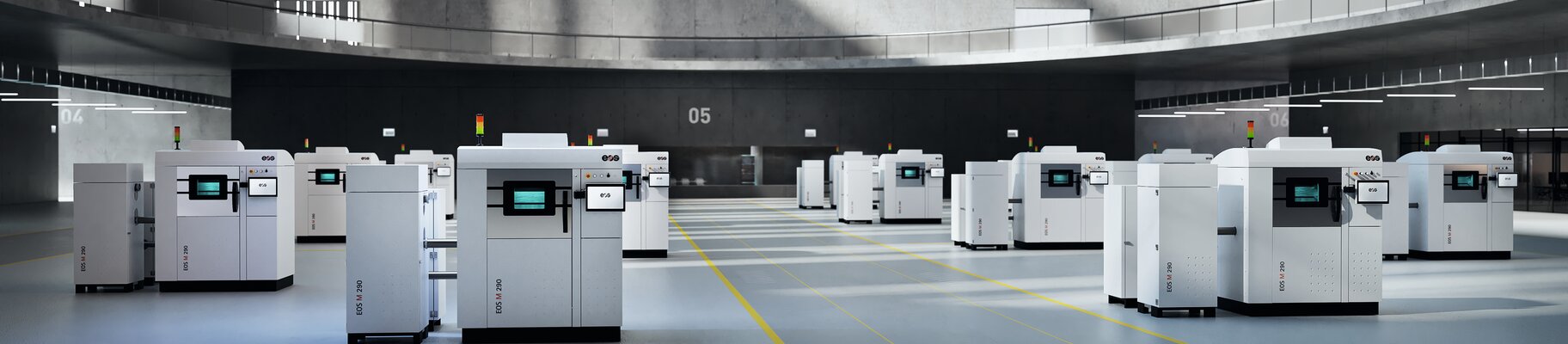
How to Bring a Part to Serial Production?
July 22, 2021 | Reading time: 6 min
Additive manufacturing (AM) has clear advantages compared to traditional manufacturing not only when it comes to design and weight, but also when considering the ecological footprint of manufacturing and vigorous supply chains. To release the full potential of AM, manufactures need to successfully integrate it into their production system.
Additive Manufacturing Qualifications in Regulated Industries
Along this journey, Additive Minds is continuously supporting customers through identifying the right application with a suitable business case, designing and developing optimal build parameters, and qualifying the application according to industry specific standards. Industries such as aerospace and health and medical technology are becoming adaptation leaders of AM. The use of AM in safety critical applications allows for high standards to set the precedent for excellent quality, safety, and reliability.
Qualification is the process of demonstrating that […] a process is capable of meeting […] the specified requirements
JEDEC, JEP 148, “Reliability Qualification of Semiconductor Devices Based on Physics of Failure Risk and Opportunity Assessment”, April 2004.
How does Qualification work?
“Qualification is the process of demonstrating that […] a process is capable of meeting […] the specified requirements” [1]. Every industry has a similar approach to conducting this requirement. Generally speaking, manufactures need to manage potential production risks and generate data which proves that the AM process can deliver repeatable results under predetermined conditions.
Let’s take a turbine blade as an example: A manufacturer needs to verify that the process is consistent and that the blades produced are going to withstand defined forces for a defined period of time (none of us wants to sit in a plane while a turbine blade breaks).
Qualification is usually a three-stage approach. At EOS, we commonly use the terms Installation Qualification (IQ), Operational Qualification (OQ) and Performance Qualification (PQ). Derived from the medical industry, these terms are now commonly accepted in AM industries as well.
Installation Qualification (IQ)
The IQ is part of a standard procedure offered by EOS. Field Service Engineers validate that on-site requirements of the machine and equipment are met and that the system’s core components are working according to EOS specifications. In addition, a test job for quality assurance is built and evaluated with the customer. All results as well as the calibrated tools used to complete the IQ are documented in a final report.
Operational Qualification (OQ)
The aim of the OQ is to verify that the production process is controlled and delivering the same results. In addition, the manufacturer needs to ensure all relevant parameters are maintained within a defined tolerance window.
An OQ is a highly customized process depending on industry specific requirements. Two steps are necessary to successfully complete an OQ:
Setting up the risk management system and conducting a capability assessment. As part of risk management, the manufacturer should identify and evaluate all related risks to the process that could affect part performance. This implies that the process is thoroughly defined (from incoming goods to post-processing) and that potential risks are recognized, evaluated, and mitigated. EOS customers are supported by Additive Minds through trainings and workshops where they are introduced to the relevant key process parameters and impact on the final part properties (e.g. critical to quality training, provision of an AM flow chart and process documentation).
In addition, customers often ask Additive Minds for additional technical information about systems, material and processes, but also how EOS runs internal procedures to ensure quality (e.g. how to ensure a consistent software validation prior to release).
The most important method to document and trace effectiveness of proper risk mitigation is a Process Failure Mode and Effect Analysis (pFMEA) which Additive Minds shares and customizes as part of an OQ project. Customers from regulated industries are required to provide proof to regulatory authorities that they have conducted this quality methodology to ensure that all development activities have been executed according to state-of-the-art procedures.
The purpose of operational qualification is to provide rigorous testing to demonstrate the effectiveness and reproducibility of the process. Process characterization to determine the process window for each of the key process variables is a pre-requisite.
ASTM F3434-20, Guide for Additive manufacturing - Installation/Operation and Performance Qualification (IQ/OQ/PQ) of Laser-Beam Powder Bed Fusion Equipment for Production Manufacturing
The most important method to document and trace effectiveness of proper risk mitigation is a Process Failure Mode and Effect Analysis (pFMEA) which Additive Minds shares and customizes as part of an OQ project. Customers from regulated industries are required to provide proof to regulatory authorities that they have conducted this quality methodology to ensure that all development activities have been executed according to state-of-the-art procedures.
Going back to our turbine blade: What should a pFMEA cover?
Lack of fusion is a defect which severely affects mechanical properties and should be avoided in safety critical applications. One possible reason this could happen is because laser power drops due to an unproperly cleaned laser window.
To minimize this risk, several mitigations can be implemented on the customer side. This might be a preventative work instruction to properly clean the laser window during machine setup, or even a CT-Scan of the final blade in order to detect and prevent any deviations.
The final step of an OQ is the capability study. The capability study follows a strictly pre-defined test plan (provided and customized by Additive Minds). Here, all relevant test parameters for all process steps are defined. This includes a process window for each parameter and acceptance criteria against which the initial design requirements are tested. To successfully pass the capability study, all acceptance criteria must be met, e.g. material properties as stated in datasheets or recognized as part of material standards (customers use these as reference point).
Many regulatory authorities (FAA/EASA of FDA/EMA) require customers also conduct Design of Experiments (DoE) to validate process performance under worst case or extreme process conditions.
Let’s have a look at our practical example!
ASTM F3434 requests that a manufacturer challenges all conditions which will be encountered during actual production, including "worst case" conditions. Because of this requirement several questions on customer side can arise. Since the manufacturer is fully responsible when introducing critical safety components to the market, it is necessary to answer these questions.
- How fast does the laser power of an AM machine degenerate?
- What are the main factors that can lead to a laser power loss?
- How much loss in laser power is acceptable until the application does not comply with the design requirements?
- How equally distributed is the laser power across the built plate and does, e.g. the f-theta lens have an effect on this distribution?
Once the OQ is completed, the manufacturing process must be qualified for a specific application, i.e. Performance Qualification.
The Performance Qualification (PQ)
The Performance Qualification is the final step in the qualification process. “This analysis will establish whether the equipment and process controls are adequate to ensure that the product specification is met” [2]. It provides the verification that all process steps, connected together, deliver the required specifications for the final part.
PQ can be a rather short phase within a qualification, as much of the extensive work has already been completed within the OQ. PQ finally adopts and compliments the generic process to a specific application, e.g. the turbine blade for a certain type of aircraft engine.
Like OQ, the PQ follows again a strict test plan – this time focusing on the part itself. The PQ defines operating parameters, equipment limits and component inputs. In serial production, this means e.g. the procedure how to handle, refurbish and reuse powder must be clearly defined and implemented.
In the case of the turbine blade production this has several implications: The manufacturer must define specifications for the recycled powder as well as instructions for how to execute the refurbishment. Limits should be established when the powder is scrapped as it needs to be ensured that the powder remains in a steady state and its status and history is properly documented.
How to keep the process qualified?
Once the qualification is completed, any change to the process should be evaluated by the manufacturer with respect to severity and potential effects on the final part. Based on this evaluation, different approaches for requalification may be applicable to keep the process qualified.
As a machine OEM, EOS cannot conduct this assessment. It is the responsibility of the manufacturer to do so. But by providing relevant information for this assessment, EOS can contribute to reducing customer efforts and fostering trust in the industrial grade of products, processes and organization. If customers can assess potential risks related to new features more easily, it enables EOS to quickly provide customers advanced, updated features and solutions.
Summary
Qualification is a common practice in serial production. The procedures and requirements towards AM are the same as any other production technology. Qualified products enable aerospace to be one of the safest means of transportation. This enables customers to qualify AM for serial production and to grow with EOS, pushing the deployment of AM technology into future.