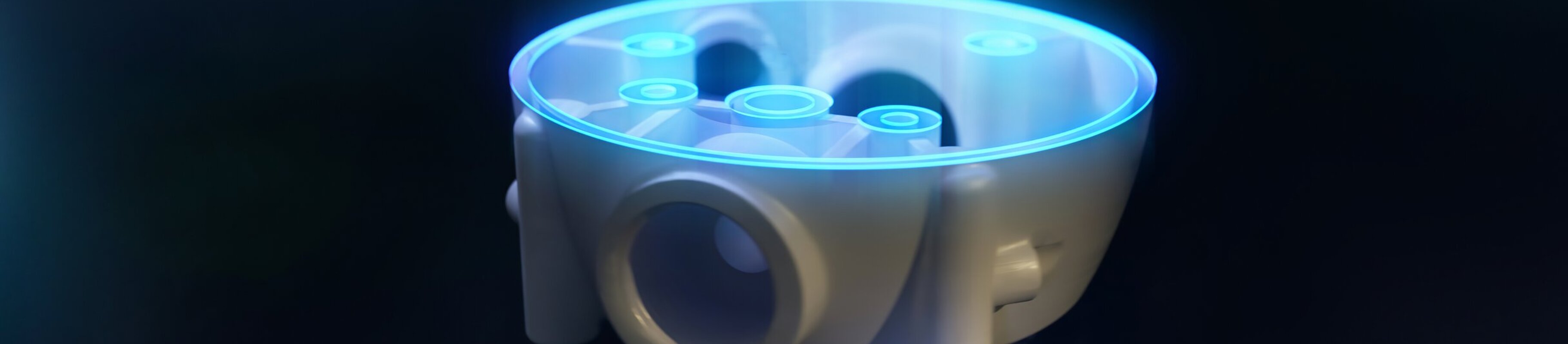
How Can Additive Manufacturing and Injection Moulding be Combined?
January 02, 2023 | Reading time: 5 min
It is possible to master the whole life cycle of your parts by combining additive manufacturing and injection molding. Take a look at our 3-step-process and download the whitepaper for more details.
Select the best of both worlds
Additive Manufacturing (AM) and Injection Moulding (IM) are often portrayed as two competing plastic processing technologies. Sometimes, AM is positioned as a disruptive production technology which takes market share from conventional offerings. However, Injection Moulding is a mature established technology, developed over nearly a century, that offers high quality and repeatability in mass production for various applications – batches of up to 10 million parts with a wide range of materials are realistic expectations.
Conversely, Additive Manufacturing enables users today to manufacture mass-customised parts, complex geometries, and small batch sizes of up to 200,000 parts economically with a fully digital value chain.
Advanced manufacturing has initially been defined as follows according to the European Commission:
“Advanced manufacturing uses new technologies and innovative and cutting-edge technologies such as robotics, 3D printing, artificial intelligence, high-performance computing and modelling, to produce complex products […]” Most sources highlight “a focus on innovation” as a core element in their definition. The authors of this paper extend the existing definition with the addition of the following: “Advanced polymer manufacturing refers to the ability to seamlessly switch between traditional and modern plastic processing technology to innovate throughout the product life cycle.”
The reality of achieving truly advanced manufacturing requires the combination of both technologies in a flexible way across the manufacturing lifecycle. How this is achieved is in part a function of the technical and economic requirements of any given application. It is also important to remember that advanced manufacturing should not be viewed as a catch-all, and different combinations of production technologies will be relevant at different stages of the production lifecycle.
This approach, which is a counter argument to the ‘fight’ portrayed between AM and IM, is something that we at EOS’ consulting division, Additive Minds, have worked on closely to conceptualise with KraussMaffei, a leading manufacturer of injection moulding machines. Together, we have created a framework to help companies assess the current and future challenges they may face with different aspects of plastics manufacturing, and determine how best to apply and integrate the two process technologies.
The framework will help decision makers choose a suitable plastic processing technology depending on criteria across three categories: technical, economic, and the readiness of their organisation for advanced manufacturing. The output of the framework is a series of graphs, showing which of the following manufacturing scenarios would be appropriate:
- Applying AM for prototyping and switching to IM when the ramp-up phase starts
- AM and IM are both technically suitable for ramp-up and declining phases. Economic criteria determine at which batch size to switch from AM to IM
- A recommendation for a completed AM solution based on the technological and economic criteria provided
- A recommendation for a completed IM solution based on the technological and economic criteria provided
Using the decision-making framework
Finding the most suitable manufacturing technology for an application can be challenging, particularly when trying to work out whether to focus on conventional manufacturing such as Injection Moulding or, for example, industrial Additive Manufacturing.
The decision-making framework that has been developed, is a simple three-step process that will help you select the most suitable manufacturing technology for each application. By completing the assessment table for a given application and lifecycle stage, a set of graphs is produced, which suggest which manufacturing scenario to consider
Step 1 - Assessment of economic and technical criteria
The first step is to assess an application from an economic and technical perspective, by completing the assessment table pictured. Each economic and technical characteristic has a score, which influences the recommendations of the framework, based on their significance.
Economic factors include the size of the series, time to manufacture, whether the product is highly customisable and the lifecycle stage of the product. Technical properties include the part size, surface quality and tolerances required, as well as regulatory requirements and material availability.
Four of the characteristics in the table are highlighted in blue/orange. These are defined as “star characteristics”. Where these characteristics apply it would push the scenario to be either a complete AM or IM solution.
An example of such a scenario is an application with a series size greater than 500k/annum. In that case, the costs of tooling and productivity in IM will outweigh any AM solution in the market. On the other hand, if the application requires mass customisation, then an AM scenario will outweigh the costs of producing multiple tools for customised applications; hence the application will shift to an AM only production scenario.
Step 2 - Rating of a company’s organisational readiness
The final section of the table is the area looking at organisational readiness. Ultimately, this is the most important aspect of the framework, as it defines a company’s ability to evaluate and switch between technologies.
This is important because there would be little point in proposing a combination of technologies that an organisation cannot realistically apply to a given application. To this end, characteristics such as the level of IM knowledge (in-house), the risks of swapping between technologies, and openness to new technology, will influence the scenario proposed by the framework for the same economic and technical criteria. The results from this section of the assessment will place an organisation at one of the following levels:
- Low – The organisation specialises in IM or AM. It has established manufacturing capacities and experience in running the production line.
- Medium – The organisation specialises in IM or AM. Furthermore, it has the knowledge to apply the other technology on a beginner to moderate level. Decisions can be made in favour of one of the two technologies on the basis of a simple break-even analysis.
- High – The organisation specialises in both technologies, and can switch between conventional and modern plastic processing technology seamlessly. It has the necessary knowledge of all materials, in-depth expertise in the processes of both manufacturing technologies and an understanding of available manufacturing output.
Step 3 - Analyzing the results
Once completed the framework provides three graphs based on the level of organisational readiness as outlined in the Whitepaper. By reviewing the different graphs, the impact of organisational readiness can be seen, and highlights how important it is to be honest about the stage at which a manufacturer is on its journey to advanced manufacturing. The final recommendations provide a point of discussion with all stakeholders across the manufacturing process.
Complementary manufacturing technologies
Today, AM and IM production technologies are a key part of the vision for advanced manufacturing. A seamless change between conventional and digital manufacturing technologies depends on the part properties, economic aspects, lifecycle stage and overarching organisational readiness.
By using the step-by-step approach outlined in this article, manufacturers can ease the path of transitioning to advanced manufacturing techniques that combine manufacturing processes. The framework provides you with a tool to ask the right questions and decide whether to use Injection Molding or Additive Manufacturing.