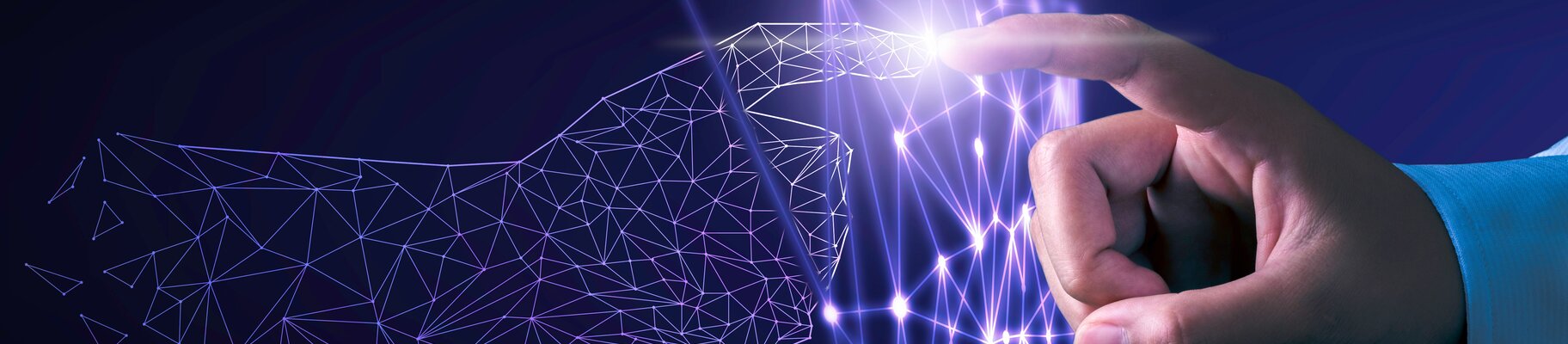
Streamlining Additive Manufacturing Operations with Digital Transformation
March 31, 2021 | Reading time: 2 min
On the latest edition of our Additive Snack podcast, we spoke with Shane Fox — former co-founder and CEO of AM workflow solution provider Link3D (now CO-AM by Materialize) — about the concrete value digital transformation can bring to additive manufacturing.
Digital transformation for the additive environment
Additive manufacturing (AM) has been revolutionary for product and part fabrication. Implementing digital transformation in conjunction with AM can strengthen and streamline additive operations similarly, moving toward new horizons of efficiency, productivity and quality.
Much of additive manufacturing's early history is dominated by excitement about the machines themselves: i.e., what 3D printers and their tangential technologies can produce, what materials are used and so on.
Only in the last few years has the additive manufacturing industry shifted focus to optimizing the machines' operating environments. This includes (but isn't necessarily limited to) sustainably increasing productivity, achieving resource optimization, maintaining quality control and establishing regulatory compliance wherever applicable. Optimizing AM through digital transformation requires this focus on the operating environment.
Shane cites the internet of things (IoT), a staple of many digital transformations, as especially valuable to additive manufacturing because of the operating environment insights it collects. These range from declines in machine health over time to the rate of build failures. All of this data can inform 3D printing at the design stage — helping to determine orientation, parameter settings, material selection and more — and during the build, reducing error rates and accelerating time-to-market.
Abandoning the 'artisanal'
During additive manufacturing's early years, 3D printing was primarily a rapid prototyping method or a technique for low-volume production of specialized components. While its machines and materials have evolved considerably since then, the perception of additive manufacturing as a niche, "artisanal" practice hasn't disappeared.
Now that additive is in the manufacturing mainstream, it's no longer feasible to view it as a delicate process. But while there's little room for an artisanal approach toward the general field, this doesn't mean digital transformation is about replacing people. Their knowledge remains essential. Rather, digitization involves smartly leveraging technologies to give engineers and experts better insights, tools and processes for design, fabrication, QC, regulatory testing and more.
Aligning a team vision for digital transformation
To ensure an optimally digitized additive manufacturing production environment, the digital transformation strategy must stem from a team's aligned vision. Stakeholders covering every vertical of the value chain must be aligned.
Fostering alignment on digitalization-driven additive manufacturing begins with having a specific end goal. Do you aim to achieve true distributed manufacturing and low-volume production? Are you laser-focused on AM sustainability? Do you need to create new geometries for new products (or improve existing products)? Whatever the goal is, it must be uniform among team members, as this will allow you to determine exactly how digital transformation can best serve your needs.
Adopting emerging technologies and optimizing infrastructure
Earlier, we cited IoT as ideal for additive manufacturing's digital transformation. But collecting sensor data is just the tip of the iceberg. You also need the right technology infrastructure to make that data broadly accessible. Cloud computing is critical here. While the manufacturing industry's recent trend away from on-premises and toward cloud-hosted operations is promising, holdouts remain. Your organization can't be among them.
Digitized AM requires organized and integrated infrastructure, allowing for the configuration and scaling of AM operations to match shifting demands, inventory levels and other KPIs. Additionally, this should facilitate the convenient aggregation of data produced by all systems integral to additive operations, ranging from CAD/CAM to predictive maintenance and asset management tools. Ensuring data availability and application integration allows additive manufacturing stakeholders to follow a single vision, ultimately leading to better products and processes.
Listen to Additive Snack now
Learn more about the importance of digital transformation to additive manufacturing on the latest episode of Additive Snack, Digitalization and Additive Manufacturing with Shane Fox. In addition to the subjects detailed above, Shane addresses how organizations can establish reliable strategies for directing the AM production environment in both the short and long term.