining product development, design engineering, and production, of clean-sheet applications that commonly leverage highly flexible polymer materials.
The 3D printing of materials is one key element, offering foam replacement options for industry-standard soft elastomerics including EVA and VN, as well as rigid materials including EPP and EPS. Moreover, digital manufacturing allows for unprecedented fine-tuning of each voxel (volume pixel) for superior comfort, safety, and performance characteristics. The process is a sophisticated endeavor that historically requires complex engineering and long cycle times to fully unlock its value – and one that Digital Foam solves, getting ideas to reality faster and providing a fast-track to production. Digital Foam is:
-
An innovative idea to leverage industrial 3D printing
-
Engineering experts leveraging powerful design software
-
Additive Manufacturing materials and technology – product and production development
-
Application Production: Go To Market
Today, historically commoditized applications are being reengineered and relaunched as high value consumer offerings – many times tailored to the individual with customized (personalized) features, or with improved functionality (comfort, safety, performance) that traditional manufacturing simply cannot replicate or meet the requirements for cost-per-part.
While explaining Digital Foam is important to understanding the basis of it’s intended purpose and capabilities, let’s explore our recent collaborative projects with companies such as Bauer Hockey and Wilson Sporting Goods that illustrate the use cases Digital Foam.
Bauer hockey MyBauer REAKT hockey helmet
Ice hockey helmet liners are an optimal example of a historically traditional product – evolving for more than 50 years, but until now, with minimal overall design changes. With new 3D printing technologies opening up product development doors and allowing for design limitations to be stripped away, the MyBauer REAKT hockey helmet with a Digital Foam insert was able to provide a new way of producing a more customized and individually tailored helmet product.
When global leader in hockey equipment innovation, Bauer, began investigating how to leverage and incorporate AM into their business, our Digital Foam approach to printing polymers stood to provide a distinct advantage for their product line and production. By leveraging Digital Foam, Bauer was able to bring initial prototyping of customized helmets to mass market for ice hockey – doing away with days of simply small, medium, or large offerings.
How it works
A player’s head is scanned, creating a digital file, which is then brought to life by utilizing Selective Laser Sintering (SLS) to 3D print a helmet insert with Digital Foam - involving a complex, varying lattice that is both personalized for the wearer for improved comfort and lighter weight. The RAEKT helmet weighs in at 580 grams, while also providing greater breathability and a truly customized fit to increase protection. Once printed, the helmet inserts are colored, finished, and readied for final assembly.
Whether elite athletes or pond hockey players, no two heads are alike. Bauer has now jumped in headlong into ‘mass customization’. Through our work with EOS and other partners, we are evolving MyBauer custom hockey equipment program to now include helmet inserts specific to the individual, but able to be produced at-scale. While Digital Foam is still relatively new, it keeps us out-front of product innovation while also bypassing other engineering and manufacturing limitations.
Mathieu Dejardins, Senior brand manager of protective equipment at Bauer Hockey
Wilson Airless Prototype
Another product that has stood the test of time with minimal changes is the basketball. With known performance and relatively low production costs, the basketball is easily overlooked for design updates. The Wilson Innovation Center is constantly seeking ways to revolutionize the sports equipment we use and enjoy every day, which is why they turned to EOS and Digital Foam for the Airless Prototype. By leveraging Digital Foam and our network of partners, Wilson was able to successfully produce an Airless Prototype, nearly equal in performance to a traditional basketball, with customized Digital Foam material, a digitally optimized lattice structure, and industrial 3D printing solutions such as the EOS P 396.
How it works
The Airless prototype leveraged expertise across members of the Digital Foam Architect Network – an overarching name for the company partners that worked with the EOS Additive Minds team to take the prototype from paper to product. While the material solution was optimized to meet process and performance targets, the Digital Foam Architect Network stepped in for additional elements of the application:
Advanced Laser Materials (ALM) – a polymer material development organization and sister company of EOS interpreted the performance goals of the ball and responded to further engineer the material and establish printing parameters to fit the Wilson innovation team’s specifications.
General Lattice – a computational design software company implemented precise lattice structure to mimic not only the visual aspects of a traditionally manufactured basketball, but the size, shape, and rebound.
EOS – Leveraging our own 3D printing technology, the EOS P 396 was able to take the design file from General Lattice and produce the prototype in a matter of a day, decreasing the time it takes to trouble shoot when prototyping and adjust based on performance testing.
DyeMansion – an AM post-processing technologies company provided the final appearance and haptics requirements of the ball via chemical vapor-smoothing and deep-dye coloring.
The airless prototype is the first of its kind in both the industrial 3D printing and sports equipment industries, showing the true innovation that is at our fingertips by leveraging additive manufacturing.
How to begin your Digital Foam journey
Has the capabilities of foam reached its maximum? The list of potential applications for Digital Foam is expanding in real-time. If mature applications, such as ice hockey helmets and basketballs, can be rethought, and re-engineered to create new market segments, Digital Foam can give engineers and product planners clean slates to transform an unlimited number of applications in ways never before possible.
3D printing Digital Foam applications can be a sophisticated endeavor and collaborating with experts who have the experience and expertise is an important consideration. I encourage you to reach out directly to us and we can work with your team from start to part.