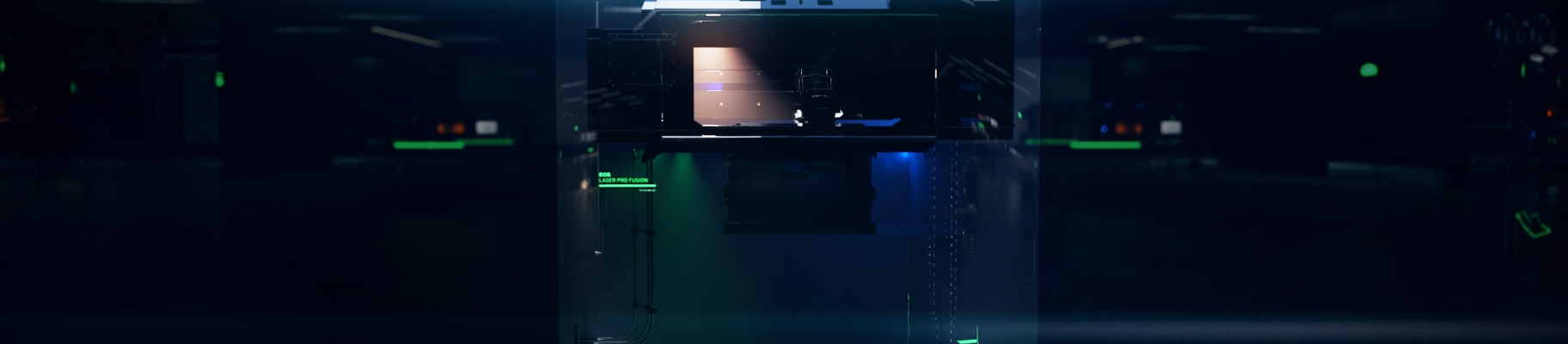
EOS Smart Monitoring
The quality assurance and process monitoring features of EOSTATE Exposure OT — in a comprehensive package together with training, consulting and game-changing features like Smart Fusion.
Ensuring reliable production quality is important to all additive manufacturing (AM) projects and especially so to industrial metal 3D printing. The EOS Smart Monitoring* Plan is the ideal solution.
EOS Smart Monitoring includes all of the end-to-end monitoring capabilities critical for series production, and the cutting-edge automation of Smart Fusion makes a viable business case for more applications.
*requires an active EOS Build Plan
Exposure OT: 100% Insight
Smart Monitoring includes EOSTATE Exposure OT, an ingenious pairing of hardware and software by utilizing optical tomography for process insights.
Smart Fusion: A Game-Changer in Additive Manufacturing
Smart Fusion brings a degree of control to metal 3D printing that even those in the AM industry might not have thought possible just a few years ago.
The automated feature adjusts laser power levels to match the standards established in pre-processing, making corrections during the build as needed. Exposure OT's heat distribution monitoring is critical to the process, as its data informs Smart Fusion's power corrections during the build. Smart Fusion reduces the likelihood of overheating and helps ensure fewer part iterations.Smart Fusion’s benefits improve the entire EOS software landscape. AM designers who know Smart Fusion, can craft part designs optimized for supportless building.

Critical OT Training
Those unfamiliar with utilizing OT for AM monitoring and QA — or who want to strengthen their knowledge of the technology — can learn everything they need via Smart Monitoring's training features. Each Smart Monitoring per-system subscription includes:
- Up to two e-learning seats for basic and advanced OT training, as well as advanced e-learning for Smart Fusion
- Entry to one four-hour expert session for OT technology and one Smart Fusion expert session

Subscription-Based Flexibility
Instead of a prepaid upfront investment in the hardware and software required for EOSTATE, EOS Smart Monitoring users only need to subscribe to a yearly subscription per 3D printing system. (min 2 years at the beginning) If you've purchased a new EOS metal AM system that features preinstalled OT, you can try EOS Smart Monitoring before subscribing. Either way, each EOS Smart Monitoring subscription includes the required hardware.
The subscription model gives EOS Smart Monitoring customers the freedom to scale their usage as needed. If Smart Fusion isn't required for your business after your initial commitment, you can deactivate it, and potentially opt back in at a later date if operational demands change.
Inactive EOS Smart Monitoring users retain the OT hardware and some Exposure OT functionality (e.g., access to historical OT data). However, they lose access to certain critical features — notably, the ability to record real-time OT data and analyze it on the fly. Also, inactive subscribers will no longer have access to training resources and Smart Fusion (which relies upon live data from Exposure OT to serve its key purpose).
Downloads
-
EOS Software Plans - Features Comparison (English)
PDF 948,94 kB -
Customer Guide - Software and Process Plans (English)
PDF 385,40 kB
Monitoring Data and Mechanical Properties of Lattice Structures
The monitoring system EOSTATE Exposure OT can be used to assess the relative density and compression strength of lattice structures. Any decrease in energy density that results in a lower EOSTATE Exposure OT value leads to a decrease in strut thickness and therefore a lower relative density.
This whitepaper gives information about:
- Producing or planning on producing porous structures by means of additive manufacturing
- Assessing mechanical properties of lattice structures during the build
- State-of-the-art alternatives to cost-intensive quality assurance methods

Monitoring Data and Defects in X-Ray CT for AM Swirler
The EOSTATE Exposure OT monitoring system can be used to identify defects. This study shows that process instability can be reflected as extreme hot spots, which can be detected by the monitoring system.
This whitepaper gives information about:
- The assessment of the sensitivity of EOSTATE Exposure OT and EOSTATE MeltPool monitoring system in registering variations in melt pool energy density when processing EOS NickelAlloy IN625 on EOS M 290
- The correlation of defects based on in-process monitoring data and CT scanning
- The application of in-process monitoring for quality assurance in a serial production scenario
