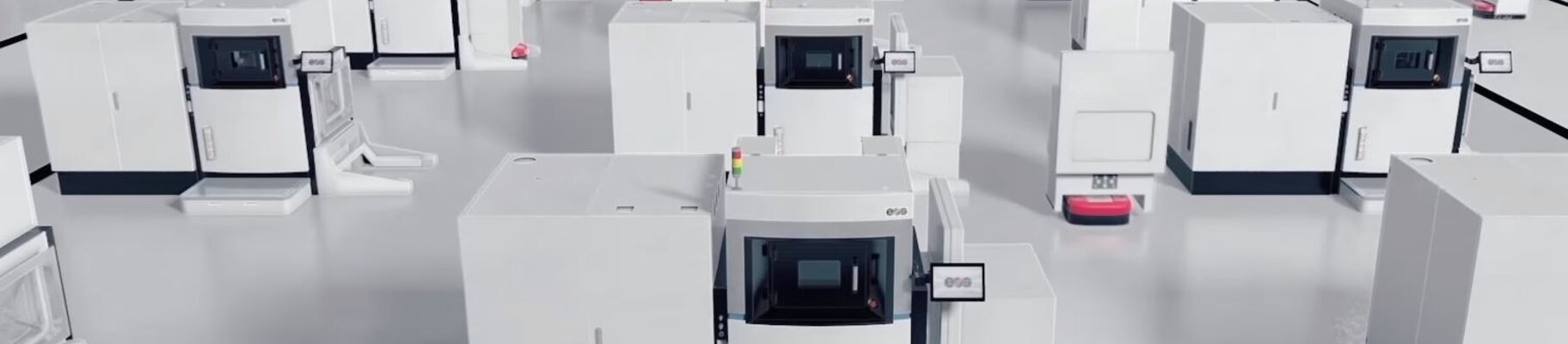
A Successful Factory Acceptance Test
April 05, 2022 | Reading time: 4 min
EOS metal and polymer systems have been manufactured and assembled at the EOS production site in Maisach since 2017. However, the production halls are not only used for assembly but also offer all services related to customer acceptance. Only when each machine has passed the comprehensive quality control is it shipped to customers worldwide.
From the production site in Maisach to the world
Around 90 employees work at the EOS production facility in Maisach. The production and training area comprises approximately 4,000 square meters. Another 2,000 square meters are available as storage space and for laboratories and workshops. Up to a thousand 3D printing systems per year can be manufactured here. Agile production processes and flexible production workstations enable the company to respond quickly and flexibly to new production, customer, and market requirements.
United under one roof, everyone works hand in hand to realize customer projects on schedule: Quality Assurance, Laboratory, Workshop, Warehouse, Production, and Technical Training. In addition, our Digital Manufacturing team is automating further the processes surrounding industrial 3D printing.
Final assembly, quality control, and acceptance
The main activity in Maisach is the final assembly of the EOS systems. The lasers and scanners are assembled and the software is installed. Then the system is calibrated. The assembly of smaller machines like the Formiga P 110 Velocis can be completed within one week. The assembly of larger platforms like the EOS M 400-4 takes a whole month. While smaller systems are assembled and stored, the large platforms are only produced on-demand.
There are over 370 EOS M 400 3D printers installed worldwide. This makes the EOS M 400 system family one of the most successful industrial 3D printers ever in terms of sales. However, this figure is only possible because we can now assemble up to nine EOS M 400 systems simultaneously in Maisach.
Only when each individual machine has passed the comprehensive quality control is it shipped to customers all over the world
Internal quality control and acceptance are among the most critical tasks at the Maisach site. It generally consists of two parts:
- the first part already occurs in parallel with the individual assembly steps. Our commissioning technicians check whether all components are functional and correct the respective parameters. This includes, among other things, the adjustment and calibration of the lasers and scanners. Our quality management documents each step in the test plans of our Computer Aided Quality Management Systems (CAQ) and decides on the system's release.
- in the second part, the machine is put into trial operation. Through a qualification job, the essential process suitability of the systems is proven. The qualification job contains various test parts for determining the relevant parameters. Such a test job takes between eight and twelve hours. The built parts are then tested for hardness, density, and roughness. Maisach has a laboratory team with its own rooms for these production tests.
The tests accompanying assembly ensure that all individual components function properly after the final assembly is complete and that the system can achieve the specified component quality.
Customized factory acceptance testing
Factory Acceptance Testing (FAT) is an additional, optional step at EOS to verify customer-specific requirements. It may involve unique measurements or build jobs. We advise the customer on what is reasonable and how to achieve the desired values or component properties.
In addition, the customer can come to Maisach himself to learn about the process on-site. Since 2021, we have also been offering factory acceptance testing with remote consultation of the customer by connecting him via live stream and letting him participate in what is happening via augmented reality glasses. He then receives all documentation of the internal and external acceptance testing.
Customers who go through this process can then be sure that the system meets all the requirements to start their planned production.