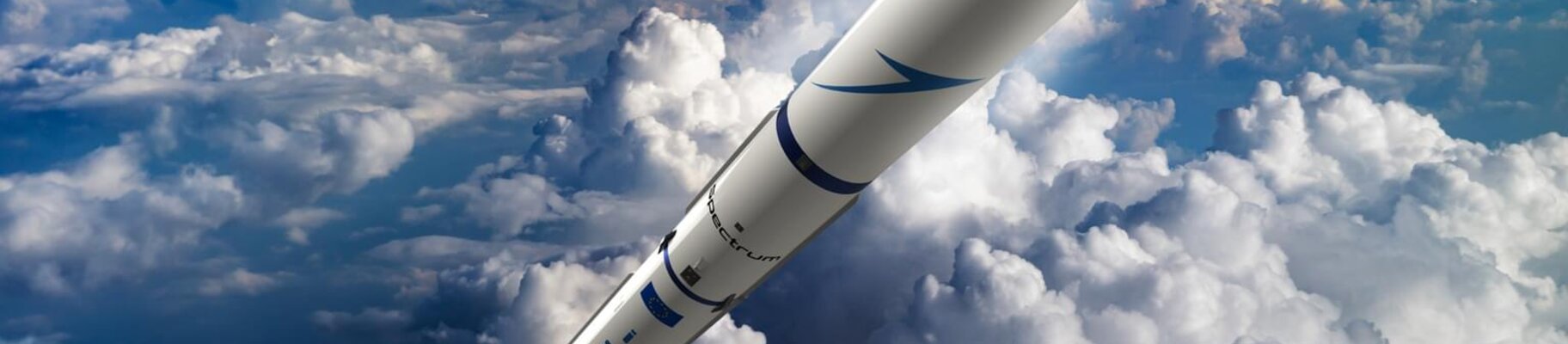
Additive Manufacturing for European New Space
January 16, 2023 | Reading time: 5 min
The New Space industry, since its inception, was strongly U.S.-centric, but with the emergence of new technologies and private organizations invested in the new space industry, that geographical focus has widened to incorporate more of the world. In this article we will explore the globalization of New Space with frontier technologies, such as additive manufacturing and Europe’s growing role.
The advance of New Space in Europe
The original space race saw countries pitted against each other to be the first out of the atmosphere, the first to land on the moon, etc. But with New Space, those national borders are beginning to tumble. The space industry is no longer just a venture for governmental institutions to pursue but independent companies are gradually beginning to occupy more of the industry, bringing with them the expertise, pioneering spirit, massive amounts of private funding and venture capital, and (literally) out of the world ambitions. There have been many technical breakthroughs driving this New Space wave like advanced manufacturing technologies, miniaturizations of satellite and its components, reusable launch systems, laser-based communication devices, laser-based ignition and artificial intelligence.
Collectively, Europe has one of the most advanced space infrastructures, with many government and private operations contributing to the advancement of the space industry. This shouldn’t come as much of a surprise, since the industrial, scientific, and academic excellence of these nations has kept pushing the boundaries of technology for decades. As many of these developments – such as additive manufacturing- have a direct and highly beneficial applications when it comes to space exploration, and with such a strong space exploration history and relevant infrastructure— it’s a logical step for Europe to get involved and play a key role in the NewSpace Industry and its future.
The European — and particularly German — market for New Space players is growing. The “new” ambition and enthusiasm of New Space ignited by the visionary entrepreneurship of fledging startups entering the industry has also reached Europe in the last few years. There have been several very solid companies like Isar Aerospace, HyImpulse, and Rocket Factory in Germany, Orbex and Skyrora in Great Britain, as well as PLD Space and Pangea Aerospace in Spain.
EOS has partnered with big space companies and start-ups globally, as their proof of concept (POC) enablement partner and as well as provider of reliable serial AM solutions, including customizing the AM solution to the industry’s specific needs. EOS’ central contribution has been to improve the New Space player’s access to the manufacturing technology essential to realize and manufacture their ambitious concepts in a fast, reliable, and cost-effective manner, while meeting their performance targets.
This entrepreneurial spirit typical for New Space has also been fostered by the European Space Agency (ESA) via ESA Space Solutions, consisting of a network of numerous BICs (Business Incubation Centers) across Europe. Here are two excellent examples of New Space organizations and projects currently thriving out of Europe and how additive manufacturing has been a significant contributor to their development:
ESA’s Prometheus
The Ariane Group, French National Center for Space Studies (CNES) and the ESA are working together on the PROMETHEUS project — a series of new liquid rocket engines designed with low cost, flexibility and reusability at the core of the project. The aim of the project is to design, produce and test an advanced 100-ton class liquid oxygen (LOx) and methane (LCH4) engine. This engine is being designed to be reusable to reduce cost and environmental impact. It’s also intended to be flexible in operation with variable thrusts and multiple ignition settings to allow for more comprehensive use for different launch types.
Previously, few rocket engine parts with a main functional and structural role have been made using additive manufacturing. The PROMETHEUS project aims to change this to use AM’s design flexibility and reduced production time. Up to 70% of (engine weight) in PROMETHEUS project is intended to be built with additive manufacturing. The intended result is to optimize processes that encourage the rapid production of low-cost engine components, while reducing the number of parts, speeding up production and reducing wastage. One strong example of how additive manufacturing is evolving the components in this project is Ariane’s mono-shaft turbo pump, which has been designed and produced specifically for the PROMETHEUS engines. These efforts will lead to a massive cost & complexity reduction for launches and there by enabling the European space industry to become internationally more competitive.
Isar Aerospace
One of the prominent success stories emerging from ESA BIC Bavaria has been the Munich-based Isar Aerospace Technologies GmbH, named after the Isar river that runs through Munich. Isar Aerospace is working towards making space access more flexible and affordable for small and medium satellites, as well as satellite constellations. Isar’s Spectrum launcher has been developed entirely in-house, using a combination of advanced materials, and technologies. One of Isar’s aims is to lower rocket launch emissions drastically by replacing conventional toxic rocket fuels with their hydrocarbon mixtures. To this end, Isar aims to build the first high-performance LOX/Hydrocarbon engine as an alternative to toxic fuel engines. Isar Aerospace is currently testing the first of its rockets, and enroute to securing its first launch in 2023.
Additive manufacturing has played a central role in Isar Aerospace’s successful development of both the Spectrum launcher and engine - one that EOS has been directly involved with. When the company’s requirements for additive manufacturing exceeded what could be accomplished with “standard” machines, Isar Aerospace partnered with EOS and AMCM to create a bespoke machine that allows them to utilize additive manufacturing exclusively in-house and push the boundaries of what can be achieved. For Isar Aerospace, additive manufacturing provides the perfect balance of malleability and progression. It allows the development of complex geometries that can reach their ambitious performance targets quickly, meeting challenging deadlines throughout the prototyping and manufacturing process, as well as assuring the higher delivery volume of parts during ramp up.
Additive Manufacturing has directly addressed the reduction of complexity cost in the Space industry, by optimizing the heaviest, longest lead time requiring, most complex and expensive parts like the Thrust Chamber Assembly. This has required application specific system and process customization, which was enabled by EOS and AMCM. The AMCM M 450 and EOS M 290 play a key role in this effort.
The AMCM M 450 has already established itself in the New Space supply chain as a reliable system for mission critical parts, with one of the largest installed base. It enables a large building volume of 450 x 450 x 400 mm with powder handling option for manual or semi-automatic operation.
The EOS M 290 is renowned for its robust system design and powerful 400-watt fiber laser that delivers reliable high performance day after day. With its mid-sized build and multi-talented approach, the EOS M 290 is the industry standard for qualified 3D printed metal parts, ensuring that Isar Aerospace continues to push the boundaries of innovation in space technology.
"When we wanted to enhance our additive manufacturing processes, we chose to use the AMCM M 450. This stable machine from EOS, which - thanks to the customization done by AMCM - can now provide the necessary build space demanded by our engine design. We want to achieve a high utilization of the machines, so the non-utilization time between print jobs is an important parameter that must be reduced. Specifically, I'm thinking of fully automatic powder management (i.e., suction, sieving and refilling), which we are working on with AMCM to determine more effective results."
Christian Wenzl, Head of Manufacturing at Isar Aerospace
Shaping the future of New Space
Additive manufacturing has been a significant enabler for the design and production of parts in the New Space industry. It has empowered companies to continually improve production processes and the capabilities of parts made, but to fully capitalize on these developments, they need to be integrated with other technologies.
The next generation of launchers, engines and modules from New Space companies will be fundamentally enabled by the continued evolution of technologies such as digital design, artificial intelligence, new materials and manufacturing methods, like additive manufacturing. The upstream applications of the New Space industry are strongly growing, in addition to the mega satellite constellations like Starlink by SpaceX or Kuiper by Amazon, recently the EU has announced its own constellation IRIS². As more companies emerge across Europe specializing in space and related industries the future of space is undeniably a global one.
Author: Vinu Vijayan