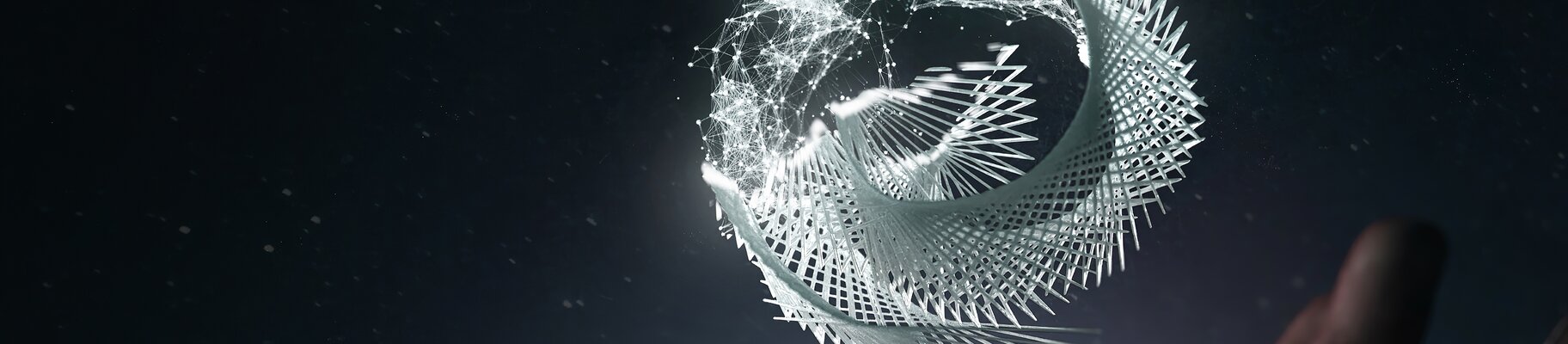
The Future of Additive Manufacturing
October 19, 2022 | Reading time: 5 min
Manufacturing has always been an industry driven by innovation and technological evolution. See how the manufacturing industry has evolved and find out what to expect in the future, so you can prepare for what’s to come.
A brief history and the latest trends
The manufacturing industry is experiencing a new wave of evolution. As the advancement of technology has accelerated, so too has the adoption of innovations in many different fields, and manufacturing is no exception. The driving force behind these advancements are many — from efficiency and cost-effectiveness to environmental and sociological. Understanding the motivation behind and the path ahead are both key to getting to grips with the latest trends in manufacturing, including being able to prepare for the future.
In this article we’ll take a look at the evolution of the manufacturing industry — past, present and future — to give you a better understanding of what the future is likely to hold for manufacturers, including where additive manufacturing fits into that future.
Major changes that shaped the industry
Since the industrial revolution in the 18th century, manufacturing has gone through several significant shifts and iterations that have led to the state of innovative growth now being experienced in the 21st century. Here is a short summary of the major changes that have shaped the industry:
The industrial revolution
The industrial revolution saw the development and refinement of machines such as steam engines, the spinning jenny and power loom in the textile industry and the coke-fueled furnace in ironmongery. The excitement and innovation stemming from such inventive times began the shift toward mass production, requiring a workforce to occupy factories where productivity became a primary concern.
The assembly line
Ransom E. Olds patented the assembly line in 1901. It focused on operational efficiency using the resources at his disposal to increase productivity by 500 percent. Not long after, Henry Ford found further ways to improve on the assembly line model by implementing moving platforms and focusing production on a single item: the Model T car. Not only did this make the production process more efficient, but it cut down on waste — still two of the major motivators of manufacturing innovation today.
The unified assembly line
Buick continued this philosophy of efficiency when it created the unified assembly line in 1919, making headlines as it was able to produce over 1,300 cars per day. It maintained quality standards while significantly cutting costs by creating a system of elaborate and intricately designed conveyors in one unified line.
Lean manufacturing
Toyota developed the lean manufacturing method in the 1940s, which focused on identifying and eliminating waste to improve the flow of production. In the 1970s the lean manufacturing model was adopted by businesses across the globe and a wide variety of industries — from electronics and aerospace to healthcare, construction and food — continue to use it as the basis for modern manufacturing strategies today.
Robotics
The latest trend to massively impact the manufacturing industry was the automation of many processes with robotics. Throughout the 20th and 21st centuries, robotics has progressively been incorporated into manufacturing operations in more ways. Automated software has been used to optimize planning, communication and management in factories, while robotic machines themselves are continually being created with greater capabilities to aid manufacturing operations.
Robotics represented the biggest leap for companies to move away from traditional manufacturing. So much so that the International Federation of Robotics reported 2.7 million robots working in factories worldwide in 2020 — a 12 percent increase over the preceding year. This progression has culminated in the age of smart manufacturing.
Throughout all of these manufacturing developments the underlying principle of elevating performance to greater heights has been at the core of innovation. It is the continued determination to excel beyond that which has come before, to not simply sit back and accept the status quo, that has driven the evolution of such exciting technologies. And this has led us to the current day, where we still look toward the future by exploring the possibilities of technologies at the forefront of shaping the future, like additive manufacturing.
The future of smart manufacturing
There are many trends in the advancement of modern technology that will shape the future landscape of smart manufacturing. At the core of these developments is the continued and increased use of robotics and artificial intelligence (AI) that becomes more accurate and predictive as it absorbs more data over time. When paired with collaborative robots (cobots), these digital technologies have been identified as a distinct contributor to the increased productivity of manufacturing operations. In fact, a 2019 Deloitte study found that early adopters of smart factory practices had seen a 3.3 percent gain in productivity between 2015 and 2018, reducing costs and increasing output for better bottom line figures.
According to Forbes, additive manufacturing is among the ten biggest future trends for the industry. Mass production using 3D printing isn’t just a conceptual idea for the future, though. It’s something that is actually being implemented within the manufacturing industry today. As more companies adopt this evolving technology its progress and development is only going to accelerate.
Further to being one of the key fields in the advancement of industrial manufacturing, 3D printing has the capacity to work in conjunction with and enhance other future trends. One of the biggest of these is sustainability. The demand for recyclable and reusable products has increased massively, leading manufacturers to explore ways to reduce waste while creating products and parts that are efficient and effective.
Additive manufacturing presents the most impactful method of production when it comes to sustainability. With additive manufacturing, companies can concisely produce batches of a product or part to only meet demand — reducing surplus, the need for storage and the amount of wasted items — while the amount of material wastage is significantly lower than in more traditional, subtractive manufacturing techniques.
Digital simulation in the design of products and parts is far from a new method for manufacturing. The predominance of product development is now done virtually, allowing engineers to push the boundaries of creation to achieve designs that would have been unfathomable under the constraints of traditional manufacturing practices. The methods of digital design and development complements the 3D printing process perfectly. Put simply, a computer-aided design (CAD) instructs a 3D printer to produce a precise physical model of that design.
Additive manufacturing is also a favored method for prototyping because of its reduced waste and expense impact. It allows organizations to fabricate and test multiple versions of a product during the development process at significantly lower costs than using traditional manufacturing methods. Hence why 3D printing is viewed as a smart manufacturing option for experimental industries such as aerospace, automotive and New Space.
The future of jobs in manufacturing
Automation may be evolving the manufacturing industry, but it hasn’t reduced the number of jobs in the field — simply changed them — according to Deloitte’s findings in its 2018 Global Human Capital Trends. It surmises that instead of there being less need for workers in manufacturing, there will be a need for different types of workers — those with specialized skills in digital technologies that can support and drive the production process of modern manufacturing operations.
Again, additive manufacturing is a strong example of how skilled professionals can bring their capabilities into an industry that is still expanding. Whether it’s in the design and virtual simulation of production, advanced machine operation or the application of engineering knowledge, fields such as 3D printing require workers with a wide range of skills to achieve the successful creation of parts and products.
Embracing and preparing for the future of manufacturing
Manufacturing is a field that is continually evolving. In order to remain competitive, manufacturers need to keep up with the changes happening in the industry, embracing the latest digital technologies and striving for greater operational efficiency. For many organizations, this will mean adopting production equipment that reflects the most up to date methods of mass production, while populating workforces with trained technicians skilled in their operation.
One effective way to do this is by upgrading current equipment. Equipment upgrading for integration is a great way to balance initial costs because it means your workforce can continue using machines that they’re familiar with while opening up the possibility for advanced production techniques to be incorporated into the production process.
The more you embrace the latest trends such as automation, robotics and 3D printing now, the easier it will be to keep pace with the industry as these technologies become more widely available and used in mass production.
The best way to prepare for the future of manufacturing is to be willing to embrace its development as it’s happening. Early adopters of the latest trends benefit from being ahead of the game, so don’t wait to be left behind and have to play catch-up. Embracing the most advanced and exciting technologies being developed today — like additive manufacturing — will put you in good stead for the future of the manufacturing industry.
Autor: Fabian Alefeld