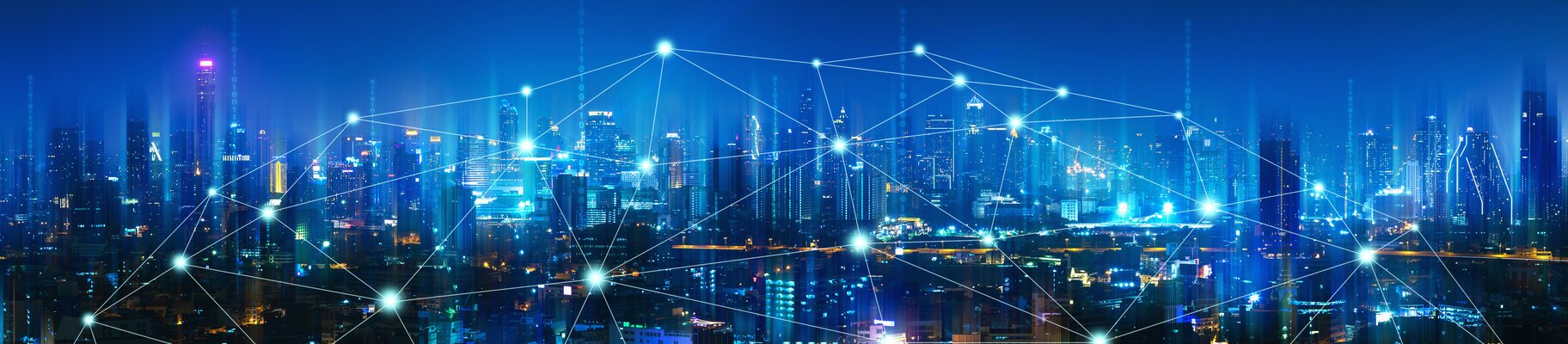
Additive Manufacturing is Key to the Future of Energy
September 30, 2022 | Reading time: 3 min
In a three-part special edition of the Additive Snack podcast from EOS, we dive into the role additive manufacturing technologies will play in the future of more powerful, efficient, and sustainable advancements in energy.
Additive manufacturing enhancements point toward reliable energy sustainability
Carbon dioxide (CO2) and other greenhouse gas (GHG) emissions are higher than ever amid increasing societal energy demands. But it's not yet feasible to abandon fossil fuels and instantly switch to renewables. Additive manufacturing presents itself as a technology with the potential to accelerate the development and deployment of innovative energy solutions to drive toward a carbon-free future.
Even if sustainable energy can't immediately replace fossil fuels, it's full of remarkable advancements, reducing fossil-fuel dependencies and helping support the foundation of a less "carbonized" world. These range from leading-edge wind-powered turbines and carbon-capture technology to working toward harnessing nuclear fusion as clean energy.
For the Future of Energy podcast mini-series, we spoke with experts across subsets of the industry, all of whom were enthusiastic about additive manufacturing's contributions to green energy. Simply put, it was one of the most intriguing series of conversations we've had the pleasure of hosting. Read on to learn each episode's major themes.
An additive approach to sustainability in natural gas
For Part 1, we spoke to Quan Lac, Siemens Energy VP of Additive Manufacturing, and Pierre Forêt, Linde Head of Additive Manufacturing. Both Forêt and Lac grew to realize that hydrogen is among the most potentially cost-efficient energy sources. Turbines powered by conventional natural gas can be converted to run partially or entirely on hydrogen, both of which are much more efficient than coal-burned gas or shale oil.
The difficulty of isolating hydrogen gas at high volume is easily one of the major stumbling blocks to its mainstream use: Electrolyzers separate it from water, after which it's compressed and routed to a turbine in need of fuel (or stored for later use). But the biggest electrolyzer ever — a machine with which Forêt is well-acquainted, as his team is building it — has a maximum electricity threshold of 24 megawatts. Suffice to say that is not sufficient power to electrolyze hydrogen and provide heat or power (or both) at large commercial and residential scales. As you might expect, these efforts are far from inexpensive — and this only compounds the challenge of turning hydrogen into a mainstream green power source.
Both Lac and Forêt use additive manufacturing in various hydrogenation projects. At Siemens Energy, Lac and his team have 3D-printed burner assemblies, combustion swirlers, ducts and other parts that cool air and mix fuel more quickly, allowing gas turbines to run hotter (and thus more efficiently). They're also engineering a prototypical integrated green energy system for an abandoned factory.
Meanwhile, Forêt and his colleagues at Linde use additive manufacturing to design parts with complex geometries simply impossible through conventional manufacturing, which is especially important to thermal management devices including heat exchangers, nozzles and connectors. Forêt noted that hydrogen is not the definitive clean energy solution, but says it will be crucial to decarbonization in numerous applications, ranging from steelmaking to aircraft manufacturing.
Responsible manufacturing in wind turbines and carbon capture
Jeremy Haight, principal engineer and lead specialist for additive manufacturing and advanced concepts at wind turbine manufacturer Vestas, explained to Additive Snack that his company started using AM for small-scale part replacement. Eventually, his team got to where major supply-chain shortages (e.g., those stemming from the COVID-19 pandemic) didn't significantly slow down Vestas' manufacturing process. Vestas is implementing laser powder bed fusion (LPBF) and other additive technologies to create drivetrain and electricity-generating components, among other parts. Haight said that because additive manufacturing allows for vertical integration and digitized inventory, it reduces construction costs and galvanizes sustainability efforts by reducing carbon output.
Meanwhile, Stefan McClelland, senior mechanical engineer at ReCarbon, is focused not on avoiding GHG emissions but trapping them (notably CO2 and methane) and transforming them into clean hydrogen-based fuel. Because the resulting gas burns at such a high temperature (2,000 degrees Celsius/3,632 Fahrenheit), only through additive manufacturing can ReCarbon efficiently create its proprietary "emission blades" and other key parts. The complex component geometries that only AM permits allow ReCarbon systems to direct the flow of gases during GHG conversion without sustaining heat-related damage. McClelland stated that while ReCarbon wasn't yet commercially ready, he was pleased with where their prototypes were, and bluntly said that "without additive manufacturing, we'd be dead in the water."
The dream of fusion energy moves toward reality
Slowly but surely, sustainable fusion-based energy is transforming from an impossible dream into a potential reality — with the help of additive manufacturing. For the Future of Energy finale, it seemed only fitting to recruit guests working toward that goal: TAE chief marketing officer Jim McNeil and senior mechanical and product engineer Vincent Pilard.
Not unlike using hydrogen gas, executing scalable fusion while mitigating radioactivity hazards has always held progress back. Temperatures within the sun, where nuclear fusion occurs every day, reach 15 million degrees Celsius (27 million Fahrenheit). As Pilard explained, practically replicating fusion on Earth would require temperatures between 100 million and 1 billion Celsius. TAE is using a proprietary technology called field reverse configuration, which confines plasma within magnetic fields. It currently maxes out at 75 million.
Neither of TAE's representatives downplayed how complex commercial nuclear fusion will be. But Pilard explained that additive manufacturing has already positively impacted their efforts and will continue to do so, such as with active cooling technologies: TAE completely redesigned a cooling component known as a "beam dump," making it lighter, more flexible and capable of greater cooling capability. This reduces material usage and boosts supply chain optimization. McNeil added that what TAE has done thus far — generations away from pure fusion though it may be — perfectly exemplifies how far additive manufacturing has come in its 40-year history.
Stay focused on AM with Additive Snack
These energy topics were undeniably complex, and the summaries above only showcase some of the most tantalizing bullet points from each episode. For the complete stories — as well as regular conversations on applications and advances within additive manufacturing — keep tuning into Additive Snack, available on all major podcast platforms.