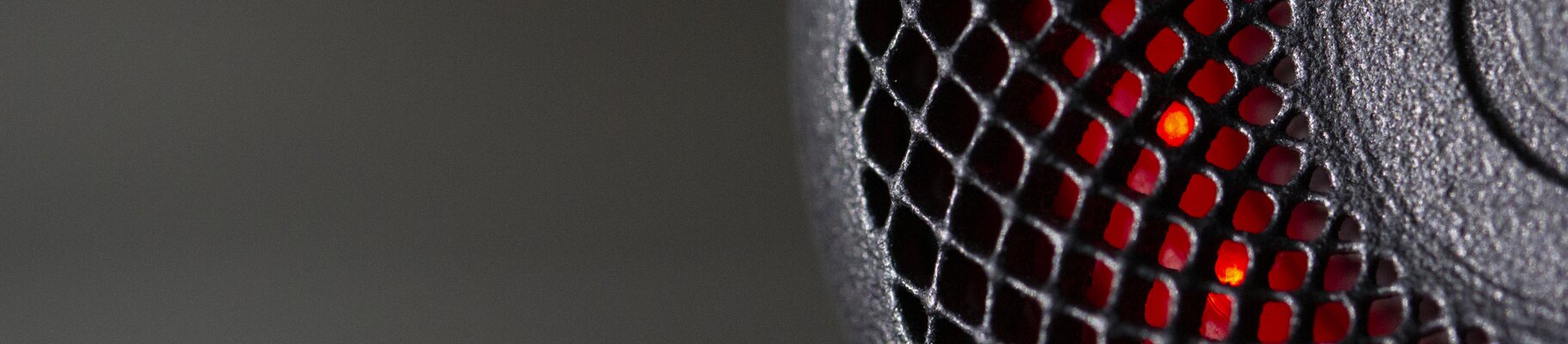
Fine Detail Resolution
Industrial 3D Printing
Highly Accurate, Delicate & Complex, Ultra-thin
Sharp Laser with Stable Material
The perfect match for parts with high detail resolution
Fine detail resolution (FDR) technology is the only solution in the 3D printing market that enables production of fine detail without sacrificing quality. The one-of-a-kind CO laser has an ultra-fine beam half the size of standard selective laser sintering (SLS) systems. Combined with PA 11, a remarkably flexible and lightweight polymer material, it produces rigid parts with a high detail resolution and smooth surface finish.
How does fine detail resolution benefit the 3D printing process?
- The 3D printing resolution with FDR technology enables the reliable production of incredibly accurate and stable parts with complex structures, tiny holes, and detail. Achieve remarkable dimensional accuracy of up to +/- 40 µm with FDR technology.
- Part complexity isn’t a cost driver. With our flexible 3D printing material, even the finest image detail from your models will translate to every printed part.
- No support structures or UV light for post-curing needed, allowing for significantly reduced post-processing times.
- The manufactured parts have a minimum wall thickness of up to 0.22 mm, ultra-smooth surfaces, and extreme edge sharpness.
- Thanks to the excellent mechanical properties of PA 1101, each 3D printed part is flexible, dimensionally stable, and light.
- FDR’s multi-level vertical part nesting increases production efficiency.
- FDR makes for strong UV, chemical, and high-temperature resistance, improving the longevity of each 3D printed part.
- Parts can be customized to the user, object of utility, and desired functionality at no additional cost.
- The smooth surface roughness allows for optimal metallization or other post-processing steps.
Watch our on-demand webinar
Learn how to unleash the power of FDR 3D printing to diversify your application portfolio.

"The new technology combines the best of two worlds: the high detail resolution of stereolithography and the durability and quality of powder-based industrial 3D printing."
Virginia Palacios | Chief Business Officer Polymer Solutions | EOS GmbH
What is FDR used for?
Insight into revolutionary fine detail resolution applications
The technology was developed to produce high-precision components to open entirely new product fields manufactured with plastics-based additive manufacturing (AM). Applications range from filter units and fluid guides to electronic components. Additionally, the material is immune to elevated ambient temperatures, which expands the application areas and allows for live-operation testing.